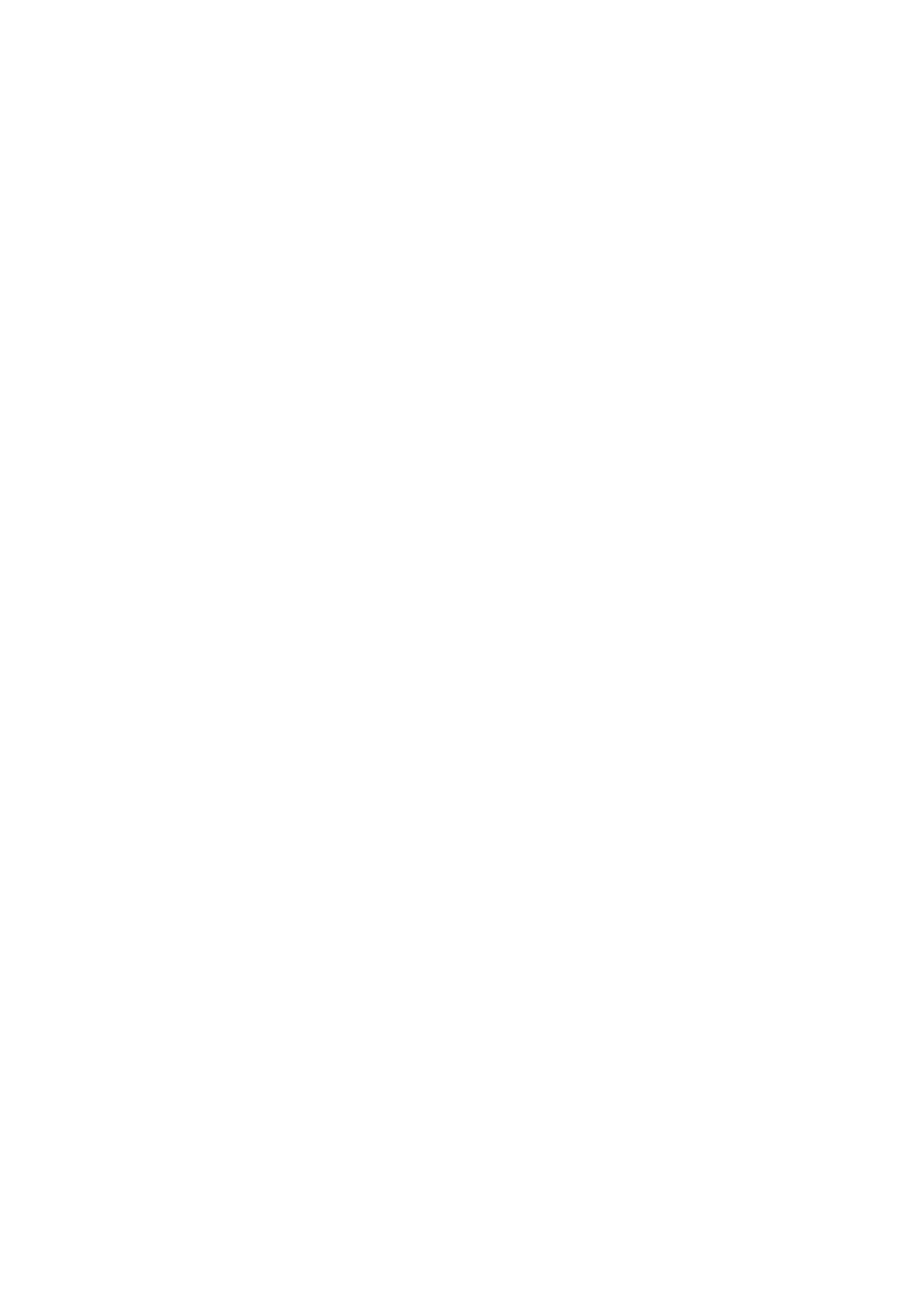
CONTENTS
HE-800A
1 . MECHANICAL DESCRIPTIONS ・・・・・・・・・・・・・・・・・・・
・・・・・・・・・・・・・・・・・・・・・・・・・・・・・・・・・・・・・・
・・・・・・・・・・・・・・・・・・・ 1
1-1 . Needle bar and thread take-up
mechanisms ・・・・・・・・・・・・・・・・・・・・・・・・・・・・・・・・・・・1
1-2 . Upper shaft, lower shaft and rotary hook
mechanisms ・・・・・・・・・・・・・・・・・・・・・・・・・・・・・・・・・・・2
1-3 . Needle zigzag mechanism ・・・・・・・・・・・・・・・・・・・・・・3
1-4 . Presser foot lifter mechanism ・・・・・・・・・・・・・・・・・・・・4
1-5 . Feed mechanism ・・・・・・・・・・・・・・・・・・・・・・・・・・・・・・・5
1-6 . Cutter mechanism ・・・・・・・・・・・・・・・・・・・・・・・・・・・・・・6
1-7 . Thread breakage detection mechanism ・・・・・・・・・・7
1-8 . Lubrication mechanism・・・・・・・・・・・・・・・・・・・・・・・・・・8
1-8-1 . Lower shaft and rotary hook lubrication ・・・・・・・9
1-9 . Tension release mechanism ・・・・・・・・・・・・・・・・・・・ 10
1-10 . Upper thread trimmer mechanism ・・・・・・・・・・・・ 12
1-10-1 . Upper thread scissors・・・・・・・・・・・・・・・・・・・・ 14
1-11 . Lower thread trimmer mechanism・・・・・・・・・・・・・ 16
2 . DISASSEMBLY ・・・・・・・・・・・・・・・・・・・・・・・・・・・・・・・・
・・・・・・・・・・・・・・・・・・・・・・・・・・・・・・・・・・・・・・・・・・・・・・・・・・・・・・・・・・・・・・・・
・・・・・・・・・・・・・・・・・・・・・・・・・・・・・・・・・・
・・・・
・・19
2-1 . Covers ・・・・・・・・・・・・・・・・・・・・・・・・・・・・・・・・・・・・・・・ 19
2-2 . Rotary hook mechanism ・・・・・・・・・・・・・・・・・・・・・・ 20
2-3 . Lubrication mechanism (1)・・・・・・・・・・・・・・・・・・・・・ 21
2-3-1 . Rotary hook lubricating mechanism ・・・・・・・・ 21
2-3-2 . Plunger pump mechanism ・・・・・・・・・・・・・・・・ 22
2-3-3 . Oil terminal mechanism ・・・・・・・・・・・・・・・・・・・ 23
2-3-4 . Needle zigzag mechanism ・・・・・・・・・・・・・・・・ 24
2-3-5 . Shaft bush mechanism ・・・・・・・・・・・・・・・・・・・・ 24
2-4 . Thread breakage detection mechanism ・・・・・・・・ 25
2-5 . Upper thread trimmer mechanism ・・・・・・・・・・・・・・ 26
2-6 . Presser bar mechanism ・・・・・・・・・・・・・・・・・・・・・・・ 28
2-7 . Needle bar and thread take-up
mechanism (1) ・・・・・・・・・・・・・・・・・・・・・・・・・・・・・・・ 29
2-8 . Needle bar and thread take-up
