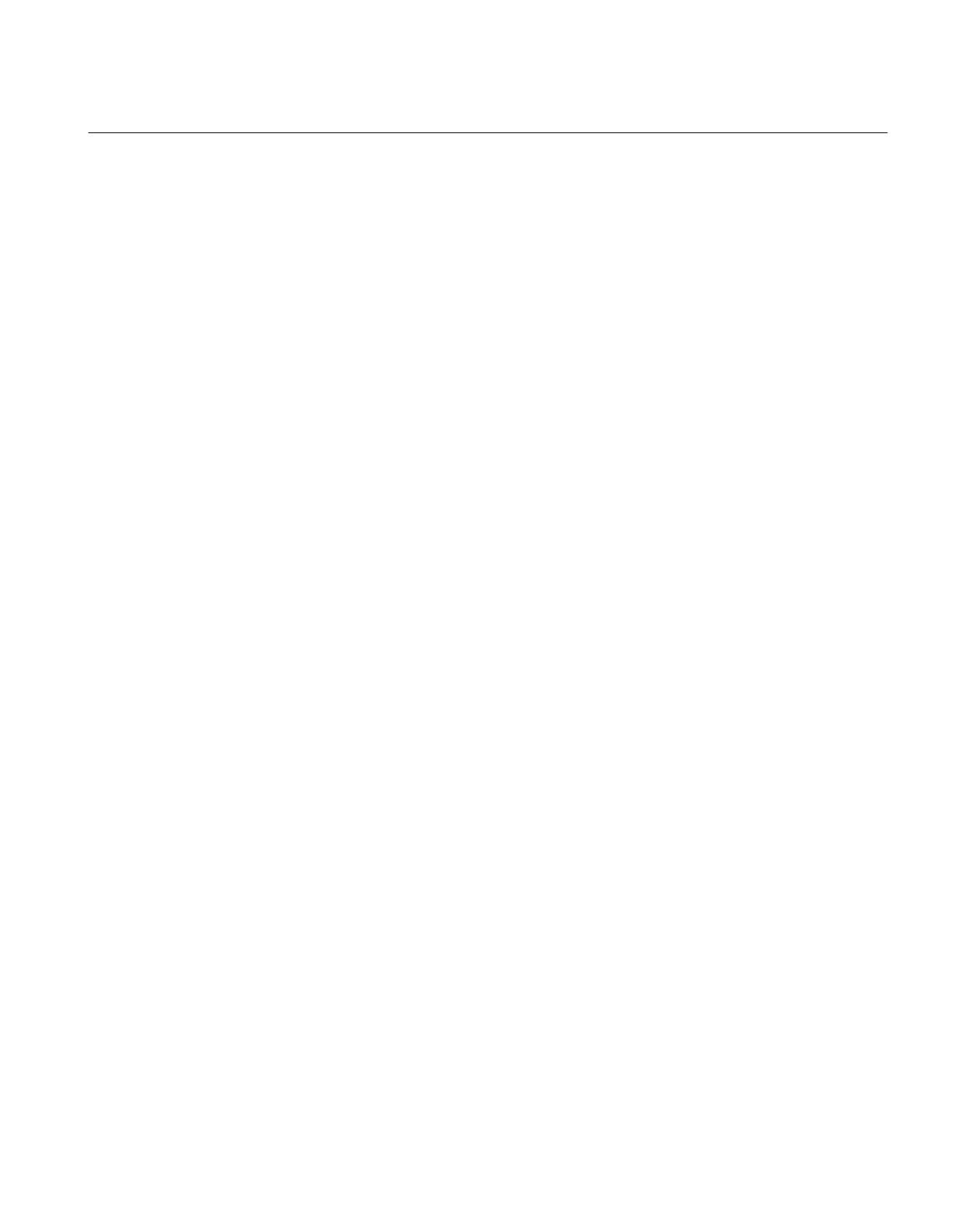
Table of contents
Section 1 Introduction............................................................................3
This manual.............................................................................................. 3
Intended audience.................................................................................... 3
Product documentation.............................................................................4
Product documentation set..................................................................4
Document revision history................................................................... 4
Related documentation........................................................................4
Symbols and conventions.........................................................................5
Symbols...............................................................................................5
Document conventions........................................................................ 5
Section 2 DNP3 overview......................................................................7
DNP3 standard......................................................................................... 7
Physical layer.......................................................................................7
Data link layer......................................................................................7
Transport pseudo-layer....................................................................... 8
Application layer parameters............................................................... 9
Communication modes........................................................................9
Section 3 Vendor-specific implementation.......................................... 11
DNP3 link modes.................................................................................... 11
DNP3 data objects.............................................................................11
DNP3 serial link mode....................................................................... 11
DNP3 TCP/IP mode...........................................................................12
DNP3 point settings................................................................................ 12
Binary input points............................................................................. 12
Binary output status points and control relay output blocks.............. 12
CROB index (point) types.............................................................13
Control modes.............................................................................. 14
Binary output status points........................................................... 16
Analog inputs.....................................................................................17
Analog data scaling...................................................................... 18
Fault record time stamp................................................................19
DNP3 points............................................................................................20
Point configuration.............................................................................20
Class assignment.............................................................................. 20
Table of contents
REF615R 1
Communication Protocol Manual