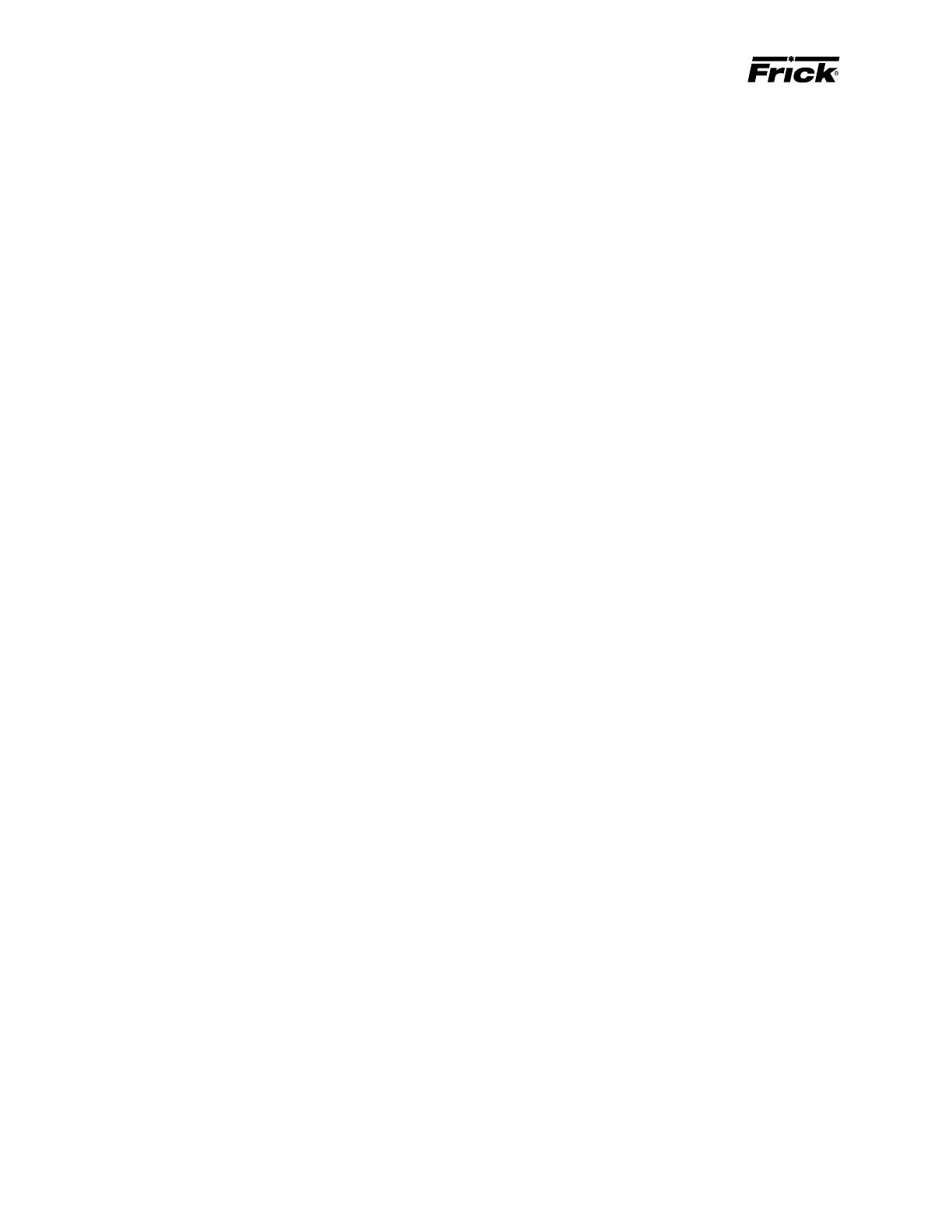
FRICK QUANTUM CONTROL PANEL
OPERATION
S90-010 O
Page 10
•Remote Comm. - A command was sent through
the serial com2 channel that forced Capacity Con-
trol to a different control.
•Schedule - The capacity is being controlled from
the Setback Schedule and the active capacity con-
trol mode. The mode 2 setpoints become active at
the start time. At the stop time the mode 1 setpoints
become active.
