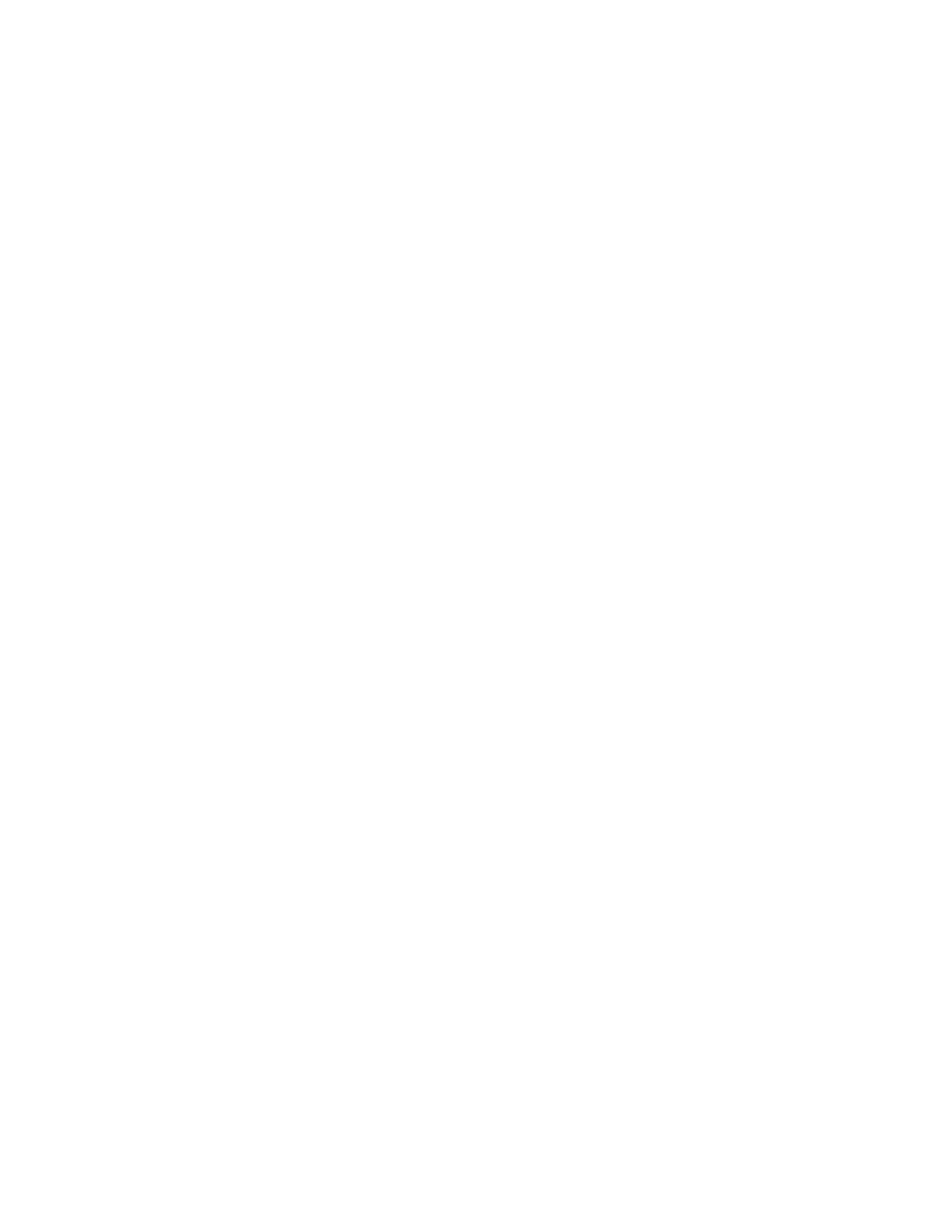
Related Manuals
2 311594Z
Contents
Related Manuals . . . . . . . . . . . . . . . . . . . . . . . . . . . 2
Models . . . . . . . . . . . . . . . . . . . . . . . . . . . . . . . . . . . 3
E-Flo 4-Ball Piston Pumps . . . . . . . . . . . . . . . . . 3
Maximum Working Pressure and Pump Operational
Limits . . . . . . . . . . . . . . . . . . . . . . . . . . . . . . 3
Approvals . . . . . . . . . . . . . . . . . . . . . . . . . . . . . . . . . 5
Warnings . . . . . . . . . . . . . . . . . . . . . . . . . . . . . . . . . 6
Pressure Relief Procedure . . . . . . . . . . . . . . . . . . . 9
Flushing . . . . . . . . . . . . . . . . . . . . . . . . . . . . . . . . . . 9
Troubleshooting . . . . . . . . . . . . . . . . . . . . . . . . . . 10
Electrical Diagrams . . . . . . . . . . . . . . . . . . . . . . . . 12
Repair . . . . . . . . . . . . . . . . . . . . . . . . . . . . . . . . . . . 15
Fluid Section . . . . . . . . . . . . . . . . . . . . . . . . . . . 15
Disassembly . . . . . . . . . . . . . . . . . . . . . . . . 15
Reassembly . . . . . . . . . . . . . . . . . . . . . . . . 17
Slider Cylinder Rebuild Kit 15H874 . . . . . . 18
Slider Cylinder Collector Kit 247341 . . . . . . 19
Electrical Section . . . . . . . . . . . . . . . . . . . . . . . 20
Pressure Transducer Kit 15H876 . . . . . . . . 20
Pressure Sensor Calibration Information
(non-ACS systems) . . . . . . . . . . . . . . . 22
Pressure Transducer Calibration Procedure
(non-ACS systems) . . . . . . . . . . . . . . . 22
TDC Sensor Kit 15H877 . . . . . . . . . . . . . . . 23
Position Sensor . . . . . . . . . . . . . . . . . . . . . . 24
Drive Section . . . . . . . . . . . . . . . . . . . . . . . . . . . 26
Slider Bearing Kit 15H882 . . . . . . . . . . . . . . 26
Drive Linkage Rebuild Kit 15H873 . . . . . . . 28
Crank Arm Kit 15H883 . . . . . . . . . . . . . . . . 29
Motor/Gear Reducer . . . . . . . . . . . . . . . . . . . . . 30
Motor Removal . . . . . . . . . . . . . . . . . . . . . . 30
Motor/Coupler is Difficult to Remove . . . . . 31
Motor Installation . . . . . . . . . . . . . . . . . . . . . 33
Gear Reducer Seal Kit 15H871 . . . . . . . . . 34
Gear Reducer Replacement Kit . . . . . . . . . 36
Parts . . . . . . . . . . . . . . . . . . . . . . . . . . . . . . . . . . . . 42
Drive Section . . . . . . . . . . . . . . . . . . . . . . . . . . . 42
Fluid Section . . . . . . . . . . . . . . . . . . . . . . . . . . . 43
Common Parts . . . . . . . . . . . . . . . . . . . . . . . . . . 44
Model-Specific Parts . . . . . . . . . . . . . . . . . . . . . 46
Gear Reducer . . . . . . . . . . . . . . . . . . . . . . . . . . 49
Technical Data . . . . . . . . . . . . . . . . . . . . . . . . . . . . 50
Graco Standard Warranty . . . . . . . . . . . . . . . . . . . 52
Graco Information . . . . . . . . . . . . . . . . . . . . . . . . . 52
Related Manuals
Manual Description
311592 E-Flo Installation Manual
311593 E-Flo Operation Manual
311595 Pneumatic Back Pressure Regulator
311596 Variable Frequency Drive Instructions
311603 Sensor Circuit Option
3A0539 4-Ball Lowers