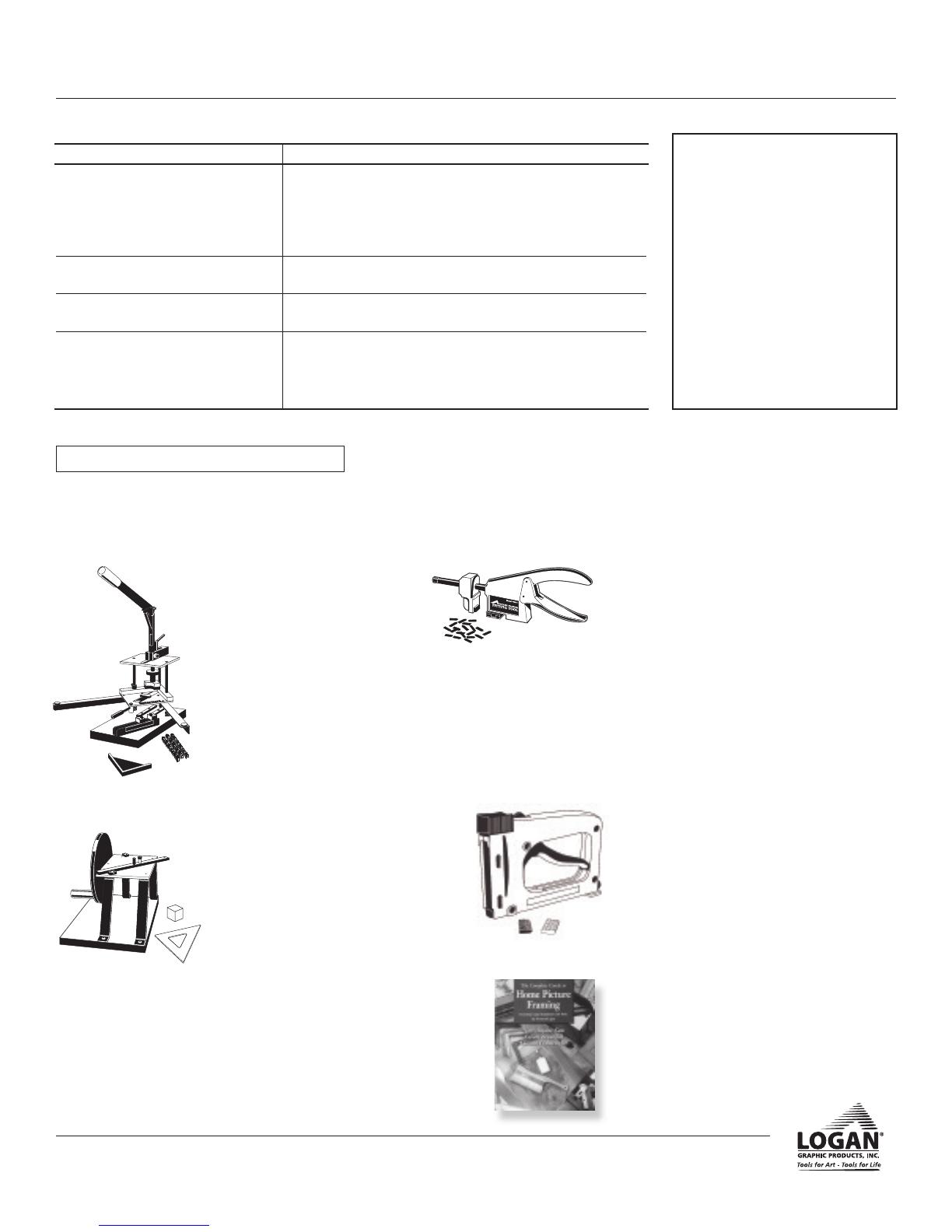
3
Instruction Manual Model F100-2
PRO SAW
Logan Graphic Products Inc., 1100 Brown Street, Wauconda, IL 60084 Toll Free 1 800 331 6232 www.logangraphic.com
Warranty
Logan Graphic Products, Inc. (“Logan”) war-
rants the Pro Saw - Model F100-2, to be free
from defects in parts and workmanship for a
period of one year from the date of original pur-
chase. Logan warrants that it will either repair
or replace, at its sole discretion, any necessary
replacement parts found to be defective.
Should the product need to be returned to
Logan for repair or replacement parts, autho-
rization for any return must come from Logan in
writing. Costs of returning the product to Logan,
including insurances, shall be borne by the pur-
chaser. Logan shall not be liable for any dam-
ages or losses, incidental or consequential,
direct or indirect, arising from the use of this
product. This warranty extends only to the origi-
nal purchaser and is not assignable or transfer-
able. This warranty is in lieu of all other war-
ranties, expressed or implied.
Trouble Shooting
Problem Solution
Saw does not cut straight. Increase blade tension using saw knob tension.
Tighten both pivot screws on back of saw base equally.
Tighten down on the angle block pointer, be sure you can still move the saw
swivel from left hand 45˚ to the right hand 45˚ marks.
Make sure the moulding is securely clamped.
Difficult or slow cutting. Make sure the saw blade is correctly installed (teeth facing away from handle).
Replace saw blade.
Clamp does not hold moulding securely. Turn clamps 90˚ so that they press moulding into the base and back of fence.
Make sure the clamp posts are tight.
Moulding lengths are not consistent. Make sure fence is secure.
Clamp left hand moulding first when using the stop.
Remove any saw dust, splinters and debris from between the
moulding and fence and moulding and the stop.
Also available From Logan Graphics
Logan Graphics picture framing system includes all the tools and accessories you need to produce professional quality
frames including…
PRO Joiner
Model F300-2
Heavy duty professional-style joiner
for precise corner joints
●
V-nail alignment pins*
●Drives all V-nail sizes
●Fits mouldings up to 2
1
/2"
●Can drive two nails at once
*Patent Pending
Fitting tool Model F400-1
Drives brads or point inserts into wood frames to
hold contents in place
●Drives four different inserts
●No slipping or bending
●Easy adjust foot
●Use on hard or soft woods
●Patented rotating insert holder
●Proper drive angle assured
●No guessing or skill required
Replacement Points:
F9 - Multipoint Insert, 400 pcs.
F10 - Rigid Insert, 400 pcs.
F11 - Flexible Insert, 400 pcs.
F12 - Brad Nails, 300 pcs.
Precision Sander Model
F200-1
Sands miters to perfect 45° angle for tight,
square frames
●10 lb wheel
●Adjusts 45° left, 90° and 45° right
●Micro adjustment for perfect 45°
●Also features pre-set stops for 5, 6, and 8
sided frames
●Aluminum oxide sand paper with life extend-
ing bar
●Sand up to 2 1/2" mouldings
●Dust removal bar
Books
Complete and detailed directions
featuring Logan's picture framing tools sys-
tem. Learn inside secrets from
professional framers for creating your own
custom framed art.
Home Picture Framing -
Model 245
Exploded parts view avaialble online at www.logangraphic.com
dual-drive point driver Model F500-1
Secure artwork, backing board and glass into hard or soft wood frames.
Spring-loaded action drives both rigid and flexible points. For successful
operation, use only authentic Logan points.
Replacement Points:
F53 - Flex Point Strip 600 pcs.
F54 - Rigid Point Strip 600 pcs.
F55 - Flex Point Strip 2,500 pcs.
F56 - Rigid Point Strip 2,500 pcs.