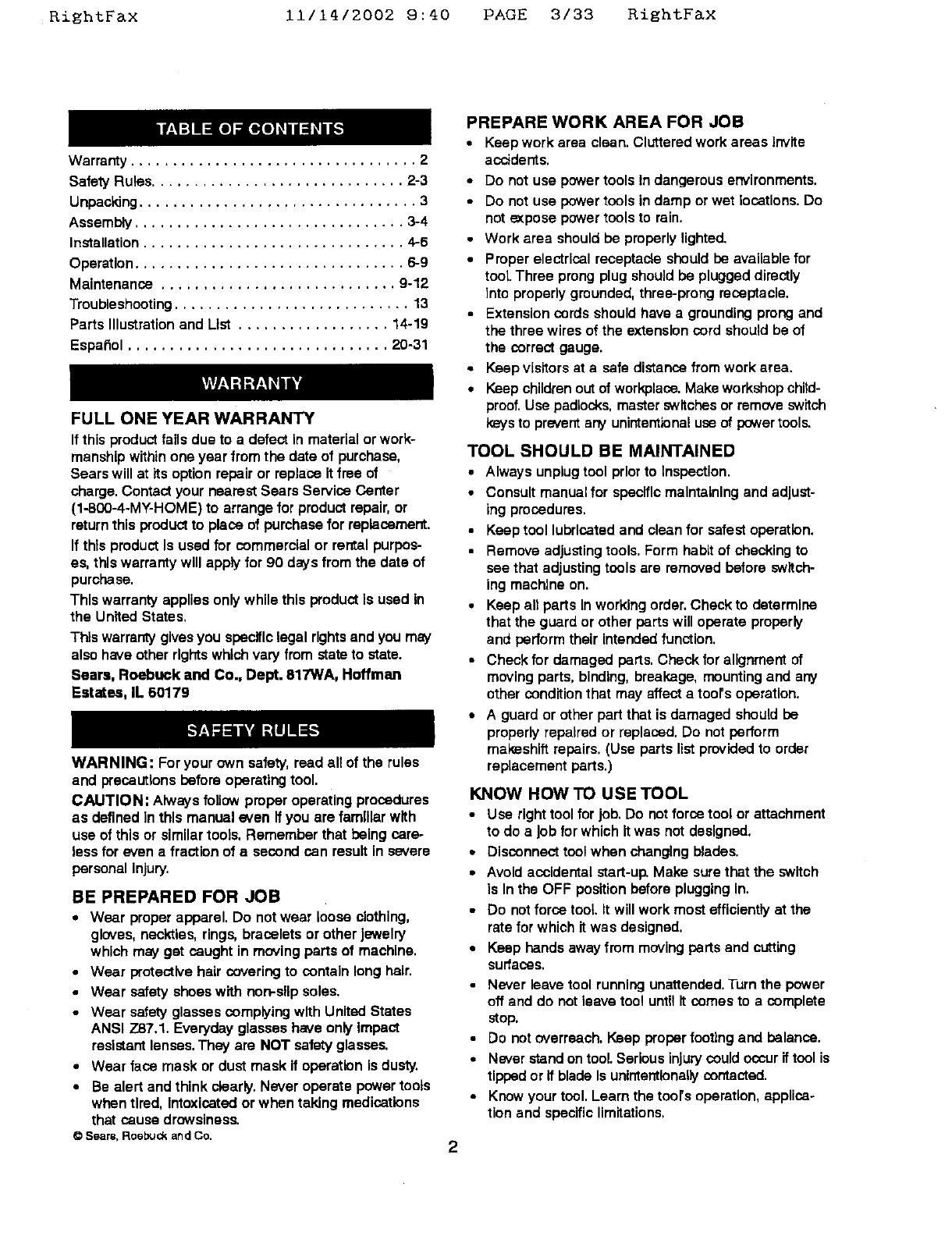
RightFax ii/14/2002 9:40 PAGE 3/33 RightF&x
Warranty .................................. 2
Safety Rules.............................. 2-3
Unpacking................................. 3
Assembly ................................ 3-4
Installation ............................... 4-6
Operation ................................ 6-9
Maintenance ............................ 9-12
TroubLeshooting............................ 13
Parts Illustration and LIst .................. 14-19
EspeSol ............................... 20-31
FULL ONE YEAR WARRANTY
If this product fails due to a defectin materialor work-
manshipwithinone yearfrom the dateof purchase,
Searswillat itsoption repairor replaceItfreeof
charge.Contactyour nearestSears ServiceCenter
(1-800-4-MY-HOME) to arrangefor productrepair,or
returnthisprodu_ to place of purchasefor replacement.
