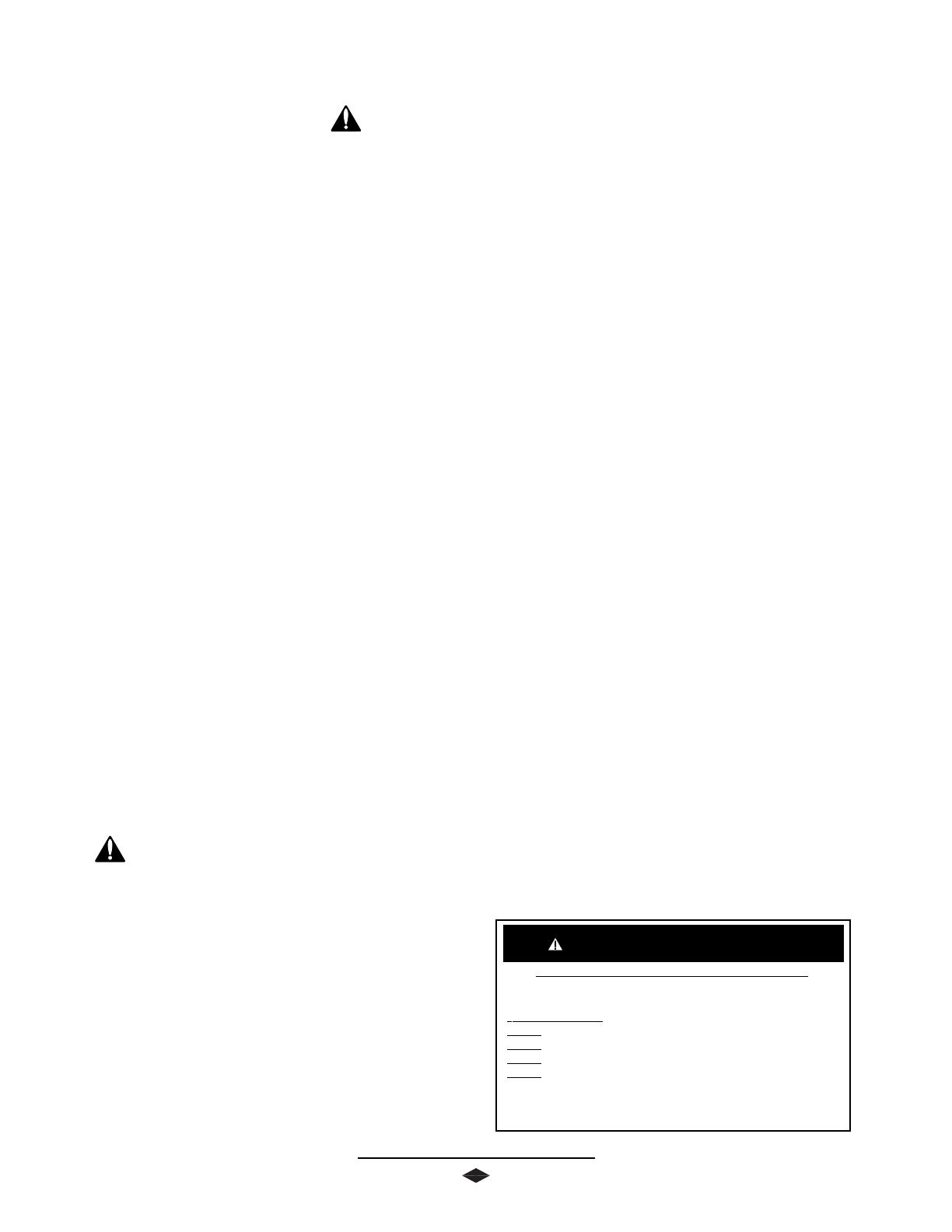
7
GENERAL PRECAUTIONS
All Spicer original equipment or service parts for
steering and drive axle brakes are manufactured using
non-asbestos brake lining. It is recommended that
original Spicer service parts be used when brake mainte-
nance is necessary.
SAFETY PRECAUTIONS
Proper service and repair of vehicle components is
important to the safe and reliable operation of all motor
vehicles. This applies particularly to brakes such as the
ones described in this manual. The procedures recom-
mended and described in this manual are tested,
effective methods for performing service operation.
