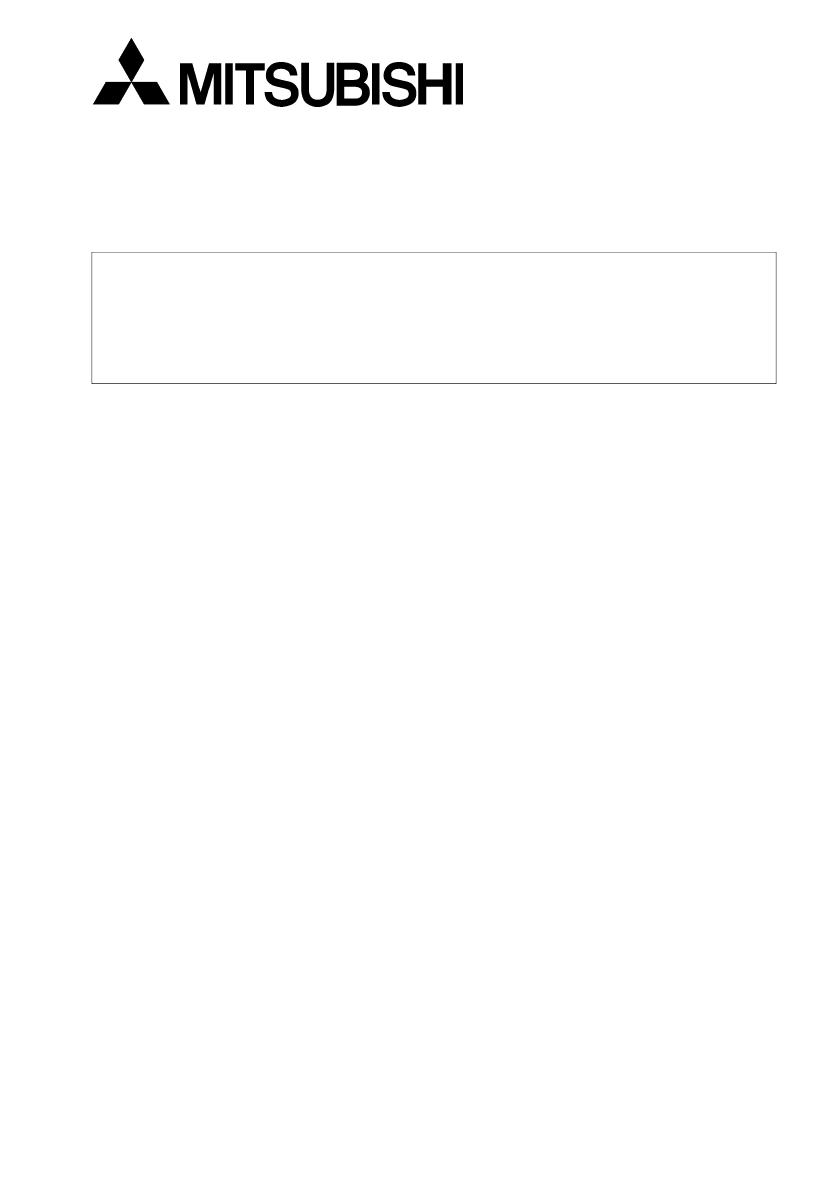
S
500
TRANSISTORIZED INVERTER
Thank you for choosing this Mitsubishi Transistorized inverter.
If this is the first time for you to use the FR-S500 series, please read through
this instruction manual (basic) carefully and use the inverter safely.
If you are going to use the inverter for higher-level applications, the FR-S500
instruction manual (detailed) [IB(NA)-0600027] is separately available from
where you purchased the inverter or your Mitsubishi sales representative.
INSTRUCTION MANUAL (BASIC)
FR-
CONTENTS
1. CONNECTION OF PERIPHERAL DEVICES..................................... 2
1.1 Basic Configuration ......................................................................2
2. INSTALLATION METHOD.................................................................. 5
2.1 Installation of the Inverter ............................................................. 5
3. SPECIFICATIONS OF WIRING AND TERMINALS............................ 6
3.1 Terminal connection diagram (Japanese version)........................ 6
3.2 Terminal connection diagram (North America version)................. 9
3.3 Terminal connection diagram (European version)...................... 13
3.4 Main Circuit................................................................................. 16
3.5 Control Circuit............................................................................. 16
4. OPERATION/CONTROL.................................................................. 20
4.1 Setting the Frequency to Perform Operation
(Example: Performing Operation at 30Hz).................................. 22
4.2 Using the setting dial like a potentiometer to perform operation.23
4.3 Setting the Parameters...............................................................24
4.4 Clearing the Parameters............................................................. 26
4.5 Monitoring the Output Current....................................................27
5. ADJUSTMENT OF THE FREQUENCY SETTING
POTENTIOMETER AND INDICATOR ............................................. 28
5.1 Changing the Output Frequency Setting of the Frequency
Setting Potentiometer (Bias and gain of frequency setting
voltage (current))........................................................................28
5.2 Adjustment (Calibration) of the Frequency Meter (Indicator)......31
6. FUNCTION LIST............................................................................... 32
6.1 Basic Function Parameter List....................................................32
6.2 Explanation of the Basic Function Parameters........................... 32
6.3 EXTENDED FUNCTION PARAMETER LIST............................. 34
7. ERRORS AND PROTECTIVE FUNCTIONS.................................... 44
7.1 About Errors (Definitions) ........................................................... 44
7.2 Inverter Reset............................................................................. 46
8. SPECIFICATIONS............................................................................ 47
8.1 Ratings ....................................................................................... 47
8.2 Common Specifications..............................................................51
9. OUTLINE DRAWINGS .....................................................................53
Appendix 1 Instructions for Compliance with the European
Standards.......................................................................... 55
Appendix 2 Instructions for compliance with U.S. and Canadian
Electrical Codes................................................................. 57