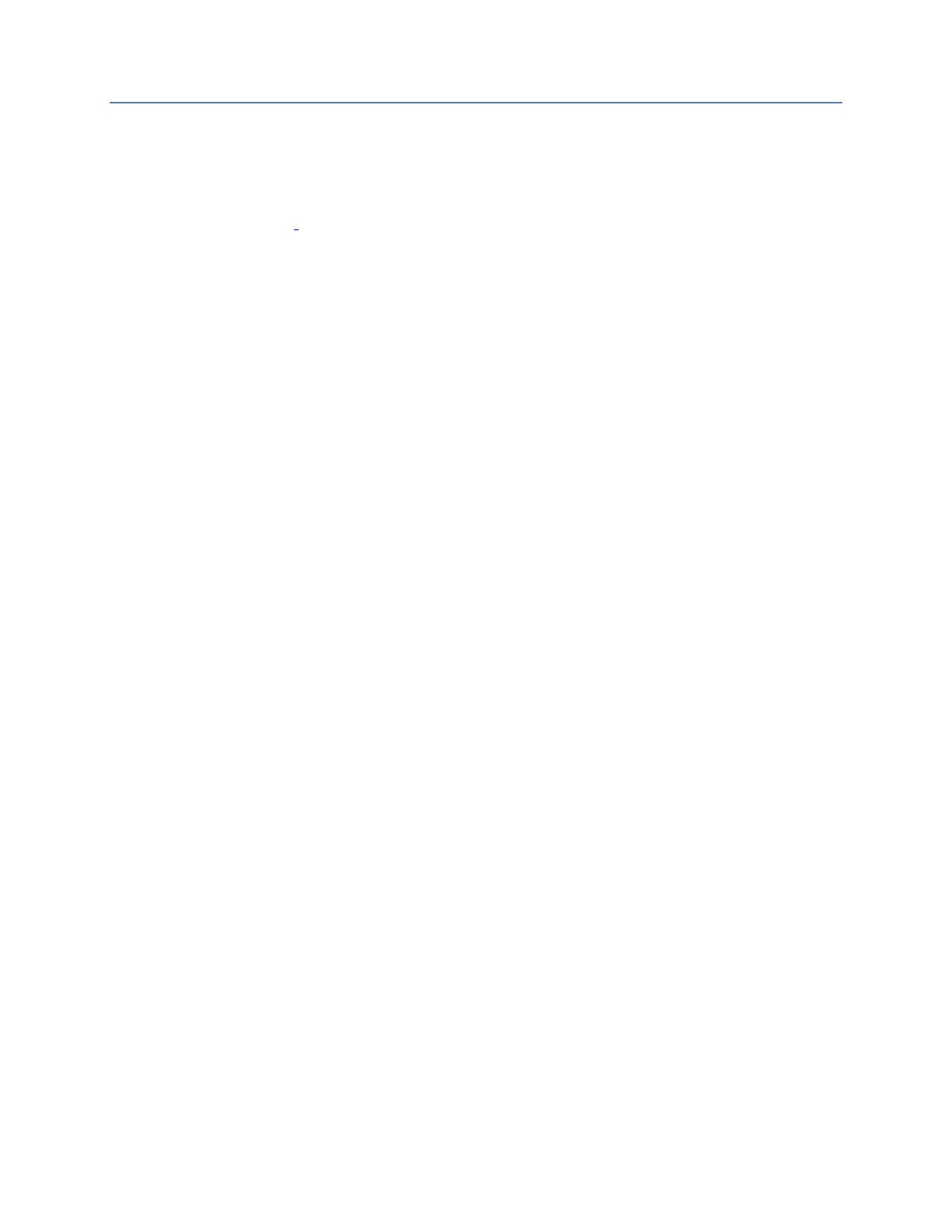
Table of Contents Operation Manual
October 2015 QCL-MAN -CT4000-OEM-Rev D
Table of Contents ii
4.13 The laser calibration tool .............................................................................. 40
4.13.1 Required equipment ................................................................... 40
4.13.2 Procedure ................................................................................... 41
Section 5:Scheduled maintenance
5.1 Maintenance ............................................................................................... 46
5.2 Schedule ................................................................................................... 46
5.2.1 Weekly check .............................................................................. 46
5.2.2 Monthly check ............................................................................. 46
5.2.3 Biannual check ............................................................................ 46
5.3 Maintenance activities ................................................................................. 46
5.3.1 Zero calibration ........................................................................... 46
5.3.2 Span calibration .......................................................................... 47
5.3.3 X-shift calibration ........................................................................ 47
5.3.4 Sample cell mirror purge ............................................................. 47
5.3.5 Laser wavelength calibration ....................................................... 47
Section 6:Failure diagnosis
6.1 Introduction ................................................................................................ 48
6.2 Failure diagnosis principles .......................................................................... 48
6.3 Repairable faults .......................................................................................... 48
6.4 Faults only repairable by Emerson Process Management .............................. 49
6.5 Tools and test equipment ............................................................................ 49
6.6 Wiring diagram ........................................................................................... 49
6.7 General troubleshooting and diagnostics information ................................. 55
6.7.1 System messages ........................................................................ 55
6.7.2 Warning or error message significance ........................................ 58
6.7.3 Communication fault messages................................................... 58
6.7.4 Resolution of warning or error messages ..................................... 59
6.8 Simple fault resolution ................................................................................. 59
6.8.1 No gas measurement change ...................................................... 59
6.8.2 Gas temperature low ................................................................... 59
6.8.3 Laser signal level low .................................................................... 60
6.9 Visual examination of the OEM module........................................................ 60
6.9.1 Visual inspection of the CT4000................................................... 60
6.9.2 Removing the lower cover ........................................................... 61
6.9.3 Replacing the lower cover ........................................................... 62
6.9.4 Component identification ........................................................... 63
Appendix A: Model CT4142
A.1 System specification .................................................................................... 66
A.2 Cross-interference performance .................................................................. 67
A.3 Linearity performance ................................................................................. 67
A.4 Performance characteristics ........................................................................ 67
A.5 Operational and physical characteristics ...................................................... 69
Appendix B: Model CT4125
B.1 System specification .................................................................................... 70
B.2 Cross-interference performance .................................................................. 70
B.3 Linearity performance ................................................................................. 70
B.4 Performance characteristics ........................................................................ 71
B.5 Operational and physical characteristics ...................................................... 71