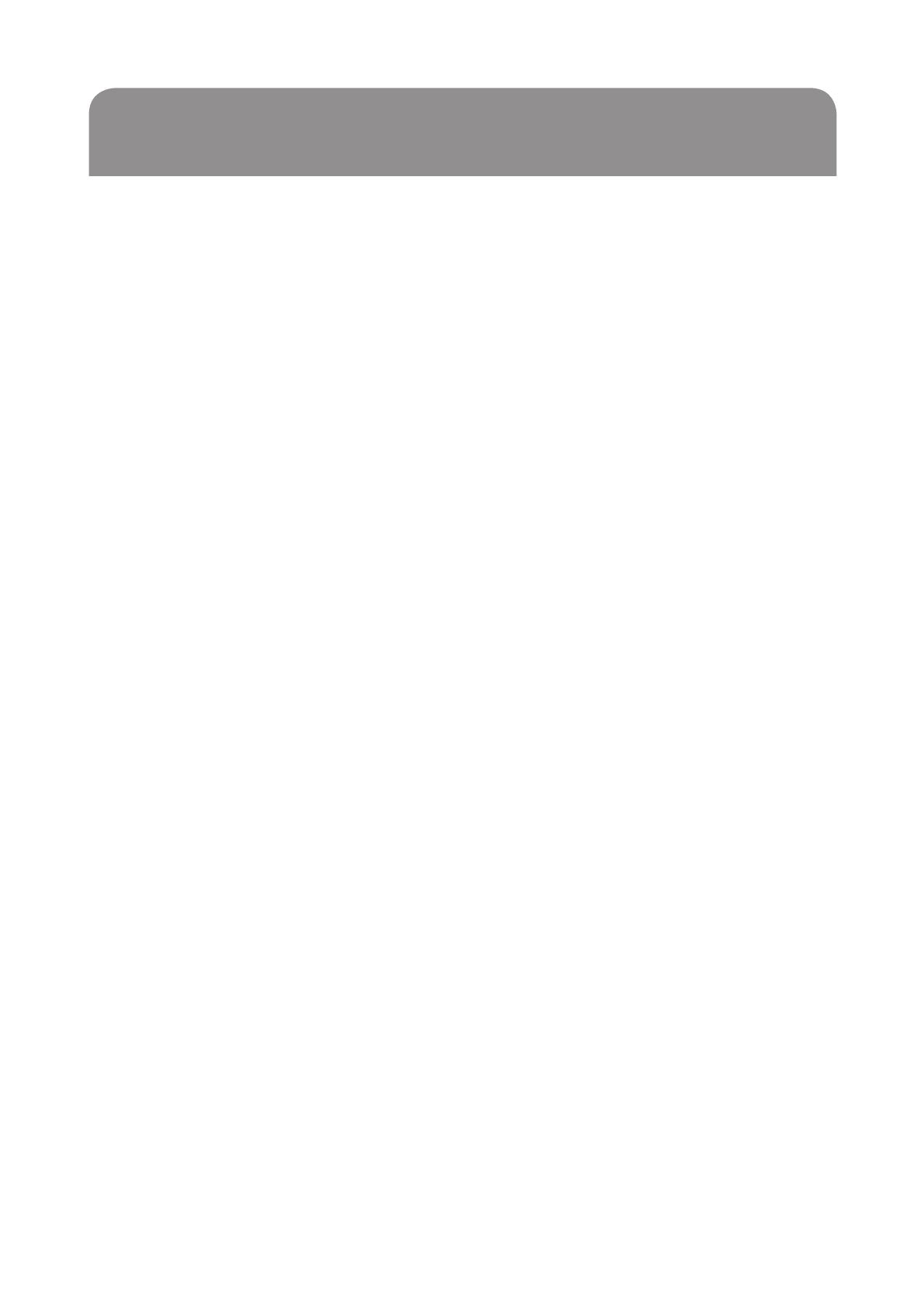
6
2 How to Install
Below is an explanation on where and how to install TS500 (Thermal Shock Test Controller).
Please read before installation.
2.1 Where to Install and Precautions
2.1.1 Where to Install
• As there is a danger of electric shock, please use this product installed on the panel.
• Do not install at places including the following.
· A place where people can contact the terminal out of awareness
· A place that is directly exposed to mechanical vibration or impact
· A place that is exposed to corrosive or combustible gas
· A place with great changes in temperature
· A place with excessively high or low a temperature
· A place that is directly exposed to the direct sunlight
· A place that is much influenced by electromagnetic waves
· A place that is very humid
· A place with inflammable things
· A place with much dust or salt.
2.1.2 Precautions
• The case of this product is made of chrome zinc plate though the bezel is made of ABS/PC fire
retardant materials, do not install this product where inflammable things are around. In particular, do
not put this product directly on an inflammable thing.
• Do not put any device or lines causing noise near this product. In particular, when using this
product at a temperature of 10 ℃ or lower, use the product after fully pre-heating it. In addition, do
not put any device providing extreme heat near this product.
• Install the product horizontally.
• Please perform wiring after blocking the power supply of all instruments.
• This product works at 100 – 240 V AC and 50 – 60 Hz without any separate control if you use
power supply other than the rated power supply, there arises a danger of electric shock and fire.
• Do not handle the product with wet hands, as there is a danger of electric shock.
• When using the product, please follow the basic precautions in order to reduce the danger of fire,
electric shock, and injury.
• Please follow the methods of installation and use specified in this manual.
• Refer to the installation methods on grounding but, never ground on things including gas pipes,
telephone lines, and lightning rods, as there is a danger of explosion and ignition.
• Do not supply power before the connection between devices of this product is finished.
• Do not block the heat release hole of this product, as it may cause a failure.
• The degree of over voltage protection is Category II the service environment is Degree II.