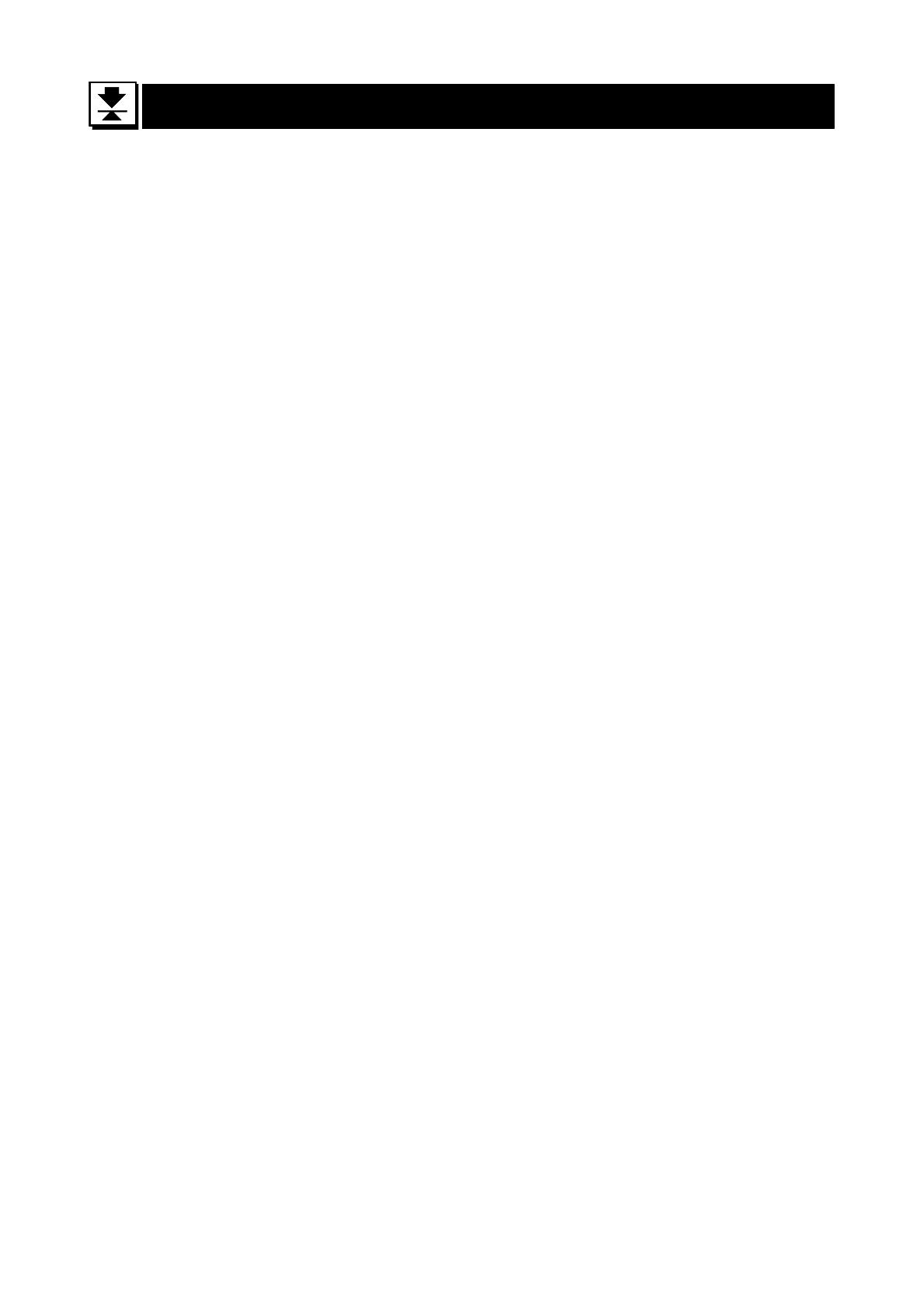
1
Contents
1. About This Manual ...........................................................................................................2
2. Introduction...................................................................................................................2
3. Description of Each Part...............................................................................................3
3.1. Status LEDs........................................................................................................3
3.2. Communication Connector..................................................................................4
4. Installation ....................................................................................................................5
4.1. Interface Module Installation...............................................................................5
4.2. Network Configuration.........................................................................................6
4.3. Setting the Functions ..........................................................................................6
5. PLC Memory.................................................................................................................8
5.1. Address Map.......................................................................................................8
5.1.1. OUT Data (6 words), PLC → AD-4408A.........................................................8
5.1.2. IN Data (10 words), AD-4408A → PLC.........................................................10
5.2. Handling Bits Directly........................................................................................13
5.2.1. Handling Command Bits ...............................................................................13
5.2.2. Command bit execution procedure ...............................................................13
5.3. Operation by Commands..................................................................................14
5.3.1. Handling Commands.....................................................................................14
5.3.2. Command execution procedure....................................................................14
5.4. Commands........................................................................................................15
6. Timing Chart...............................................................................................................16
6.1. Read Command................................................................................................16
6.2. Write Command................................................................................................16
7. Errors..........................................................................................................................18
7.1. Error Types.......................................................................................................18
8. Check Mode
...............................................................................................................19
8.1. Checking the PROFIBUS Communication Status.............................................19
8.1.1. Entering the Check Mode..............................................................................19
8.1.2. Checking the Communication Status............................................................20