Follow each procedure closely, making use of both the
text and pictures. Some of these service procedures
show the use of certain tools designed especially for the
operation being performed. It is not mandatory that
these tools be used; they are shown only as preferred
means of performing the operation. It is not practical to
anticipate and advise the service trade of all possible
alternate service methods, and of all possible hazardous
consequences that could result from any particular
method. Accordingly, anyone who uses a service
procedure or tool different than shown must insure that
their safety, and that the vehicle’s safety will not be
jeopardized by the service method selected.
CA CA
CA CA
CA
UTION:UTION:
UTION:UTION:
UTION:
When wWhen w
When wWhen w
When w
orking on or arorking on or ar
orking on or arorking on or ar
orking on or ar
ound airound air
ound airound air
ound air
brbr
brbr
br
akak
akak
ak
e se s
e se s
e s
yy
yy
y
stst
stst
st
ems and componentems and component
ems and componentems and component
ems and component
s, the follos, the follo
s, the follos, the follo
s, the follo
wingwing
wingwing
wing
prpr
prpr
pr
ecautions should be observecautions should be observ
ecautions should be observecautions should be observ
ecautions should be observ
ed:ed:
ed:ed:
ed:
1.1.
1.1.
1. Always block vehicle wheels. Stop engine when
working under a vehicle. Depleting vehicle air
system pressure may cause vehicle to roll. Keep
hands away from chamber push rods and slack
adjusters; they may automatically apply as system
pressure drops.
2.2.
2.2.
2. Never connect or disconnect a hose or line con-
taining air pressure. It may whip as air escapes.
IMPORIMPOR
IMPORIMPOR
IMPOR
TT
TT
T
ANTANT
ANTANT
ANT
READ THIS SECTION BEFORE STREAD THIS SECTION BEFORE ST
READ THIS SECTION BEFORE STREAD THIS SECTION BEFORE ST
READ THIS SECTION BEFORE ST
ARAR
ARAR
AR
TINGTING
TINGTING
TING
ANY SERANY SER
ANY SERANY SER
ANY SER
VICE PROCEDURESVICE PROCEDURES
VICE PROCEDURESVICE PROCEDURES
VICE PROCEDURES
Never remove a component or pipe plug unless you
are certain all system pressure has been depleted.
3.3.
3.3.
3. Never exceed recommended air pressure and always
wear safety glasses when working with air pressure.
Never look into air jets or direct them at anyone.
4.4.
4.4.
4. Never attempt to disassemble a component until
you have read and understand recommended
procedures. Some components contain powerful
springs and injury can result if not properly
disassembled. Use only proper tools and observe
all precautions pertaining to use of those tools.
5.5.
5.5.
5. Use only genuine Spicer replacement parts and
components.
A. A.
A. A.
A. Only components, devices, mounting and
attaching hardware specifically designed for use
in air brake systems should be used.
B. B.
B. B.
B. Replacement hardware, tubing, hose, fittings, etc.
should be of equivalent size, type, length and
strength as the original equipment.
C. C.
C. C.
C. Make certain that when replacing tubing or hose,
all supports, clamps or suspending devices that
were originally installed by the vehicle manufac-
turer are reinstalled.
6.6.
6.6.
6. Devices with stripped threads or damaged parts
should be replaced. Repairs requiring machining
should not be attempted.
CAUTION
BREATHING BRAKE DUST MAY BE HAZARDOUS TO YOUR HEALTH AND
MAY CAUSE SERIOUS RESPIRATORY OR OTHER BODILY HARM.
FOLLOW 0.S.H.A. STANDARDS FOR PROPER PROTECTIVE DEVICES TO BE USED
WHEN WORKING WITH BRAKE MATERIALS.
BRAKE LININGS CONTAIN NON-ASBESTOS FIBERS
AVOID CREATING DUST
DO NOT REMOVE BRAKE DRUM WITHOUT PROPER PROTECTIVE EQUIPMENT.
DO NOT WORK ON LININGS WITHOUT PROPER PROTECTIVE EQUIPMENT.
DO NOT REPLACE LININGS WITHOUT PROPER PROTECTIVE EQUIPMENT.
DO NOT ATTEMPT TO SAND, GRIND, CHISEL, FILE, HAMMER OR ALTER BRAKE
LININGS IN ANY MANNER WITHOUT PROPER PROTECTIVE EQUIPMENT.