SENSOR INDICATION BOX:
The following sensors are displayed:
•Suction - Suction Pressure and Temperature are mea-
sured at the compressor inlet and the values are dis-
played along with the unit of measure.
•Discharge - Discharge Pressure and Temperature are
measured at the compressor outlet and the values are
displayed along with the unit of measure.
•Oil - Oil Pressure and Temperature are measured prior
to entering the compressor and the values are dis-
played along with the unit of measure.
•Filter Diff. - If applicable, pressure drop across the oil
filter. The main oil injection oil filter pressure drop value
(differential) is displayed along with the unit of measure.
•Separator - Oil Separator Temperature value is dis-
played along with the unit of measure.
•Leaving Process - If “Process Temperature Control
Modes” were enabled in Panel Setup, the Leaving Pro-
cess Temperature value is displayed along with the
unit of measure.
•Balance Piston - If applicable, the Balance Piston pres-
sure reading is displayed along with the unit of mea-
sure. This reading is a measurement of the oil pressure
at the Balance Piston.
SLIDE VALVE and SLIDE STOP STATUS BOX:
•Position - The following values are shown:
•Slide Valve or Capacity is shown depending on
the compressor model (Reference “Compressor
Model Differences”)
•Slide Valve - The position is displayed as a
percentage. This value indicates the mechani-
cal position of the Slide Valve and does not
indicate the percentage of compressor capac-
ity.
•Capacity - The position is displayed as a per-
centage. This value indicates the mechanical
position of the Capacity Control pistons and
does not reflect the percentage of full load
operation.
•Slide Stop (If applicable, reference “Compressor
Model Differences”) - The position is displayed as a
ratio (volume index (VI)).
•Mode - The following are shown:
•Slide Valve or Capacity (Reference “Compressor
Model Differences”) - One of the following is shown:
•
Auto (Automatic) - Capacity is being controlled
from active Capacity Control setpoints at the panel.
•Manual - A manual load or unload command
was sent.
•Remote - The Slide Valve or capacity is being
controlled from a remote device.
•Slide Stop (If applicable, reference “Compressor
Model Differences”) - One of the following is shown:
•Auto (Automatic) - The movement of the Slide
Stop is being controlled from internal logic at
the panel.
•Manual - A Slide Stop manual increase or
decrease command was sent.
•Status - The following are shown:
•Slide Valve or Capacity (Reference “Compressor
Model Differences”) - One of the following could
be shown:
•Load - Indicates the compressor is loading
and the Slide Valve or capacity value is in-
creasing.
•Unload - Indicates the compressor is unload-
ing and the Slide Valve or capacity value is
decreasing.
•Idle - Indicates the Slide Valve or capacity is
holding at the present position
•Slide Stop (If applicable) - One of the following is
shown:
•Increase - Moving to a higher VI.
•Decrease - Moving to a lower VI.
•Idle - Not moving.
The following messages could be shown:
•Stop Load - If this message is shown, it indicates that
the compressor is being prevented from further load-
ing. The Stop Load setpoint that has been reached is
shown next to the stop load message, i.e. Stop Load -
High Motor Amps, this message indicates that the “High
Motor Amps Stop Load” setpoint was reached and the
compressor is being prevented from further loading.
One of the following messages could be shown if the
corresponding Stop Load setpoint is reached:
•High Motor Amps
The motor amps is greater than or equal to the
“High Motor Amps Stop Load” setpoint, the com-
pressor is prevented from further loading until the
Motor Amps is less than this setpoint.
•High Discharge Pressure
The Discharge Pressure is greater than or equal
to the “High Discharge Pressure Stop Load” set-
point, the compressor is prevented from further
loading until the Discharge Pressure is less than
this setpoint.
•High Discharge Temperature
The Discharge Temperature is greater than or
equal to the “High Discharge Temperature Stop
Load” setpoint, the compressor is prevented from
further loading until the Discharge Temperature is
less than this setpoint.
•Low Suction Pressure
The Suction Pressure is less than or equal to the
“Low Suction Pressure Stop Load” setpoint, the
compressor is prevented from further loading until
the Suction Pressure is greater than this setpoint.
•High Suction Pressure
The Suction Pressure is greater than or equal to