If thlsproductIs usedfor commercialor rentalpurpos-
es, thiswarrantywill applyfor 90 days fromthe date of
purchase.
Thiswarrantyappliesonlywhilethis productIs used In
the United States.
This warrantygivesyou specificlegal rights and youmay
also have otherrightswhichvaryfromstate to state.
Sears, Roebuck and Co., Dept. 817WA, Hoffman
Estates, IL 60179
WARNING: For yourown safety,read all of the rules
and precautions beforeoperatingtool.
CAUTION; Always follow properoperatingprocedures
as definedInthis manual even Ifyou are familiar with
use ofthis or similartools,Remember that being care-
less foreven a fractionof a secondcan resultIn severe
personalInjury.
BE PREPARED FOR JOB
• wear properapparel. Do notwear loose clothing,
gloves,neckties,rings,braceletsor otherJewelry
which may get caughtin moving partsof machine.
• Wear protectivehaircoveringto containlong hair.
• Wear safety shoeswith non-slip soles.
• Wear safetyglassescomplyingwith UnitedStates
ANSI 7.87.1.Everydayglasseshave onlyImpact
resistantlenses.They are NOT safetyglasses.
• Wear face mask or dustmask ifoperationIs dusty.
• Be alert and thinkclearly.Never operatepowertools
when tired, Intoxicated or when taking medications
that causedrowsiness.
© Sears, Roebud_and Co.
2
PREPARE WORK AREA FOR JOB
• Keepwork area clean.Clutteredwork areas invite
accidents.
• Do notuse powertoolstn dangerousenvironments.
• Do notuse powertoolsin damp or wet locations. Do
notexpose powertoolsto rain.
• Work area shouldbe properlylighted.
• Proper electricalreceptacleshouldbe availablefor
tool Three prongplug shouldbe pluggeddirectly
into properly grounded, three-prongreceptacle.
• Extensioncords shouldhavea groundingprongand
thethree wires ofthe extensioncord shouldbeof
the correctgauge.
• Keep visitorsat a safe distancefrom work area.
• Keepchildrenoutofworkplace.Makeworkshopchild-
proof. Usepadlocks,master switchasor removeswitch
kaysto preventany unintentionaluseof powertools.
TOOL SHOULD BE MAINTAINED
• Always unplugtool priorto Inspection.
• Consultmanualfor specificmaintaining and adjust-
ingprocedures,
• Keeptoollubricatedand cleanfor safestoperation.
• Removeadjustingtools.Formhabitofcheckingto
see thatadjustingtoolsare removedbeforeswitch-
ingmachineon.
• Keepan parts Inworkingorder.Check to determine
thatthe guard or otherparts willoperate properly
and perform their intendedfunction,
• Checkfor damaged parts.Check for alignmentof
movingparts, binding,breakage, mountingand any
otherconditionthat may affecta toots operation.
• A guardor other partthat isdamaged shouldbe
properlyrepairedor replaced.Do notperform
makeshiftrepairs.(Use parts listprovidedto order
replacementparts.)
KNOW HOW TO USE TOOL
• Use righttoolfor job. Do notforcetoolor attachment
to do a Jobforwhichitwas not designed.
• Disconnecttoolwhen changingblades.
• Avoidacoidentaistart-ul_ Make surethatthe switch
Is Inthe OFF positionbeforepluggingin.
• Do notforcetool, It willwork most efficientlyat the
ratefor whichitwas designed,
• Keep hands awayfrom movingparts and cutting
surfaces.
• Never leavetool runningunattended.Turnthe power
offend do notleave tooluntilit comes to a complete
stop,
• Do not overreach.Keep proper footing and balance.
• Never standontool.Seriousinjurycouldoccuriftoolis
tippedor ifbladeIs unintentionallycontacted.
• Knowyourtool.Learnthe tool'soperation,applica-
tionand specificlimitations,