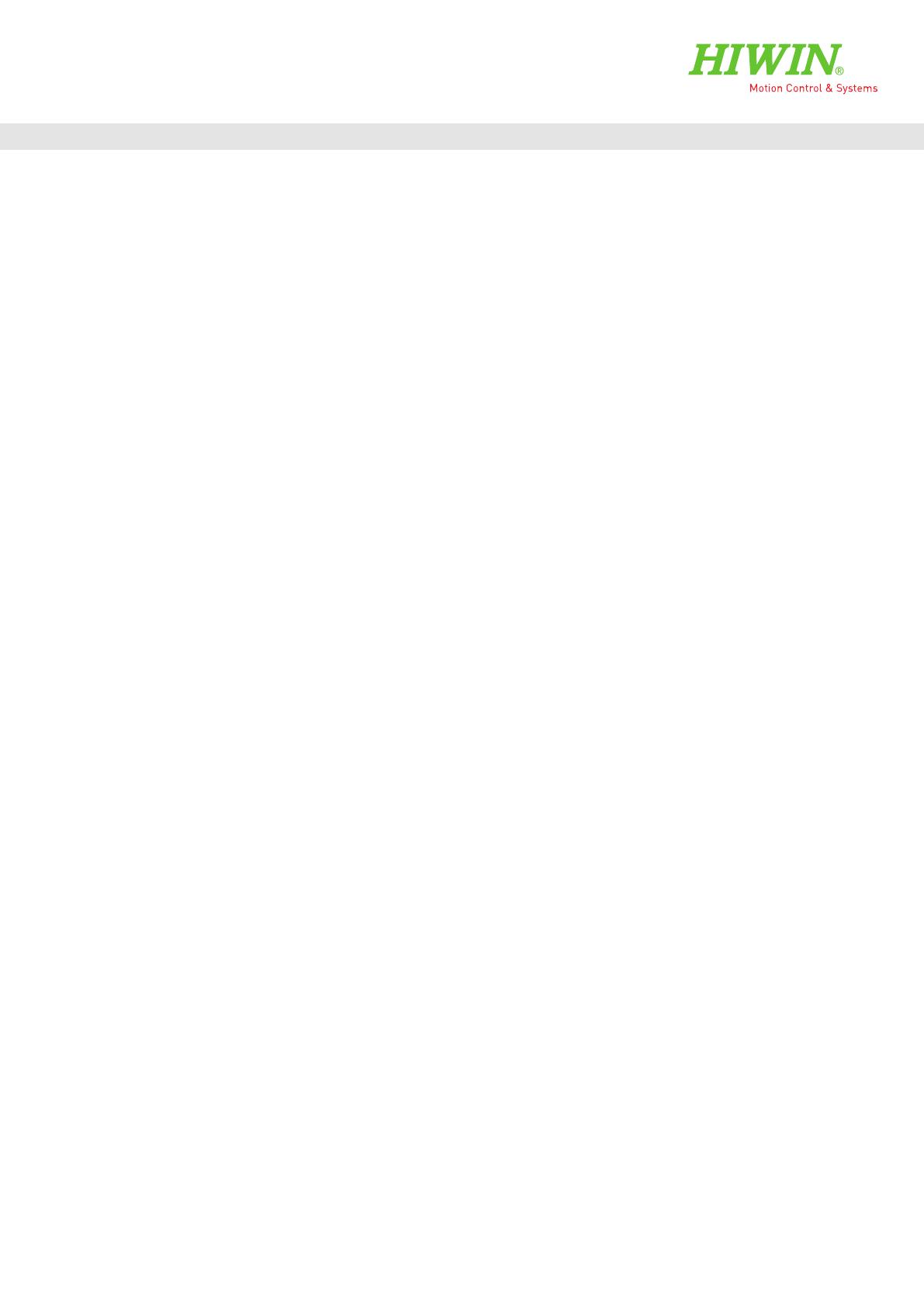
Assembly and Commissioning Instructions
D1-N Servo Drive Amplifier
D1N-02-4-EN-1709-MA
Contents
Contents
1. General information ........................................................4
1.1 Information about the document 4
1.2 Depictions used in these assembly instructions 5
1.3 Warranty and liability 7
1.4 Manufacturer’s details 7
1.5 Copyright 7
1.6 Product monitoring 7
2. Basic safety notices ........................................................8
2.1 Intended use 8
2.2 Disclaimer in the event of modification or improper use 8
2.3 Qualified trained staff 8
2.4 General safety notices 9
2.5 HIWIN technical support 10
2.6 Labels on D1-N servo drive amplifier 10
3. Product description .......................................................11
3.1 Order code 11
3.2 Type plates 12
3.3 Guidelines and standards 13
3.4 Scope of supply 13
3.5 Technical specification 14
4. Assembly .....................................................................16
4.1 Assembling the drive amplifier 16
4.2 Dimensions 16
4.3 Switch cabinet assembly 18
5. Electrical connection.....................................................19
5.1 Overview of electrical connections 19
5.2 X1 – mains connection 21
5.3 X2 – Brake resistor connection 22
5.4 X3 – motor connection 26
5.5 X4 – control voltage and motor brake connection 26
5.6 X5 – parameterisation interface 27
5.7 X6 – input and output connection 28
5.8 X7 and X8 – STO safety function connection 32
5.9 X9 – motor temperature sensor 32
5.10 X10, X11, X12 – encoder connection 33
5.11 X13 – EtherCAT 34
6. STO safety function ....................................................... 35
6.1 Definition STO 35
6.2 Functional principle of the STO function on the D1-N 35
6.3 Connections of STO function on D1-N 36
6.4 Activation of the STO function 37
6.5 Preconditions for using the safety function 40
6.6 Examples of circuits for the STO function 42
6.7 Safety function certified by TÜV 44
7. EtherCAT ......................................................................45
7.1 D1-N EtherCAT with CoE protocol 45
8. “Lightening” commissioning software ............................49
8.1 Installation of the software 49
8.2 Initial launch of the “Lightening” software 50
8.3 Operating interface 51
8.4 “Configuration center” without EtherCAT/with EtherCAT 55
8.5 “Application center” 78
8.6 “Protection center” (limitations) 89
8.7 Digital inputs and outputs / “I/O center” 92
9. Commissioning ............................................................94
9.1 Commissioning 95
9.2 “Auto phase center” 95
9.3 “Performance center”, controller parameter optimisation 107
9.4 First travel subject to control 109
9.5 Using the “Scope” functions 110
9.6 Controller tuning 116
9.7 “Advanced gains” – filter 117
9.8 Error history 126
10. mega-ulink protocol .................................................... 127
10.1 Features of the MPI library 127
10.2 PDL (Process Description Language) programming 127
10.3 Features of PDL programming 128
10.4 Programming examples (no liability accepted)) 128
10.5 Writing PDL program to D1-N and saving 131
10.6 Overview advanced parameters 135
10.7 Stopping PDL program, allowing it to run on and deleting it 141
11. Implementing the “Position trigger” ............................. 143
11.1 Requirements 143
12. Troubleshooting .......................................................... 147
12.1 Error codes and troubleshooting 148
12.2 Warnings and problem rectification 150
12.3 Other errors and problem rectification 151
13. Repair and replacement ............................................... 152
14. Parts numbers and accessories .................................... 153
14.1 Article numbers for drive amplifier sets 153
14.2 Article numbers for connector kits 153
14.3 Article numbers for motor cables 154
14.4 Cables for encoder systems 154
15. EC Declaration of Conformity ........................................ 155