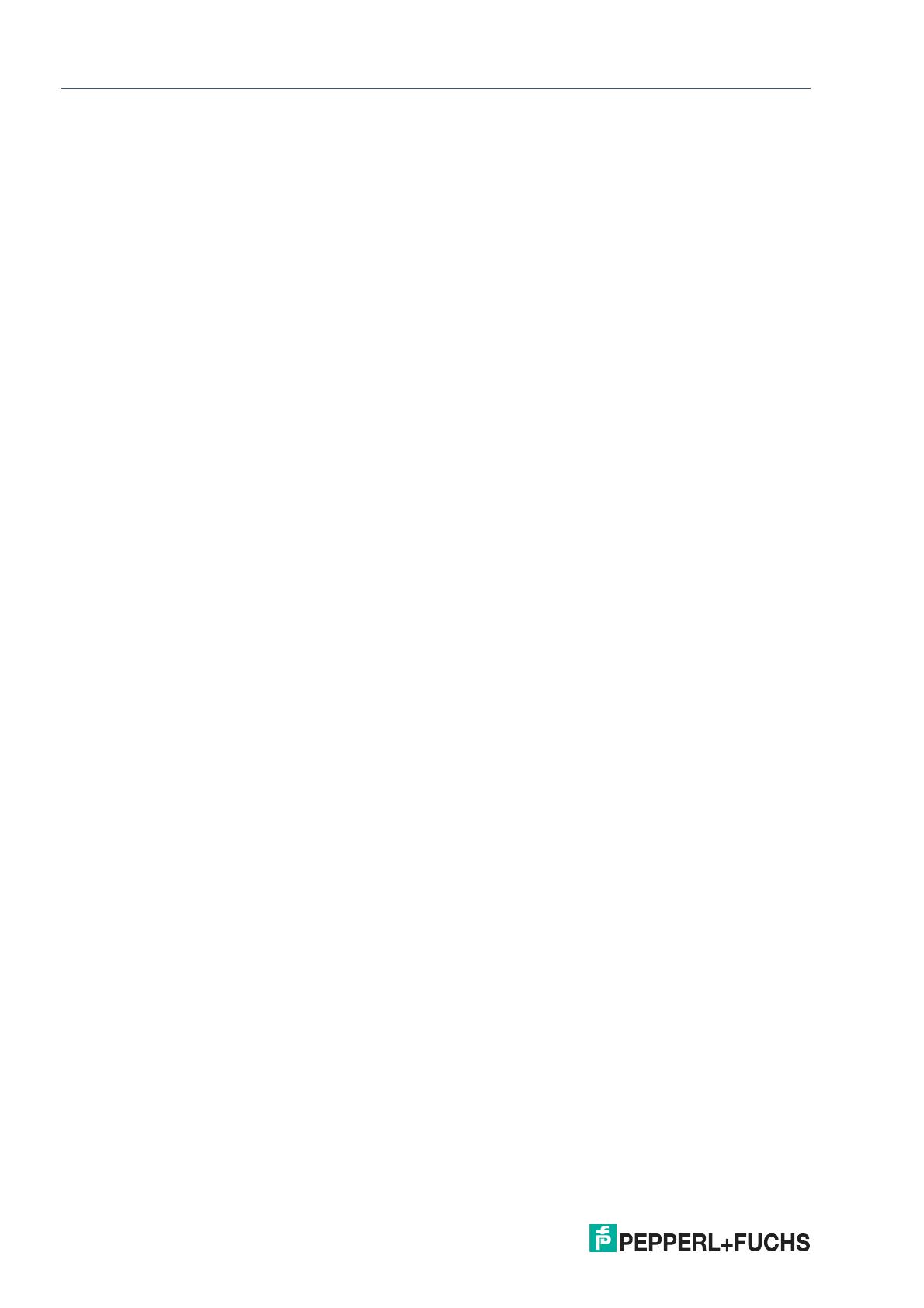
PANOS (Process Automation Network Operating System)
Contents
2023-07
4
6 Diagnostic Information and Troubleshooting .......................................................23
6.1 PROFINET Diagnosis...................................................................................24
6.2 LED Information ...........................................................................................25
6.3 Communication Statistics...........................................................................26
6.4 Ethernet-APL Physical Layer Information .................................................27
6.5 PROFIBUS PA Physical Layer Information ................................................27
6.6 Switch Device Diagnostics..........................................................................29
6.7 Uplink Ports and Spur Ports Diagnostics..................................................30
6.8 Uplink Ports Diagnostics.............................................................................31
6.9 Spur Ports Diagnostics ...............................................................................31
6.10 Spur Ports Diagnostics with Ethernet-APL Device...................................32
6.11 Spur Ports Diagnostics with PROFIBUS PA Device..................................33
7 Maintenance .............................................................................................................36
8 Asset Management ..................................................................................................37
8.1 Web Server ...................................................................................................37
8.1.1 User Interface Basics........................................................................................................ 37
8.1.2 Dashboard ........................................................................................................................ 39
8.1.3 Diagnostics ....................................................................................................................... 41
8.1.3.1 Diagnostics / Overview .......................................................................................................... 41
8.1.3.2 Diagnostics / Details .............................................................................................................. 43
8.1.3.3 Diagnostics / Network............................................................................................................ 49
8.1.3.4 Diagnostics / Device .............................................................................................................. 52
8.1.3.5 Event Log .............................................................................................................................. 53
8.1.3.6 Data History........................................................................................................................... 56
8.1.3.7 Snapshots ............................................................................................................................. 57
8.1.3.8 Diagnostics / Physical layer ................................................................................................... 57
8.1.4 Configuration .................................................................................................................... 58
8.1.4.1 Configuration / Diagnosis ...................................................................................................... 58
8.1.4.2 Configuration / Network ......................................................................................................... 59
8.1.4.3 Configuration / Device ........................................................................................................... 62
8.1.5 Expert ............................................................................................................................... 69
8.1.5.1 Diagnosis Data Download ..................................................................................................... 69
8.1.6 Downloads........................................................................................................................ 69
8.1.6.1 Downloads / Documents........................................................................................................ 69
8.1.6.2 Downloads / Certificates........................................................................................................ 69
8.1.6.3 Downloads / Drivers .............................................................................................................. 69
8.1.6.4 Downloads / Licenses............................................................................................................ 69
8.1.7 Help .................................................................................................................................. 69
8.1.7.1 Support.................................................................................................................................. 69
8.2 Pepperl+Fuchs Discovery and Configuration Tool (PFDCT)....................70