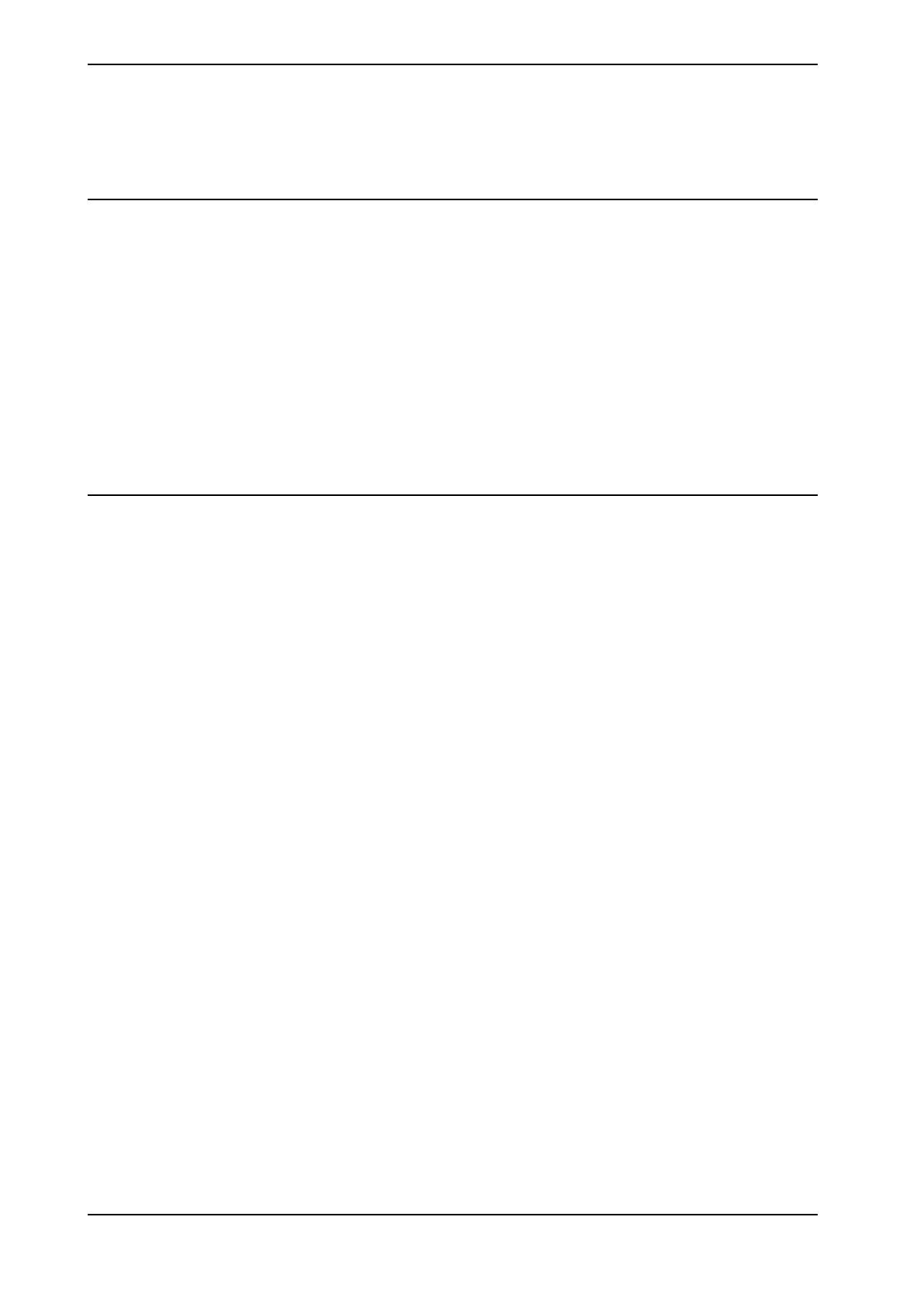
1262.6 Start of robot in cold environments ......................................................................
1273 Maintenance
1273.1 Introduction ......................................................................................................
