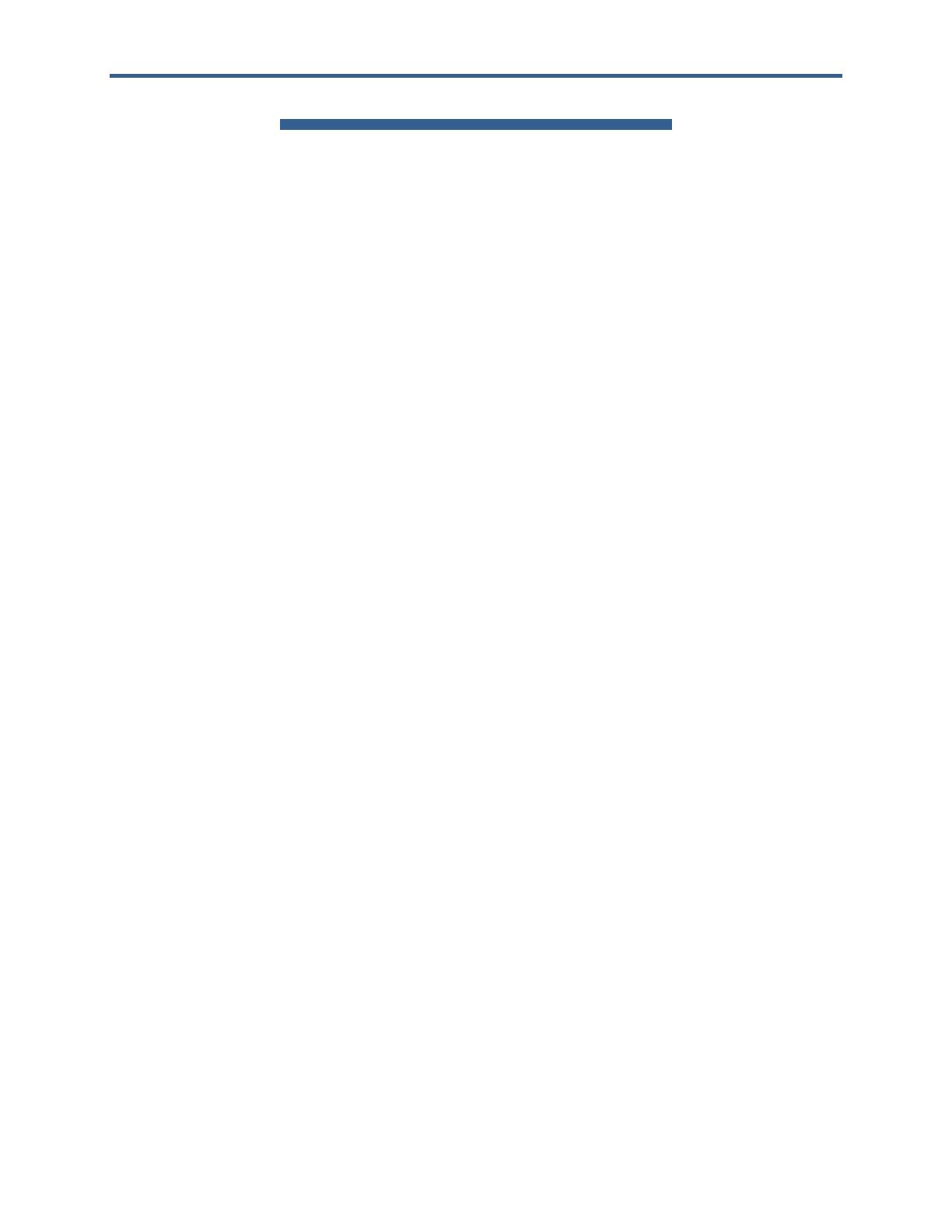
Manual 35018V3 505XT Dual Redundant Control System for Steam Turbines
Illustrations and Tables
Figure 15-1. Typical Redundant 505XT Application Configuration ............................................................... 9
Figure 16-1. 505DR with FTM ..................................................................................................................... 12
Figure 16-2. Single Coil Shared Driver ....................................................................................................... 17
Figure 16-3 Single Coil Shared Driver with 505DR FTM ............................................................................ 17
Figure 16-4 Dual Coil Driver........................................................................................................................ 18
Figure 16-5. Dual Coil Driver with 505DR FTM .......................................................................................... 18
Figure 16-6. Redundant (Parallel) Actuator Driver ..................................................................................... 19
Figure 16-7. Redundant (Parallel) Actuator Driver with 505DR FTM ......................................................... 19
Figure 16-8. Actuator Driver with Redundant Demands ............................................................................. 20
Figure 16-9. Actuator Type Configuration ................................................................................................... 23
Figure 16-10. Driver Channel Configuration ............................................................................................... 24
Figure 16-11. mA Backup Channel Configuration ...................................................................................... 25
Figure 16-12. Driver Configuration Page Buttons ....................................................................................... 26
Figure 16-13. Servo Position Controller ...................................................................................................... 27
Figure 16-14. SPC Driver CAN Links .......................................................................................................... 28
Figure 16-15a. SPC Driver Configuration for Redundant Actuators ........................................................... 29
Figure 16-15b. SPC Driver Configuration for Redundant Actuators ........................................................... 30
Figure 16-15c. SPC Driver Configuration for Redundant Actuators ........................................................... 31
Figure 16-15d. SPC Driver Configuration for Redundant Actuators ........................................................... 32
Figure 16-15e. SPC Driver Configuration for Redundant Actuators ........................................................... 33
Figure 16-15f. SPC Driver Configuration for Redundant Actuators ............................................................ 33
Figure 16-15g. SPC Driver Configuration for Redundant Actuators ........................................................... 34
Figure 16-16a. SPC Driver Configuration for Dual Coil Actuators .............................................................. 34
Figure 16-16b. SPC Driver Configuration for Dual Coil Actuators .............................................................. 35
Figure 16-17. Expandable I/O Node 26 Driver (bumpless SYSCON transfer) ........................................... 37
