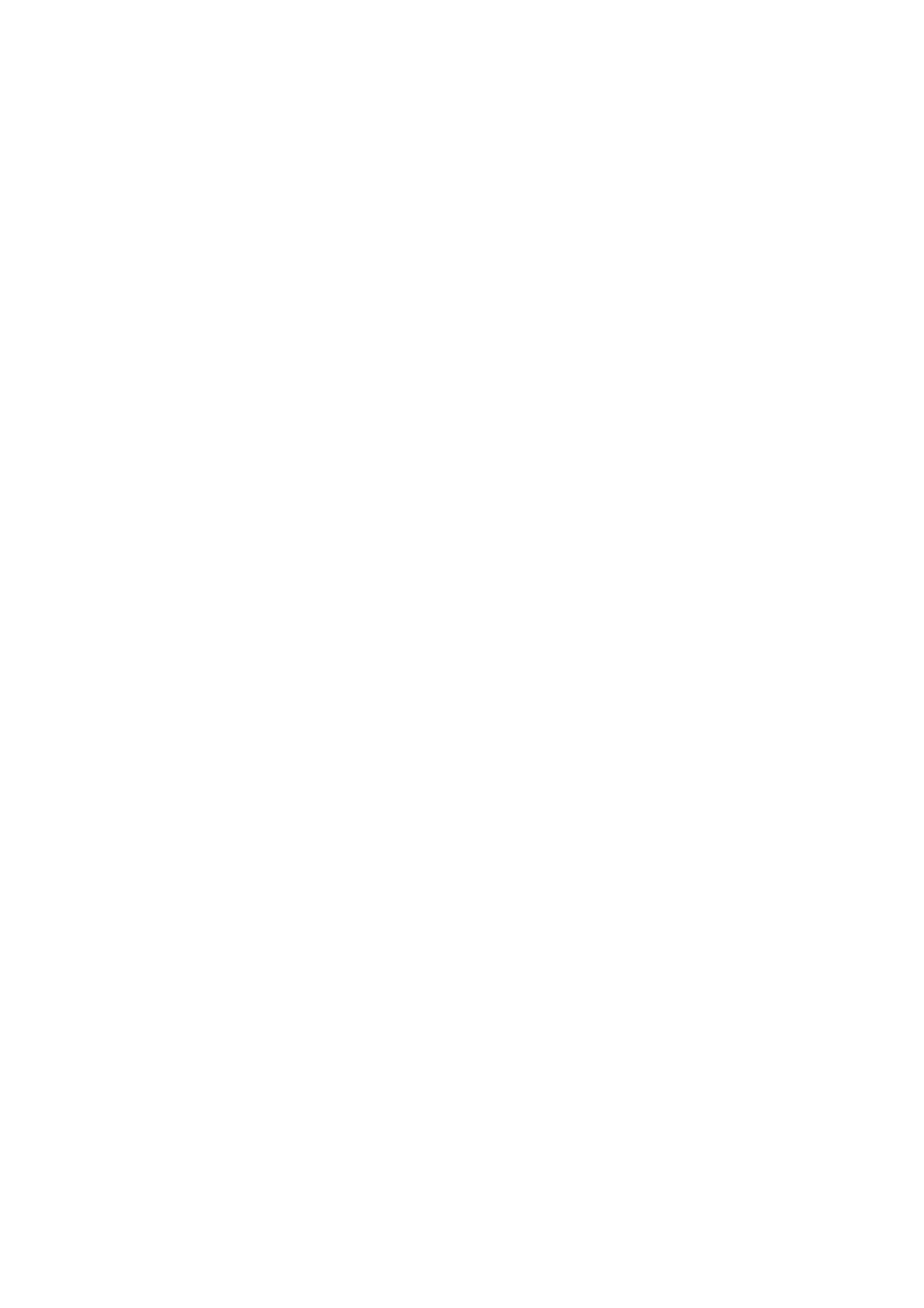
INDEX
1
GENERAL............................................................................................................................................................................................................3
1.1
SHELTER........................................................................................................................................................................................................3
1.2
THE PROGRAM.............................................................................................................................................................................................3
1.3
SETTING UP THE pLAN NETWORK ..........................................................................................................................................................4
2
LIST OF CONFIGURATIONS.............................................................................................................................................................................5
2.1
DIGITAL INPUTS ..........................................................................................................................................................................................5
2.2
ANALOGUE INPUTS.....................................................................................................................................................................................5
2.3
DIGITAL OUTPUTS.......................................................................................................................................................................................5
2.4
ANALOGUE OUTPUTS.................................................................................................................................................................................5
3
TEMPERATURE CONTROL..............................................................................................................................................................................6
3.1
SHELTER........................................................................................................................................................................................................6
3.2
OTHER TEMPERATURE FUNCTIONS .......................................................................................................................................................7
3.3
HUMIDITY CONTROL..................................................................................................................................................................................7
3.4
OTHER HUMIDITY FUNCTIONS................................................................................................................................................................8
4
OUTLET LIMITATION.......................................................................................................................................................................................8
5
OUTLET FAN......................................................................................................................................................................................................9
6
CONDENSER FANS............................................................................................................................................................................................9
6.1
NUMBER OF PROBES AND CONDENSING COILS................................................................................................................................10
6.2
PREVENT FUNCTION.................................................................................................................................................................................10
6.3
SPEED-UP FUNCTION................................................................................................................................................................................10
6.4
PRESSURE – TEMPERATURE CONVERSION.........................................................................................................................................10
7
COMPRESSORS ................................................................................................................................................................................................11
7.1
ROTATION...................................................................................................................................................................................................11
7.2
TIMES ...........................................................................................................................................................................................................11
7.3
COMPRESSOR ALARMS............................................................................................................................................................................11
8
HEATERS...........................................................................................................................................................................................................12
8.1
HEATER ALARMS ......................................................................................................................................................................................12
9
FREECOOLING.................................................................................................................................................................................................13
