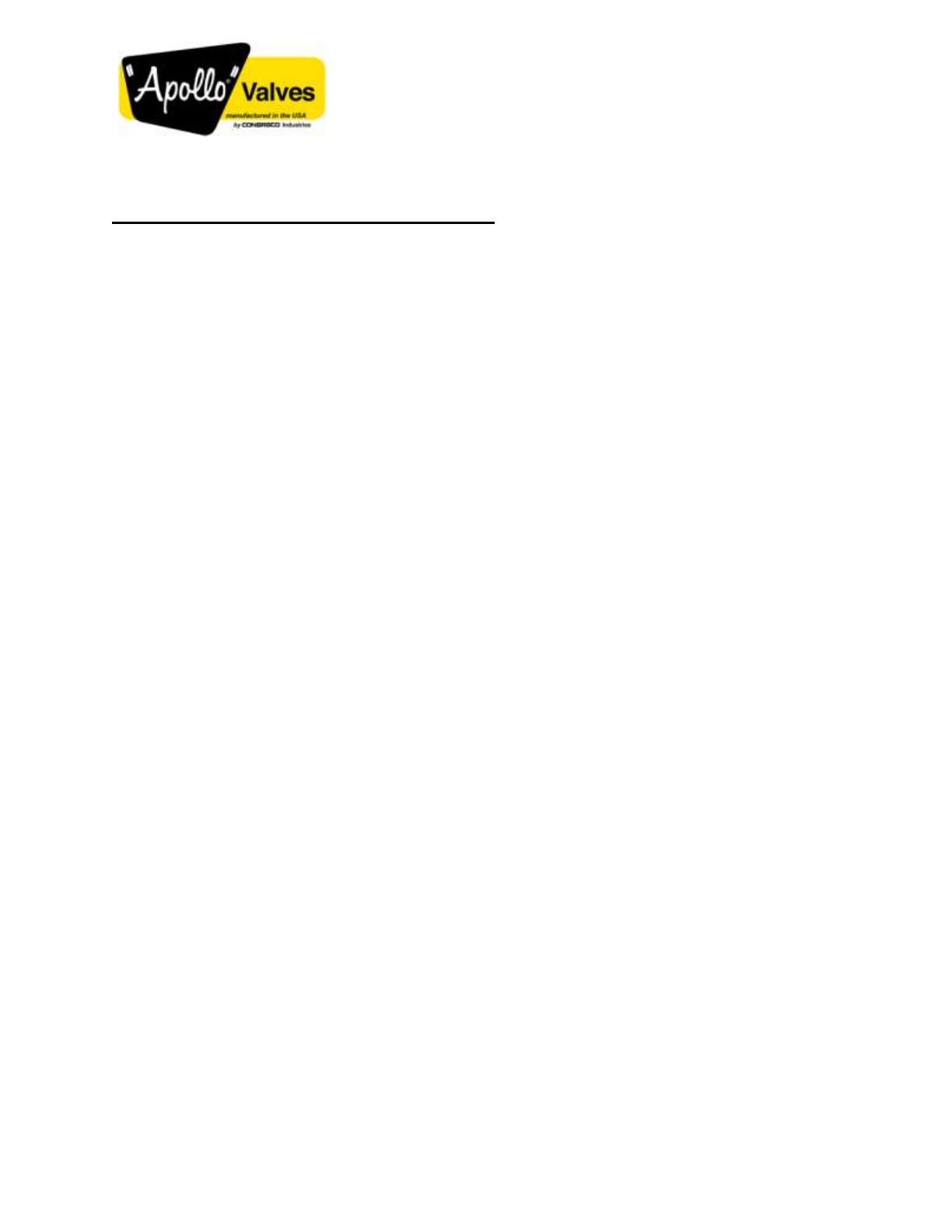
Office Address: 701 Matthews-Mint Hill Road, Matthews, North Carolina 28105
Soldering of Apollo Lead-Free Alloys
Rev. 7/18/2012
With the increasing use of lead-free¹ brass and bronze alloys for valve construction,
concerns regarding soldering have arisen because of the multitude of lead free alloys,
both domestic and foreign, introduced over the past ten or so years. Apollo has been
careful to select lead free alloys for use in our products that retain the ease and
confidence of soldering our customers have grown to expect of the standard brass and
bronze alloys we have been using for decades. We have conducted extensive
soldering tests in our R&D Laboratory in search of alloys that would make the transition
from leaded brass and bronze alloys to lead free alloys transparent for our customers.
A critical element of this change was to have the lead free alloys capable of being
soldered in the same manner and with the same solders and fluxes commonly used for
the standard brass and bronze alloys.
Alloys
Apollo has used C36000 free machining brass for nearly all of its 85 years of existence.
We have poured both C83600 and C84400 bronze in our US based foundry operations
for decades. C84400 is the more common material used n plumbing applications.
Our Brass Foundry, Machining, Assembly & Test, and R&D facilities are located in
Pageland, SC. Since we are in the same location, we were able, as a team, to conduct
extensive testing and development, both in process and product performance, of a
number of lead-free casting alloys. C89836 was selected as our material of choice for
lead-free products.
We purchase brass bar from US suppliers for our brass machining operation, also
located in Pageland. We worked closely with the suppliers to find a lead free material
that was close in performance to the C36000. Again, after extensive testing, C27450
was selected.
Thermal Conductivity
A consideration in selecting lead-free materials was to have the thermal conductivity of
the lead free alloy close to the standard alloy being replaced by the lead-free material.
Having similar thermal conductivity would mean that the plumber or technician would
not have to change the soldering process that they are familiar with when soldering lead
free materials. Note the similarity of the thermal conductivity for the lead free alloys and
standard alloys shown below.
Conbraco Industries, Inc.
Post Office Box 247
Matthews, N.C. 28106
Telephone (704) 847-9191
Sales Fax (704) 841-6021