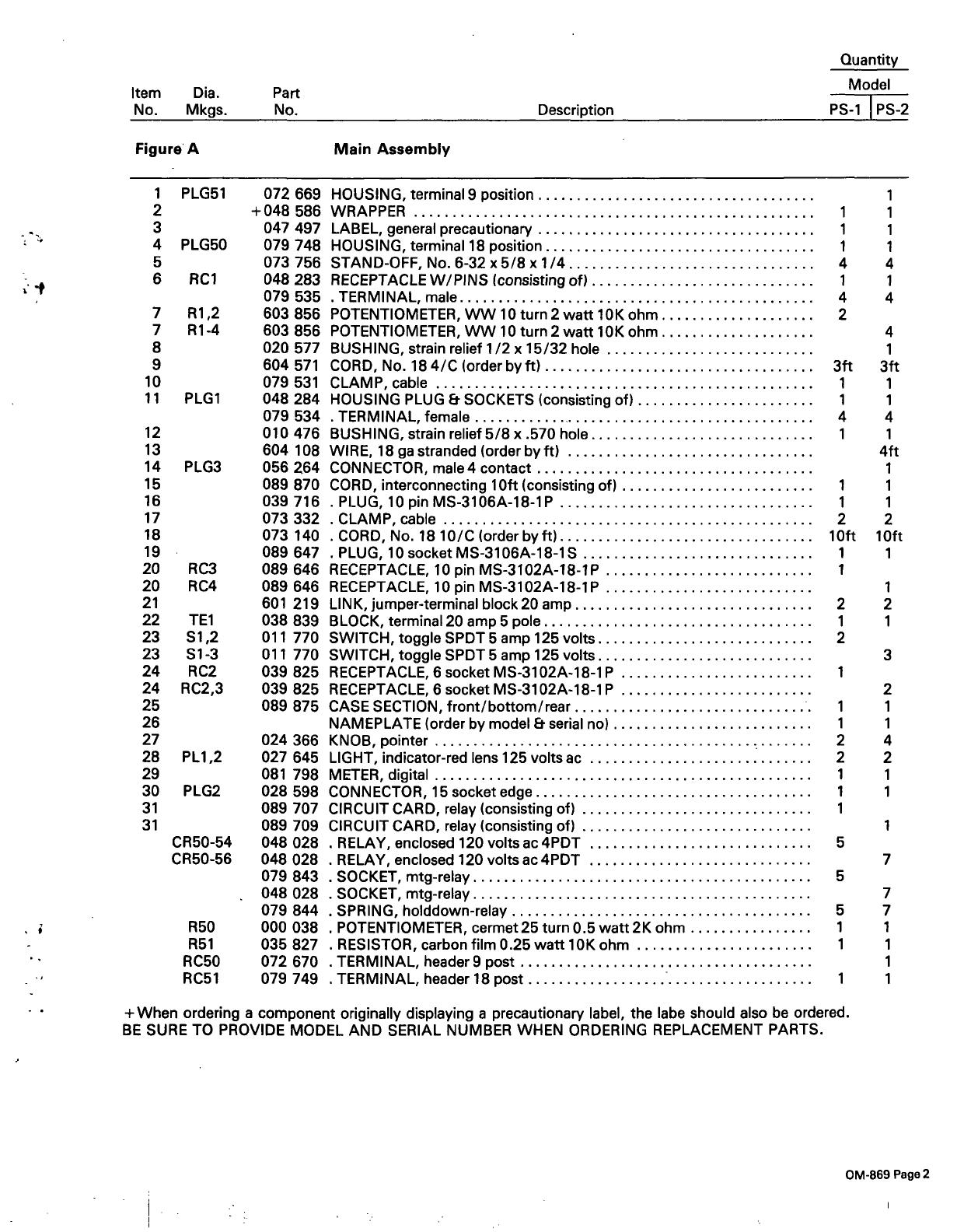
Quantity
Model
Item
Dia.
Part
No.
Mkgs.
No.
