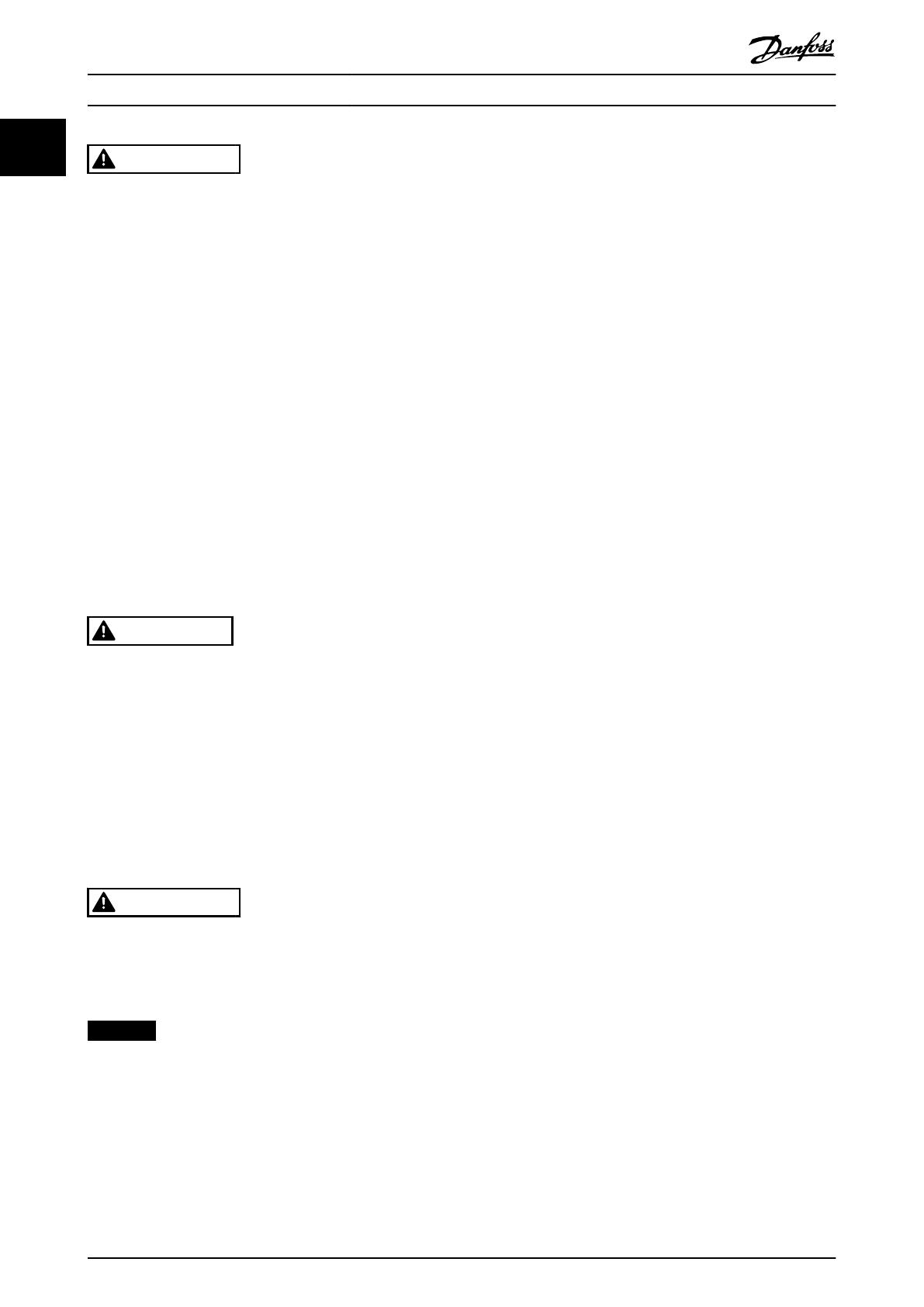
WARNING
DISCHARGE TIME
The frequency converter contains DC-link capacitors,
which can remain charged even when the frequency
converter is not powered. High voltage can be present
even when the warning LED indicator lights are o.
Failure to wait the specied time after power has been
removed before performing service or repair work can
result in death or serious injury.
•
Stop the motor.
•
Disconnect AC mains and remote DC-link power
supplies, including battery back-ups, UPS, and
DC-link connections to other frequency
converters.
•
Disconnect or lock PM motor.
•
Wait at least 4 minutes for the capacitors to
discharge fully.
•
Before performing any service or repair work,
use an appropriate voltage measuring device to
make sure that the capacitors are fully
discharged.
CAUTION
RISK OF INJURY OR PROPERTY DAMAGE
Do not assume that a motor is wired properly after
completed service of the frequency converter.
Check for:
•
Loose connections.
•
Improper programming.
•
Added equipment.
Failure to perform these checks can result in personal
injury, property damage, or less than optimal
performance.
WARNING
REPAIR WORK
In the event of an error, alarm or warning, refer to
chapter 7 Troubleshooting. Before commencing repair
work, contact Danfoss Service.
NOTICE
PELV COMPLIANCE
All control terminals and relay terminals 01-03/04-06
comply with PELV (Protective Extra Low Voltage).
However, in grounded delta conguration above 400 V,
the frequency converter is not PELV-compliant.
1.3 Purpose of the Manual
This manual is intended to provide detailed information for
the installation and start up of the frequency converter.
Chapter 2 Installation provides details of mechanical and
electrical installation. Chapter 3 Start Up and Functional
Testing provides detailed procedures for startup and
functional testing. The remaining chapters provide supple-
mentary details. These include user interface, basic
operational concepts, programming and application
examples, start up troubleshooting, and equipment speci-
cations.
Optional equipment is available that can change some of
the procedures described. Be sure to see the instructions
supplied with those options for specic requirements.
1.4 Additional Resources
Other resources are available to understand advanced
frequency controller functions and programming.
•
The VLT
®
Decentral Drive FCD 302 Programming
Guide, provides greater detail in how to work
with parameters and many application examples.
•
The VLT
®
Decentral Drive FCD 302 Design Guide, is
intended to provide detailed capabilities and
functionality to design motor control systems.
•
VLT
®
Installation Instructions.
•
VLT
®
Installation Instructions.
•
VLT
®
Safe PLC Interface Option Installation
Instructions.
•
Fieldbus manuals:
•
VLT
®
PROFIBUS DP MCA 101 Programming
Guide.
•
VLT
®
PROFIBUS DP MCA 101 Installation
Instructions.
•
VLT
®
EtherNet/IP MCA 121 Programming
Guide.
•
VLT
®
EtherNet/IP MCA 121 Installation
Instructions.
•
VLT
®
PROFINET MCA 120 Programming
Guide.
•
VLT
®
PROFINET MCA 120 Installation
Instructions.
•
VLT
®
Brake Resistor MCE 101 Design Guide.
•
Training courses both on-line and in person.
•
Hotline, telephone and on-line help.
•
Installation, set up, and commissioning is also
available by Danfoss trained and approved
installers.
Introduction
VLT
®
Decentral Drive FCD 302
4 Danfoss A/S © 05/2016 All rights reserved. MG04F402
11