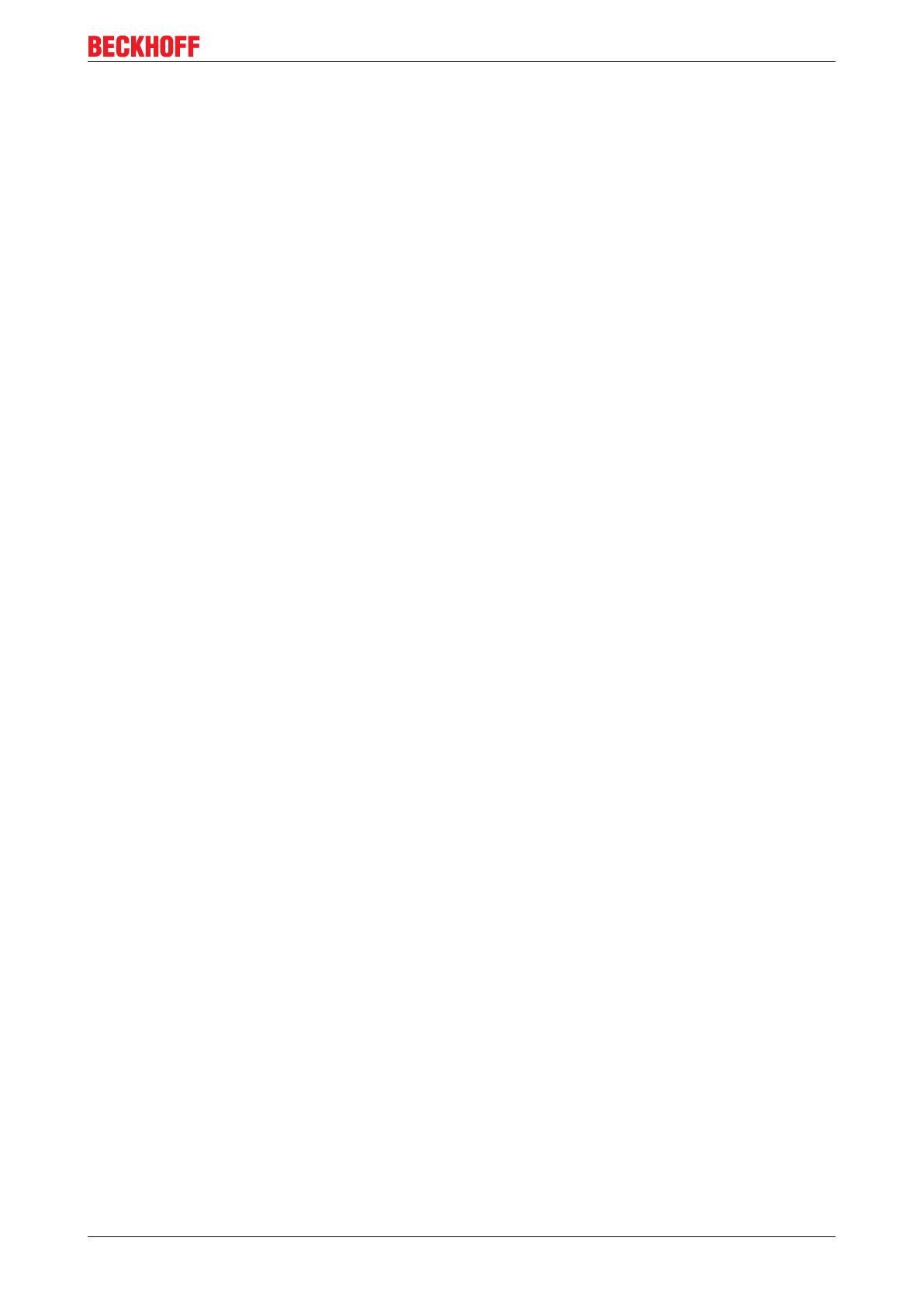
Table of contents
Profibus M310/B310 3Version: 1.0
Table of contents
1 Foreword ....................................................................................................................................................5
1.1 Notes on the documentation........................................................................................................... 5
1.2 Safety instructions .......................................................................................................................... 6
1.3 Documentation issue state ............................................................................................................. 7
2 PROFIBUS system overview ....................................................................................................................8
2.1 Configuration options.................................................................................................................... 10
2.2 Communication protocols and services ........................................................................................ 13
2.3 Technical data - PROFIBUS......................................................................................................... 15
3 Connection and cabling..........................................................................................................................16
3.1 Profibus Connection ..................................................................................................................... 16
3.2 Cabling.......................................................................................................................................... 17
3.3 Topology ....................................................................................................................................... 20
4 TwinCAT tabs...........................................................................................................................................21
4.1 Tree view ...................................................................................................................................... 21
4.2 Profibus master............................................................................................................................. 23
4.2.1 General ............................................................................................................................23
4.2.2 CCAT PBM.......................................................................................................................24
4.2.3 Bus Parameters (DP).......................................................................................................25
4.2.4 Startup/Fault settings .......................................................................................................26
4.2.5 ADS..................................................................................................................................27
4.2.6 DP diag ............................................................................................................................28
4.2.7 Box States........................................................................................................................29
4.3 Profibus slave ............................................................................................................................... 30
4.3.1 Profibus............................................................................................................................30
4.3.2 Features...........................................................................................................................31
4.3.3 Diag..................................................................................................................................32
5 Parameterization and commissioning...................................................................................................33
5.1 Synchronizing Profibus ................................................................................................................. 33
5.2 Parameterization with TwinCAT 2 ................................................................................................ 37
5.2.1 Searching for target systems ...........................................................................................37
5.2.2 Adding a Profibus slave ...................................................................................................39
5.2.3 Creating a virtual slave ....................................................................................................41
5.2.4 Setting the address ..........................................................................................................42
5.2.5 Creating a PLC project.....................................................................................................43
5.2.6 Linking variables ..............................................................................................................45
5.2.7 Load configuration to CX .................................................................................................46
5.2.8 Adding a Profibus master.................................................................................................48
5.2.9 Testing Profibus networking.............................................................................................49
5.2.10 'Turning' process data ......................................................................................................50
5.3 Parameterization with TwinCAT 3 ................................................................................................ 51
5.3.1 Searching for target systems ...........................................................................................51
5.3.2 Adding a Profibus slave ...................................................................................................53
5.3.3 Creating a virtual slave ....................................................................................................55
5.3.4 Setting the address ..........................................................................................................56
5.3.5 Creating a PLC project.....................................................................................................57
5.3.6 Linking variables ..............................................................................................................59
5.3.7 Load configuration to CX .................................................................................................60
5.3.8 Adding a Profibus master.................................................................................................62