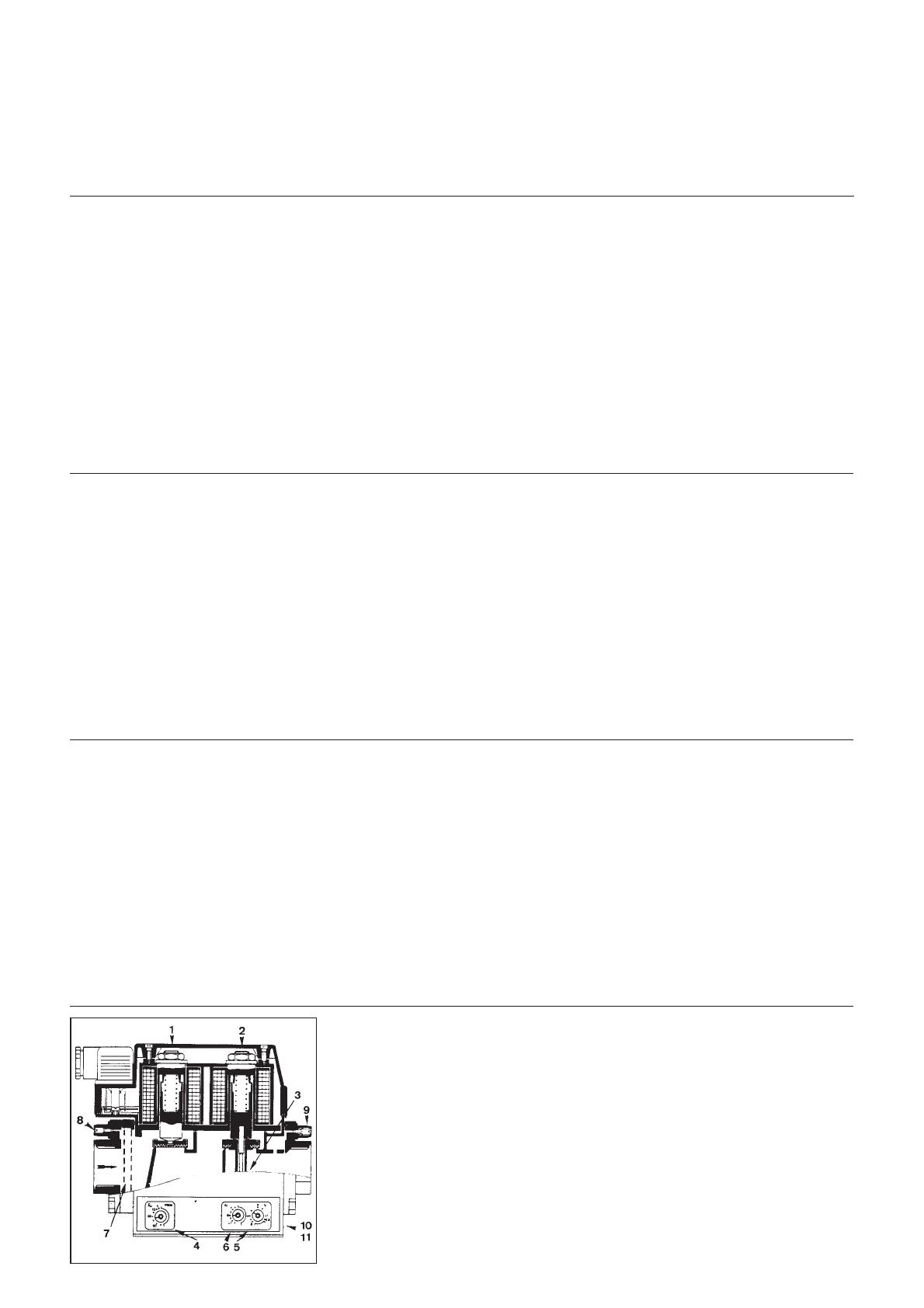
08/2005 - Art. Nr. 13 018 073A
36
Starting in gas-burning mode
The fuel selector control located on the
burner unit is set to gas operation. If
heat is required of the installation, the
heat generator regulator switches the
burner on automatically. The
subsequent operation of the burner
depends on the way the automatic
combustion controller is programmed.
The electric motor with fan turbine
starts up on initial blower operation with
prescribed air flow rate and time.
Immediately after initial blower
operation starts, the air deficiency
safety device must switch within a
specific time limit to operating
mode, i.e. the set air pressure must be
reached and must be maintained until
the switch over. Pre-ignition then starts,
followed by gas release. Proper flame
quality must be signalled to the
automatic combustion controller by the
UV cell within the specified safety
period.
The burner is in operation.
Operating functions in gas-burning
mode
Once the sequence of initial blower
operation, high voltage ignition, gas
release and ignition switch-off has been
correctly performed, a flame must be
signalled by the UV cell.
The burner is then in operating mode.
Two-stage burner operation
The air flap actuator receives current
from the stage 2 thermostat of the heat
generator. The air flap and compact
gas unit open and release full load
quantities of gas and air. The burner is
in full-load mode.
Safety functions, gas-burning mode
Should a flame fail to ignite when the
burner is started (on gas release), the
burner will be switched off as soon as
the safety interval t2 of max. 3 seconds
has elapsed (safety shutdown). In
safety shutdown the gas valve
invariably closes and the electric motor
stops. In the event of flame extinction
during operation, the gas supply is
interrupted immediately and the
automatic combustion controller
switches over to fault within 1 second.
In the event of air deficiency during the
initial blower time, the burner does not
come into operation.
A safety shutdown follows. Air
deficiency during operation also triggers
a safety shutdown.
In the event of gas deficiency, the
burner does not come into operation.
No initial blower operation takes place.
In the event of gas deficiency during
operation, the gas valve closes and the
burner switches off. However, safety
shutdown does not take place. After
re-establishment of gas pressure, the
burner starts up again automatically.
If the power supply is interrupted, the
gas supply is immediately cut off. After
re-establishment of the power supply,
the burner starts up again
automatically.
If light deficiency is detected by the UV
flame monitor, safety shutdown takes
place. If flame presence is signalled
during initial blower operation, the
program sequence is broken off and
the automatic combustion controller
locks out. Burner failure is signalled by
a red indicator light in the release
button of the automatic combustion
controller. The installation can be
started up again by pressing the
release button.
Mode of operation of compact gas
unit type CG... V
When current is applied to the
windings, valve 1 and valve 2 open.
The incoming gas is cleaned by a filter
pos. 5. The integral pressure regulator
pos. 3 regulates the desired output
pressure. Burner gas pressure p
G
(internal pressure take-off line) of the
relative pressure regulator is
determined by combustion air pressure
p
L
(external pressure take-off line) as
reference variable.
Combustion chamber pressure pF can be
taken into account with it as a correction.
The required values for:
·
pressure monitor set pressure p
W
·
transfer ratio V and
·
zero point displacement N can be
adjusted with the adjusting screws pos. 4
provided on both sides.
Threaded connection points for combustion
chamber pressure p
F
and combustion air
pressure p
L
are provided on the front.
Inlet and outlet gas pressure can be
measured at sampling points pos. A
and pos. B.
1 Valve 1
2 Valve 2
3 Pressure regulator
4 Adjusting screw p
W
, V, N
5 Adjusting screw V
6 Adjusting screw N
7 Filter
8 Measurement point, inlet pressure
9 Measurement point, outlet pressure
10 Connection point p
L
“Combustion Air Pressure”
11 Connection point p
F
“Combustion
Chamber Pressure”
Gas functions
Starting
Operation
Safety function
Mode of operation of the compact gas unit