1283.2 Maintenance schedule and expected component life ...............................................
1283.2.1 Specification of maintenance intervals ........................................................
1293.2.2 Maintenance schedule .............................................................................
1313.2.3 Expected component life ..........................................................................
1323.3 Inspection activities ...........................................................................................
1323.3.1 Inspection, damper axes 2, 3 and 5 .............................................................
1353.3.2 Inspecting information labels .....................................................................
1373.4 Replacement activities .......................................................................................
1373.4.1 Type of lubrication in gearboxes ................................................................
1383.4.2 Changing the oil in axes 5 and 6 gearboxes .................................................
1413.4.3 Changing the oil in axes 5 and axis 5 and 6 gearboxes, IRB 1600ID/1660ID ........
1443.4.4 Replacing the battery pack ........................................................................
1493.5 Cleaning activities .............................................................................................
1493.5.1 Cleaning the IRB 1600/1660ID ...................................................................
1534 Repair
1534.1 Introduction ......................................................................................................
1544.2 General procedures ...........................................................................................
1544.2.1 Performing a leak-down test ......................................................................
1554.2.2 Mounting instructions for bearings .............................................................
1574.2.3 Mounting instructions for seals ..................................................................
1594.2.4 Cut the paint or surface on the robot before replacing parts ............................
1614.2.5 The brake release buttons may be jammed after service work .........................
1624.3 Complete manipulator ........................................................................................
1624.3.1 Replacing the cable harness, IRB 1600 .......................................................
1724.3.2 Replacing the cable harness, 1600ID/1660ID ................................................
1784.3.3 Replacement of complete arm system .........................................................
1834.4 Upper and lower arm .........................................................................................
1834.4.1 Replacing the complete upper arm, IRB 1600 ...............................................
1884.4.2 Replacing the complete upper arm, IRB 1600ID/1660ID ..................................
1964.4.3 Replacing the complete lower arm ..............................................................
2014.4.4 Replacing the wrist unit, IRB 1600 ..............................................................
2064.4.5 Replacing the wrist unit, IRB 1600ID ...........................................................
2124.4.6 Replacing the wrist unit, IRB1660ID ............................................................
2204.4.7 Replacing the damper, axis 2 .....................................................................
2224.4.8 Replacing the damper, axis 3 .....................................................................
2244.4.9 Replacing the mechanical stop axis 3, IRB 1600ID/1660ID ..............................
2264.4.10 Replacement of damper, axis 5 ..................................................................
2284.4.11 Remove upper arm AW Gun ......................................................................
2334.4.12 Measuring the play 1600ID/1660ID, axis 5 ....................................................
2364.4.13 Measuring the play 1600ID/1660ID, axis 6 ....................................................
2394.5 Frame and base ................................................................................................
2394.5.1 Replacement of base ...............................................................................
2444.5.2 Replacing the serial measurement unit ........................................................
2514.5.3 Replacing the push button unit ..................................................................
2574.6 Motors ............................................................................................................
2574.6.1 Replacement of motor, axis 1 ....................................................................
2624.6.2 Replacement of motor, axis 2 ....................................................................
2684.6.3 Replacement of motor, axis 3, IRB 1600 ......................................................
2734.6.4 Replacement of motor, axis 3, 1600ID/1660ID ...............................................
2794.6.5 Replacement of motor, axis 4, IRB 1600 ......................................................
2844.6.6 Replacement of motor, axis 4, 1600ID/1660ID ...............................................
2884.6.7 Replacement of motor and timing belt, axis 5, IRB 1600 .................................
2944.6.8 Replacement of motor, axis 5, IRB 1600ID ...................................................
3024.6.9 Replacement of motor, axis 5, IRB 1660ID ...................................................
6 Product manual - IRB 1600/1660
3HAC026660-001 Revision: W
© Copyright 2006-2018 ABB. All rights reserved.
Table of contents