mechanism (2) ・・・・・・・・・・・・・・・・・・・・・・・・・・・・・・・ 30
2-9 . Lubrication mechanism (2)・・・・・・・・・・・・・・・・・・・・・ 31
2-9-1 . Oil tubes ・・・・・・・・・・・・・・・・・・・・・・・・・・・・・・・・・ 31
2-10 . Upper shaft and tension pulley
mechanisms ・・・・・・・・・・・・・・・・・・・・・・・・・・・・・・・・ 32
2-11 . Cutter mechanism (1) ・・・・・・・・・・・・・・・・・・・・・・・・ 33
2-12 . Cutter mechanism (2) ・・・・・・・・・・・・・・・・・・・・・・・・ 34
2-13 . Needle zigzag mechanism ・・・・・・・・・・・・・・・・・・・ 35
2-14 . Presser lifter mechanism (1) ・・・・・・・・・・・・・・・・・・ 36
2-15 . Presser lifter mechanism (2) ・・・・・・・・・・・・・・・・・・ 37
2-16 . Presser lifter mechanism (3) ・・・・・・・・・・・・・・・・・・ 38
2-17 . Tension release mechanism (1) ・・・・・・・・・・・・・・・ 39
2-18 . Tension release mechanism (2) ・・・・・・・・・・・・・・・ 40
2-19 . Bobbin presser mechanism ・・・・・・・・・・・・・・・・・・ 41
2-20 . Feed mechanism (1) ・・・・・・・・・・・・・・・・・・・・・・・・・ 42
2-21 . Feed mechanism (2) ・・・・・・・・・・・・・・・・・・・・・・・・・ 44
2-22 . Lower thread trimmer mechanism (1) ・・・・・・・・・ 45
2-23 . Lower thread trimmer mechanism (2) ・・・・・・・・・ 46
2-24 . Lower shaft and idle pulley
mechanisms・・・・・・・・・・・・・・・・・・・・・・・・・・・・・・・・・ 47
3 . ASSEMBLY ・・・・・・・・・・・・・・・・・・・・・・・・・・・・・・・・
・・・・・・・・・・・・・・・・・・・・・・・・・・・・・・・・・・・・・・・・・・・・・・・・・・・・・・・・・・・・・・・・
・・・・・・・・・・・・・・・・・・・・・・・・・・・・・・・・・・・・・・
・・・・・・・・・・・・
・・・・・・48
3-1 . Lower shaft and idle pulley mechanisms ・・・・・・・・ 48
3-2 . Lower thread trimmer mechanism (1) ・・・・・・・・・・・ 49
3-3 . Lower thread trimmer mechanism (2) ・・・・・・・・・・・ 50
3-4 . Feed mechanism (1) ・・・・・・・・・・・・・・・・・・・・・・・・・・ 51
3-5 . Feed mechanism (2) ・・・・・・・・・・・・・・・・・・・・・・・・・・ 53
3-6 . Bobbin presser mechanism ・・・・・・・・・・・・・・・・・・・・ 54
3-7 . Tension release mechanism (1) ・・・・・・・・・・・・・・・・ 55
3-8 . Tension release mechanism (2) ・・・・・・・・・・・・・・・・ 56
3-9 . Presser lifter mechanism (1)・・・・・・・・・・・・・・・・・・・・ 57
3-10 . Presser lifter mechanism (2) ・・・・・・・・・・・・・・・・・・ 58
3-11 . Presser lifter mechanism (3) ・・・・・・・・・・・・・・・・・・ 59