Description
PS-i
I
PS-2
Figure
A
Main
Assembly
1
PLG51
072
669
HOUSING,
terminal
9
position
1
2
+048
586
WRAPPER
1
1
3
047
497
LABEL,
general
precautionary
1
4
PLG5O
079
748
HOUSING,
terminal
18
position
1
1
5
073
756
STAND-OFF,
No.
6-32
x
5/8
x
1/4
4
4
6
RC1
048
283
RECEPTACLE
W/
PINS
(consisting
of)
1
079
535
.
TERMINAL,
male
4
4
7
R1,2
603
856
POTENTIOMETER,
WWi0turn2watt
10K
ohm
2
7
R1-4
603
856
POTENTIOMETER,
WWl0turn2watt
10K
ohm
4
8
020
577
BUSHING,
strain
relief
1/2
x
15/32
hole
1
9
604
571
CORD,
No.
184/C
(order
by
ft)
3ft
3ft
10
079531
CLAMP,cable
1
1
11
PLG1
048
284
HOUSING
PLUG
&
SOCKETS
(consisting
of)
1
1
079
534
.
TERMINAL,
female
4
4
12
010
476
BUSHING,
strain
relief
5/8
x
.570
hole
1
13
604
108
WIRE,
l8gastranded(orderbyft)
4ft
14
PLG3
056
264
CONNECTOR,
male
4
contact
1
15
089
870
CORD,
interconnecting
lOft
(consisting
of)
1
16
039716
.PLUG,iOpinMS-3106A-i8-1P
1 1
17
073
332
.
CLAMP,
cable
2
2
18
073
140
.CORD,No.
18
10/C
(orderbyft)
lOft
lOft
19
089
647
.
PLUG,
l0socketMS-3106A-i8-1S
1
1
20
RC3
089
646
RECEPTACLE,
10
pin
MS-3102A-18-1P
1
20
RC4
089
646
RECEPTACLE,
i0pinMS-3i02A-18-1P
1
21
601
219
LINK,jumper-terminalblock20amp
2
2
22
TEl
038
839
BLOCK,
terminal
20
amp
5
pole
1 1
23
S1,2
011
770
SWITCH,toggleSPDT5ampi25volts
2
23
S1-3
011
770
SWITCH,toggleSPDT5ampl25volts
3
24
RC2
039
825
RECEPTACLE,6socketMS-3i02A-i8-1P
1
24
RC2,3
039
825
RECEPTACLE,6socketMS-3i02A-18-1P
2
25
089
875
CASE
SECTION,
front/bottom/rear
1
1
26
NAMEPLATE
(order
by
model
&
serial
no)
1
1
27
024
366
KNOB,
pointer
2
4
28
PL1,2
027
645
LIGHT,
indicator-red
lens
125
voltsac
2
2
29
081
798
METER,
digital
1
30
PLG2
028
598
CONNECTOR,
15
socket
edge
1
1
31
089
707
CIRCUIT
CARD,
relay
(consisting
of)
31
089
709
CIRCUIT
CARD,
relay
(consisting
of)
1
CR5O-54
048
028
.
RELAY,
enclosed
120
volts
ac
4PDT
5
CR5O-56
048
028
.
RELAY,
enclosed
120
volts
ac4PDT
7
079
843
.
SOCKET,
mtg-relay
5
048
028
.
SOCKET,
mtg-relay
7
079
844
.
SPRING,
hoiddown-relay
5
7
R50
000
038
.
POTENTIOMETER,
cermet25turnO.5watt2K
ohm
1 1
R51
035827
.RESISTOR,carbonfilm0.25wattl0Kohm
1
1
RC5O
072
670
.
TERMINAL,
header
9
post
1
RC51
079
749
.
TERMINAL,
header
18
post
1
1
+
When
ordering
a
component
originally
displaying
a
precautionary
label,
the
labe
should
also
be
ordered.
BE
SURE
TO
PROVIDE
MODEL
AND
SERIAL
NUMBER
WHEN
ORDERING
REPLACEMENT
PARTS.
OM-869
Page
2