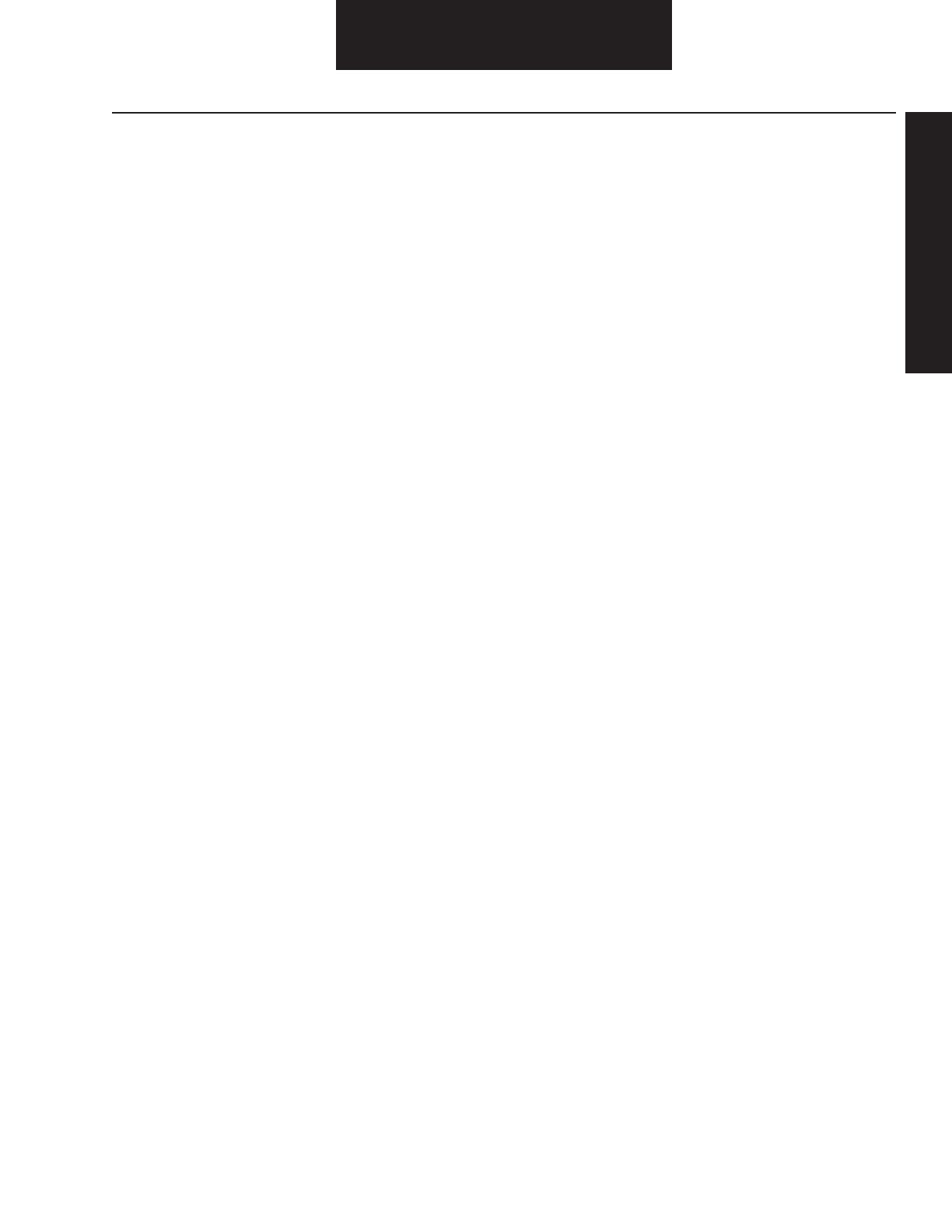
1
Table of Contents
General Information
Model Identifi cation . . . . . . . . . . . . . . . . . . . . . . . 2
Exploded View. . . . . . . . . . . . . . . . . . . . . . . . . . . 3
Specifi cations
Disc Brake ESD225. . . . . . . . . . . . . . . . . . . . . . . 4
Tightening Torque. . . . . . . . . . . . . . . . . . . . . . . . . 5
Wear Limits . . . . . . . . . . . . . . . . . . . . . . . . . . . . . 5
Description of Operation
Actuation/Release of the Brake . . . . . . . . . . . . . . 6
Self-Adjusting Adjustment . . . . . . . . . . . . . . . . . . 6
Application . . . . . . . . . . . . . . . . . . . . . . . . . . . . . . 7
Release . . . . . . . . . . . . . . . . . . . . . . . . . . . . . . . . 8
Safety Instructions. . . . . . . . . . . . . . . . . . . . . . . . 10
Service Instructions
Service Intervals. . . . . . . . . . . . . . . . . . . . . . . . . 11
Checking Pads. . . . . . . . . . . . . . . . . . . . . . . . 12
Checking Brake Disc. . . . . . . . . . . . . . . . . . . 12
Checking Sliding Function. . . . . . . . . . . . . . . 13
Checking Play in the Slide Pins. . . . . . . . . . . 13
Checking Boots for Slide Pins. . . . . . . . . . . . 14
Checking Bellows for Adjustment Screws . . . 14
Operating Test . . . . . . . . . . . . . . . . . . . . . . . . . . 15
Initial Adjustment . . . . . . . . . . . . . . . . . . . . . . . . 16
Lubrication . . . . . . . . . . . . . . . . . . . . . . . . . . . . . 16
General . . . . . . . . . . . . . . . . . . . . . . . . . . . . . 16
Adjustment Mechanism. . . . . . . . . . . . . . . . . 16
Slide Pins and Bushings . . . . . . . . . . . . . . . . 16
Replacing Pads
Removing Pads . . . . . . . . . . . . . . . . . . . . . . . . . 17
Replacing Pads . . . . . . . . . . . . . . . . . . . . . . . . . 17
Initial Adjustment . . . . . . . . . . . . . . . . . . . . . . . . 18
Replacing Disc Brake
Removing Disc Brake Caliper . . . . . . . . . . . . . . 19
Replacing Disc Brake Caliper . . . . . . . . . . . . . . 19
Replacing Slide Pins, Slide Bushings, and Boots
Removing Slide Pins, Slide Bushings,
and Boots. . . . . . . . . . . . . . . . . . . . . . . . . . . . . . 20
Inspection. . . . . . . . . . . . . . . . . . . . . . . . . . . . . . 22
Replacing Slide Bushings and Slide Pins . . . . . 22
Replacing Boots in Caliper. . . . . . . . . . . . . . . . . 23
Replacing Brake Chamber
Removing Brake Chamber. . . . . . . . . . . . . . . . . 25
Replacing Brake Chamber. . . . . . . . . . . . . . . . . 25
Replacing Spring Brake Chamber
Removing Spring Brake Chamber. . . . . . . . . . . 26
Replacing Spring Brake Chamber . . . . . . . . . . . 27
Replacing Rotor
Removing Rotor. . . . . . . . . . . . . . . . . . . . . . . . . 28
Replacing Rotor. . . . . . . . . . . . . . . . . . . . . . . . . 28
Rotor Runout Check. . . . . . . . . . . . . . . . . . . . . . 28
Cleaning and Inspection. . . . . . . . . . . . . . . . . . . 29
Rotor Resurfacing . . . . . . . . . . . . . . . . . . . . . . . 29
Troubleshooting . . . . . . . . . . . . . . . . . . . . . . . . . . 30
Table of Contents