9.1
HUMIDITY CONTROL IN FREECOOLING..............................................................................................................................................13
9.2
0-10Volt MODULATING DAMPER............................................................................................................................................................13
9.3
FREECOOLING CONTROLLED BY DIGITAL OUTPUTS ......................................................................................................................13
10
MANUAL OPERATION OF THE DEVICES....................................................................................................................................................14
11
AUTOMATIC ROTATION BETWEEN DIFFERENT SHELTER UNITS IN A pLAN...........................................................................................14
11.1
CRITICAL SITUATIONS........................................................................................................................................................................14
11.2
FORCING.................................................................................................................................................................................................14
11.3
FIXED TIME ROTATION.......................................................................................................................................................................14
12
ALARMS............................................................................................................................................................................................................15
12.1
ALARM RELAY......................................................................................................................................................................................16
12.2
SUMMARY ALARM TABLE.................................................................................................................................................................16
13
ALARM LOG.....................................................................................................................................................................................................17
13.1
BASIC LOG (pCO1 only if the clock card is installed – pCO2) ..............................................................................................................17
13.2
ADVANCED LOG (pCO2)......................................................................................................................................................................17
14
LIST OF PARAMETERS AND DEFAULT VALUES......................................................................................................................................21
15
SCREENS...........................................................................................................................................................................................................25
15.1
LIST OF THE SCREENS.........................................................................................................................................................................25
16
SUPERVISION...................................................................................................................................................................................................27
16.1
CAREL SUPERVISOR............................................................................................................................................................................27
16.2
BMS..........................................................................................................................................................................................................27
16.3
GSM PROTOCOL....................................................................................................................................................................................27
16.4
GSM VARIABLE DATABASE ..............................................................................................................................................................27
16.5
SUPERVISOR VARIABLE DATABASE...............................................................................................................................................28
17
ELECTRONIC EXPANSION VALVE..............................................................................................................................................................31
18
THE USER TERMINAL ....................................................................................................................................................................................32
18.1
EXTERNAL DISPLAY............................................................................................................................................................................32
18.2
BUILT-IN DISPLAY ...............................................................................................................................................................................32
19
MANAGING THE CONNECTION BETWEEN BOARDS (pLAN).................................................................................................................33
19.1
ASSIGNING THE ADDRESSES.............................................................................................................................................................33