Figure 16-18. Single Network Modbus Architecture ................................................................................... 38
Figure 16-19. Redundant Network Modbus Architecture ............................................................................ 38
Figure 17-1. Wait Run Permissive Screen .................................................................................................. 63
Figure 17-2. Navigating to the DR Overview Screen .................................................................................. 64
Figure 17-3. System Diagnostics Screen .................................................................................................... 66
Figure 17-4. Primary/Secondary SYSCON/BACKUP Indications............................................................... 67
Figure 17-5. Front Panel CPU LED SYCON/BACKUP Indication .............................................................. 68
Figure 17-6. SYSCON I/O Monitoring Pages.............................................................................................. 70
Figure 17-7. BACKUP Unit Available Screen ............................................................................................. 71
Figure 17-8. BACKUP Unit Inhibited Screen .............................................................................................. 72
Figure 17-9. BACKUP I/O Monitoring Menu ............................................................................................... 73
Figure 17-10 BACKUP Analog Inputs Screen ............................................................................................ 74
Figure 17-11. BACKUP Speed Inputs Screen ............................................................................................ 74
Figure 17-12. BACKUP Analog Outputs Screen ........................................................................................ 75
Figure 17-13. BACKUP Actuator Outputs Screen ...................................................................................... 76
Figure 17-14. BACKUP Boolean Inputs Screen ......................................................................................... 77
Figure 17-15. BACKUP Relay Outputs Screen........................................................................................... 77
Figure 17-16. User SYSCON Transfer Command ...................................................................................... 79
Figure 17-17. User Unsync Backup Command .......................................................................................... 80
Figure 17-18. User Reset Backup Command ............................................................................................. 80
Figure 17-19. System Diagnostic Faults Cleared ....................................................................................... 81
Figure 17-20. BACKUP Available ............................................................................................................... 82
Figure 17-21. Session connections dialog box ........................................................................................... 83
Figure 17-22. Actuator Output Failover Performance ................................................................................. 84
Figure 17-23. RTCNet Node 26 Analog Output Performance .................................................................... 84
Figure 17-24. SPC Analog Output Performance......................................................................................... 85