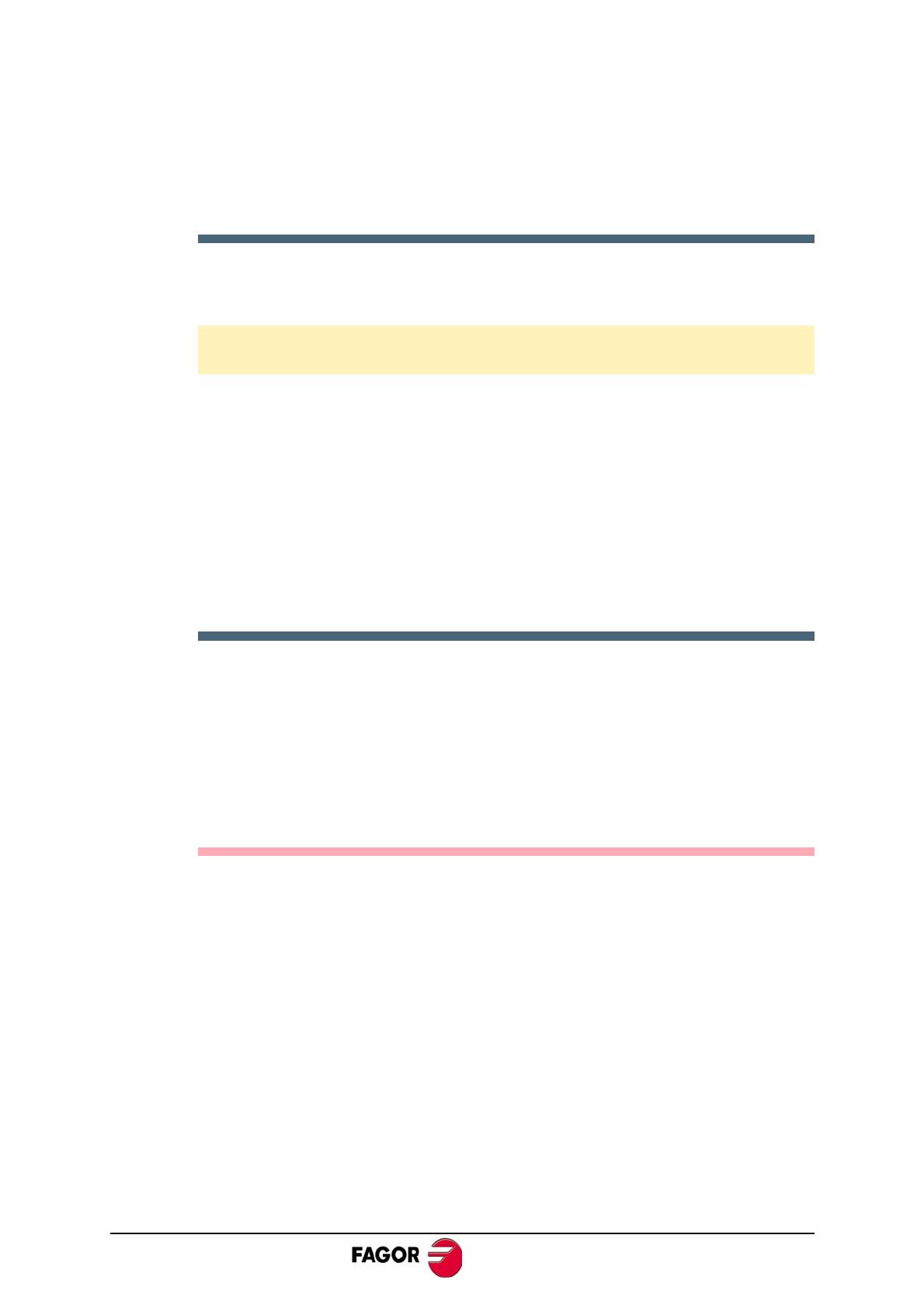
16/40 - CANopen protocol MCP/MCPi - Ref.0612
where:
<SYNC> means that the transmission of the PDO has to do with the reception
of the synchronism message.
<ASYNC> means that the transmission of the PDO has nothing to do with the
reception of the synchronism message.
Type of transmission = 0.Synchronous and non-cyclic. The messages are only sent
when an event takes place and, in that case, the message is sent in synchronism
with the next synchronism message.
Type of transmission = 1 to 240.The PDO is transmitted after receiving the
number of synchronism messages specified in the type of transmission.
Type of transmission = 252 to 253. Values only possible in transmission PDO's.
In either case, the PDO is sent as response to an RTR frame of the master element.
The difference is that in the type of transmission = 252 it updates the variables
when receiving the synchronism and the transmission = 253 updates the variables
and sends them when receiving the RTR frame.
Type of transmission = 254.The PDO is transmitted when some OEM-specific
event occurs.
Type of transmission = 255. The PDO is transmitted when some device-profile-
specific event occurs.
Value of subindex 3 ( inhibit time or disable time)
It indicates the minimum time interval (in 100 µs increments ) elapsed between
PDO's. This time interval cannot be changed while the value of bit 31 of subindex
1 (COB ID) is 0 (the PDO exists).
Value of subindex 5 (event timer)
It indicates the value of the event timer (in 1 ms increments) when the transmission
type is 254 or 255.
Example to explain the meaning of the "time inhibit" and the "event timer".
When programming a type-254 transmission PDO that includes a position variable,
two different scenarios occur. As long as the element to send the PDO is stopped
(its position has not changed), it will not have to be sent. When programming a 10
ms event timer, even if the element does not change its position (it does not move),
it will send PDO's every 10 ms indicating its position. When starting the movement,
it will try sending PDO's constantly, thus taking up the whole bus with this information.
In order to avoid this situation, an inhibit time of 2 may be programmed so it only sends
PDO's every 2 ms while it is moving.
An event is a change of value of the variable or (if it is supported by the equipment,
communication objects with subindex 5).