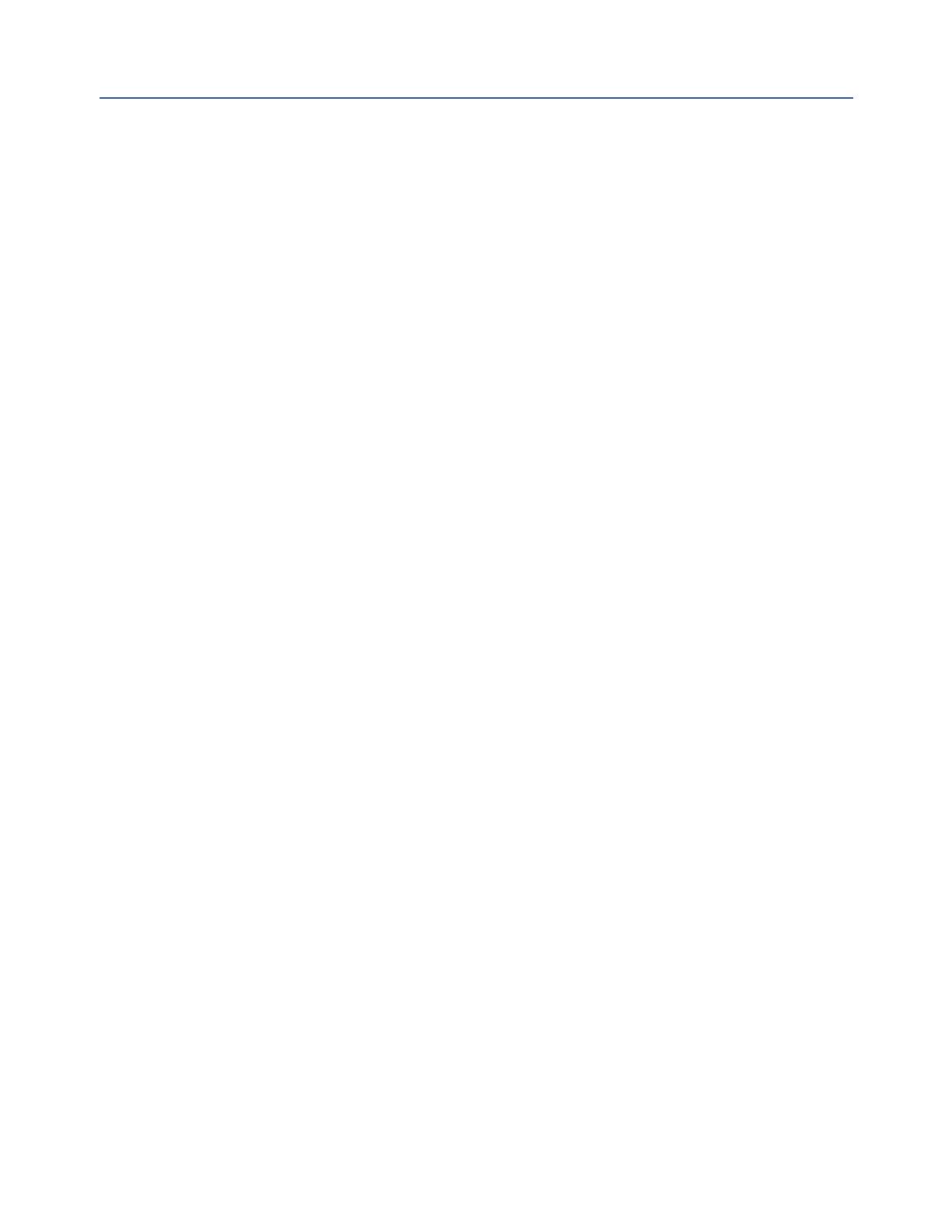
Installation, Operation and Maintenance Manual
MAN-01-10-93-0722-EN Rev. 0
July 2019
6
Section 2: Procedure
Procedure
2.3 Firmware Download Procedure
Computer and software requirements:
1. Laptop or other computer equipment with Windows 98 or later and one RS-232 serial
port.
2. Engineering RJ12 cable with DB9 adapter.
3. ABM Commander for Windows V1.45
Application software requirements:
1. M124 Network master software file to be downloaded:
M124N110.ABM for one Modbus master module located in slot 1 of each chassis.
LCD124_4.ABM for one Modbus master module located in slot 2 of each chassis.
2. M250 Network master software file to be downloaded:
M25MBP12.ABM for one Modbus master module located in slot 2 of each chassis.
Download Procedure for Modbus master:
1. Turn off power to master to be upgraded. Power may remain on the other chassis.
2. Remove CoProcessor from the PLC rack slot 1 (first module beside the main CPU).
3. Insert the “Clear All” jumper onto the 2-pin header.
4. Insert the module back into the rack.
5. Cycle power to the master on and then off.
6. Again, remove the CoProcessor form the rack.
7. Remove the “Clear All” jumper and place on only one pin of the 2-pin header.
8. Insert the module back into the rack.
9. Connect RJ12 cable end to Port 1 of the Coprocessor and the DB9 end to the PC.
10. Turn on power.
11. Open ABM Commander application on the PC.