3-12 . Needle zigzag mechanism・・・・・・・・・・・・・・・・・・・・ 60
3-13 . Cutter mechanism (1) ・・・・・・・・・・・・・・・・・・・・・・・・ 61
3-14 . Cutter mechanism (2) ・・・・・・・・・・・・・・・・・・・・・・・・ 62
3-15 . Upper shaft and tension pulley
mechanism・・・・・・・・・・・・・・・・・・・・・・・・・・・・・・・・・・ 64
3-16 . Lubrication mechanism (1)・・・・・・・・・・・・・・・・・・・・ 65
3-16-1 . Oil tubes・・・・・・・・・・・・・・・・・・・・・・・・・・・・・・・・・ 65
3-17 . Needle bar and thread take-up
mechanisms (1) ・・・・・・・・・・・・・・・・・・・・・・・・・・・・・ 66
3-18 . Needle bar and thread take-up
mechanisms (2) ・・・・・・・・・・・・・・・・・・・・・・・・・・・・・ 67
3-19 . Presser bar mechanism ・・・・・・・・・・・・・・・・・・・・・・ 68
3-20 . Upper thread trimmer mechanism ・・・・・・・・・・・・・ 69
3-21 . Thread breakage detection mechanism・・・・・・・・ 71
3-22 . Lubrication mechanism (2)・・・・・・・・・・・・・・・・・・・・ 72
3-22-1 . Shaft bush mechanism ・・・・・・・・・・・・・・・・・・・ 72
3-22-2 . Needle zigzag mechanism ・・・・・・・・・・・・・・・ 73
3-22-3 . Oil terminal mechanism ・・・・・・・・・・・・・・・・・・ 74
3-22-4 . Plunger pump mechanism・・・・・・・・・・・・・・・・ 75
3-22-5 . Rotary hook lubrication mechanism ・・・・・・・ 76
3-23 . Rotary hook mechanism・・・・・・・・・・・・・・・・・・・・・・ 77
3-24 . Covers ・・・・・・・・・・・・・・・・・・・・・・・・・・・・・・・・・・・・・・ 77
4 . ADJUSTMENT ・・・・・・・・・・・・・・・・・・・・・・・・・・・・・・・・
・・・・・・・・・・・・・・・・・・・・・・・・・・・・・・・・・・・・・・・・・・・・・・・・・・・・・・・・・・・・・・・・
・・・・・・・・・・・・・・・・・・・・・・・・・・・・・・・・・・・
・・・・・・
・・・78
4-1 . Notes on making adjustments ・・・・・・・・・・・・・・・・・・ 78
4-2 . Adjusting the needle zigzag home position
sensor position ・・・・・・・・・・・・・・・・・・・・・・・・・・・・・・・・ 80
4-3 . Adjusting the feed home position
sensor position ・・・・・・・・・・・・・・・・・・・・・・・・・・・・・・・・ 81
4-4 . Adjusting the work clamp home position
sensor position ・・・・・・・・・・・・・・・・・・・・・・・・・・・・・・・・ 82
4-5 . Adjusting the needle bar height ・・・・・・・・・・・・・・・・・ 83
4-6 . Adjusting the needle and hook timing ・・・・・・・・・・・ 83
4-6-1 . Adjusting the clearance between
needle and hook point ・・・・・・・・・・・・・・・・・・・・・ 84