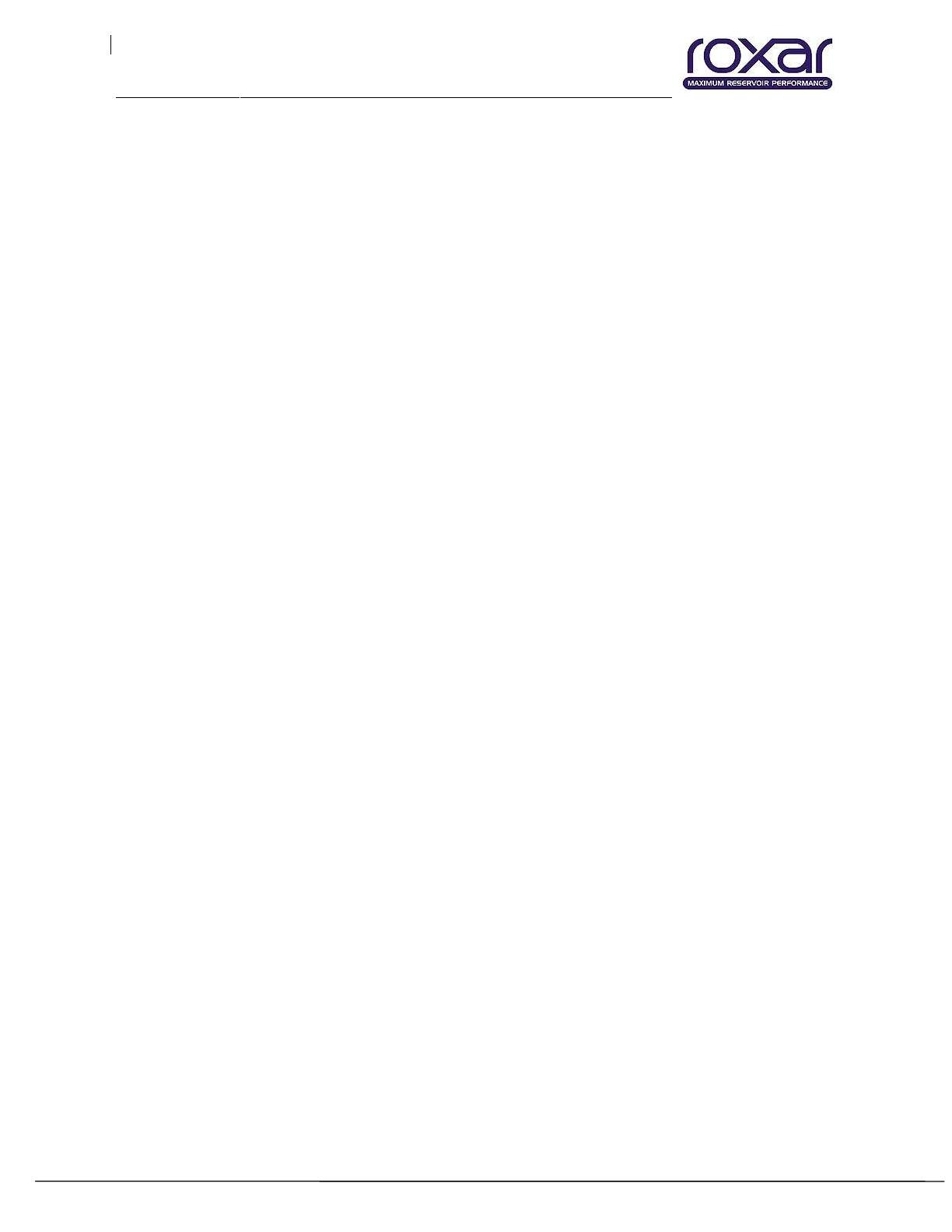
Document no.: 020085/F
Document
name:
Roxar subsea Sand monitor and Pig detector functional
design specification
Page 2 of 22
TABLE OF CONTENTS
Table of Contents ................................................................................................................... 2
1.
Purpose .......................................................................................................................... 3
2.
Abbreviations................................................................................................................... 3
3.
Roxar subsea acoustic detector .........................................................................................4
3.1
Introduction............................................................................................................. 4
3.2
Detector unit ........................................................................................................... 4
3.2.1
Detector unit in funnel /retrievable version ............................................................. 4
3.2.2
Detector unit in tube fixture /non-retrievable version............................................... 6
3.2.3
Interface connector type ....................................................................................... 6
3.2.4
Oil filled jumper....................................................................................................6
4.
Roxar subsea Sand monitor ..............................................................................................7
4.1
Introduction............................................................................................................. 7
4.2
Mounting location..................................................................................................... 7
4.3
Operation principle and calibration.............................................................................8
4.3.1
Background noise compensation ............................................................................8
4.3.2
Sand calibration....................................................................................................8
4.4
Sand rate calculation ................................................................................................9
4.4.1
Sand calculation input / equations........................................................................ 10
4.5
Detector sensitivity................................................................................................. 11
5.
Roxar subsea Pig detector .............................................................................................. 13
5.1
Introduction........................................................................................................... 13
5.2
Mounting location................................................................................................... 13
5.3
Operating principle................................................................................................. 13
5.3.1
Basic detection principle...................................................................................... 14
5.3.2
Sensitivity .......................................................................................................... 14
5.4
Configuration and set-up ........................................................................................ 14
5.4.1
Configuration ..................................................................................................... 14
5.4.2
Set-up ............................................................................................................... 14
5.5
Debris indicator...................................................................................................... 15
6.
Design specifications ...................................................................................................... 16
6.1
General ................................................................................................................. 16
6.1.1
Detector body .................................................................................................... 16
6.1.2
Funnel ............................................................................................................... 16
6.1.3
Tube fixture ....................................................................................................... 16
6.1.4
Power supply and communication ........................................................................ 16
6.2
Operational features............................................................................................... 17
6.3
Optional ................................................................................................................ 17
6.4
Mechanics.............................................................................................................. 17
6.4.1
General design specifications ............................................................................... 17
6.4.2
Coating and cathodic protection (CP) ................................................................... 18
6.5
Electrical specifications ........................................................................................... 19
6.5.1
Isolation with respect to chassis earth .................................................................. 19
6.5.2
Redundancy ....................................................................................................... 19
6.5.3
Power interface .................................................................................................. 19
6.5.4
Available signal interfaces.................................................................................... 20
6.5.5
EMI susceptibility................................................................................................ 21
6.5.6
Electrical interfaces............................................................................................. 21
6.5.7
Options.............................................................................................................. 21
6.6
Approvals and standards......................................................................................... 22
7.
References .................................................................................................................... 22