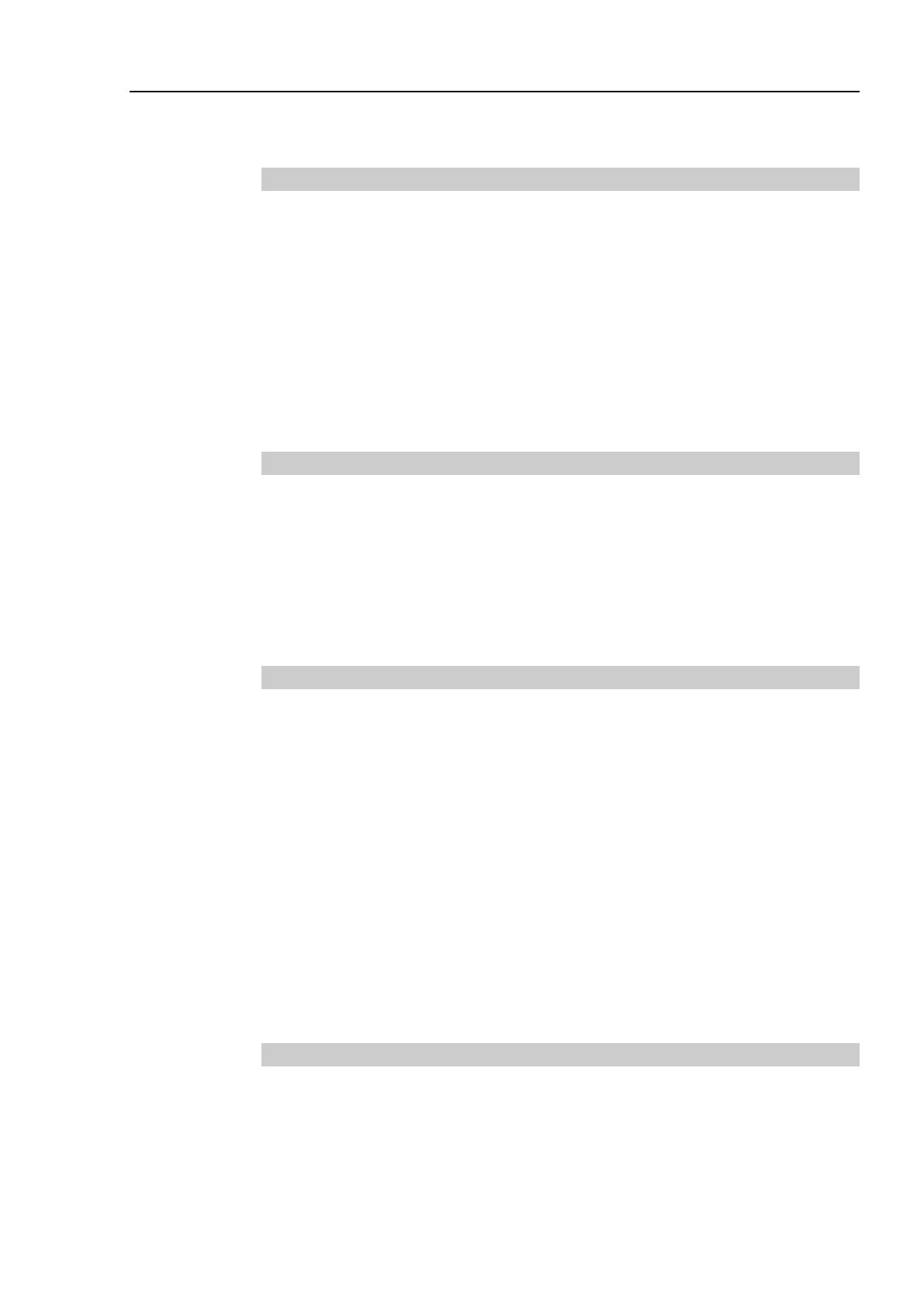
TABLE OF CONTENTS
LS Rev.13 ix
Setup & Operation
1. Safety 3
1.1 Conventions.............................................................................................. 3
1.2 Design and Installation Safety .................................................................. 4
1.2.1 Strength of the Ball Screw Spline ................................................. 5
1.3 Operation Safety ...................................................................................... 6
1.4 Emergency Stop ....................................................................................... 8
1.4.1 Controller Firmware Ver. 7.0.2.3 or earlier ................................... 8
1.4.2 Controller Firmware Ver. 7.0.2.4 or later .................................... 10
1.5 Emergency Movement Without Drive Power ......................................... 12
1.6 ACCELS Setting for CP Motions ............................................................ 13
1.7 Warning Labels ....................................................................................... 14
2. Specifications 16
2.1 Features of LS series Manipulators ....................................................... 16
2.2 Model Number ........................................................................................ 17
2.3 Part Names and Outer Dimensions ....................................................... 18
2.3.1 LS3 ............................................................................................. 18
2.3.2 LS6 ............................................................................................. 22
2.4 Specifications ......................................................................................... 26
2.5 How to Set the Model ............................................................................. 28
3. Environments and Installation 29
3.1 Environmental Conditions ...................................................................... 29
3.2 Base Table .............................................................................................. 30
3.3 Mounting Dimensions ............................................................................. 31
3.3.1 LS3 ............................................................................................. 31
3.3.2 LS6 ............................................................................................. 33
3.4 Unpacking and Transportation ............................................................... 35
3.5 Installation Procedure............................................................................. 36
3.5.1 Standard-Model .......................................................................... 37
3.5.2 Cleanroom-Model ....................................................................... 38
3.6 Connecting the Cables ........................................................................... 39
3.7 User Wires and Pneumatic Tubes.......................................................... 40
3.8 Relocation and Storage .......................................................................... 41
3.8.1 Precautions for Relocation and Storage .................................... 41
3.8.2 Relocation ................................................................................... 42
4. Setting of End Effectors 43
4.1 Attaching an End Effector....................................................................... 43
4.2 Attaching Cameras and Valves .............................................................. 45
4.3 Weight and Inertia Settings .................................................................... 46
4.3.1 Weight Setting ............................................................................ 46
4.3.2 Inertia Setting ............................................................................. 49
4.4 Precautions for Auto Acceleration/Deceleration of Joint #3 ................... 53