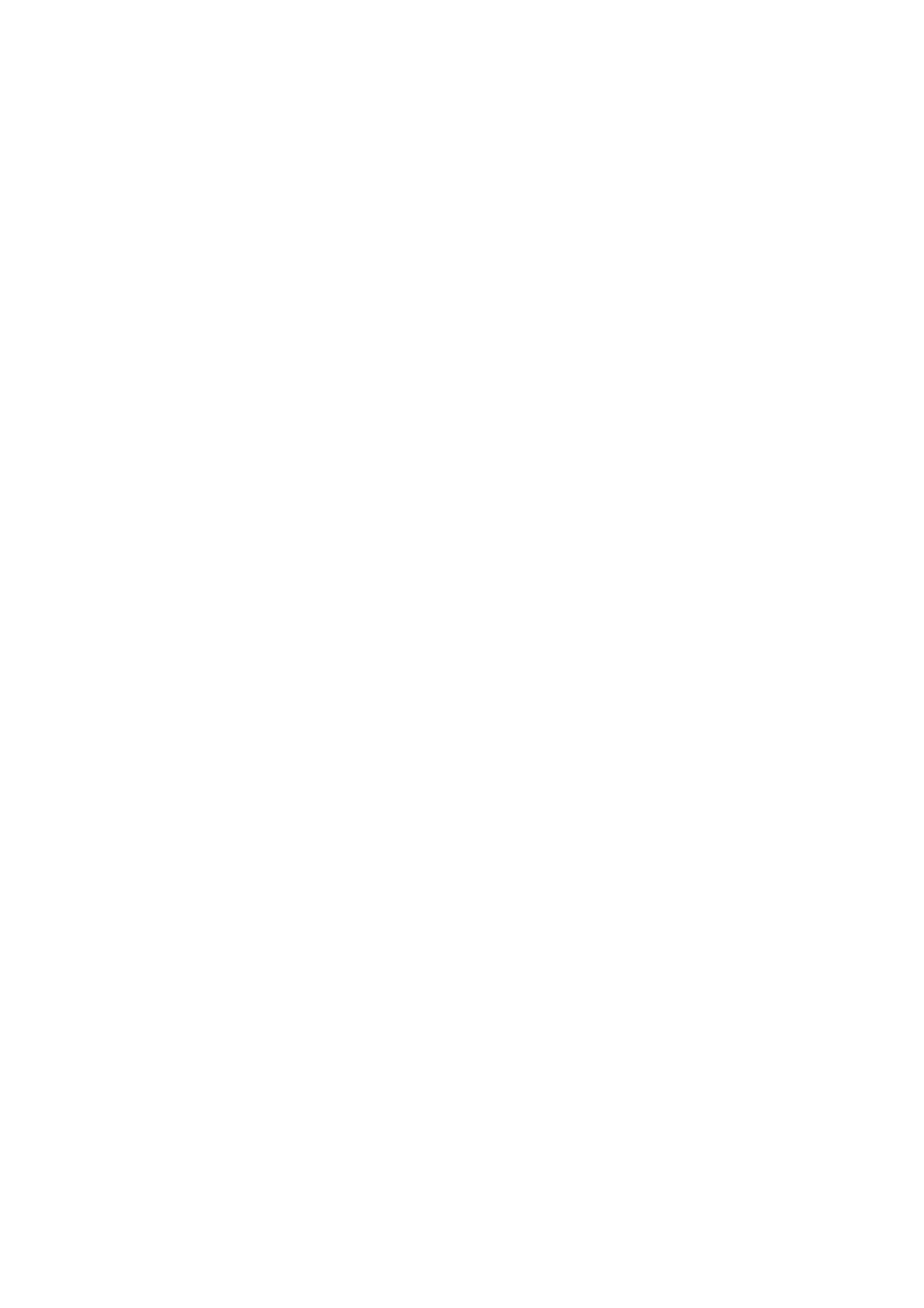
4.2 Connection of Control Unit .......................................................................................83
4.2.1 Control Unit Connection System Drawing.........................................................83
4.2.2 Connecting with Power Supply .........................................................................84
4.2.3 Connecting with Emergency Stop Signal..........................................................85
4.2.4 Connecting with Operation Panel I/O Unit ........................................................87
4.2.5 Connecting with Servo Drive Unit .....................................................................88
4.2.5.1 Connecting with MDS-D/DH Series...........................................................89
4.2.5.2 Connecting with MDS-DM Series ..............................................................92
4.2.5.3 Connecting with MDS-SVJ3/SPJ3 Series..................................................97
4.2.6 Connecting I/O Devices via CC-Link.................................................................98
4.2.7 Connecting with RS-232C Device...................................................................100
4.2.8 Connecting with Skip Signal (Sensor).............................................................102
4.2.9 Connecting with Synchronous Feed Encoder/ Manual Pulse Generator........104
4.3 Connection of Operation Panel I/O Unit.................................................................105
4.3.1 Operation Panel I/O Unit Connection System Drawing...................................105
4.3.2 Connecting with Keyboard Unit.......................................................................106
4.3.3 Connecting with Manual Pulse Generator (MPG)...........................................107
4.3.4 Connecting with Machine Operation Panel.....................................................108
4.3.4.1 Wiring for Sink Type Output (FCU7-DX710/DX720/DX730)....................109
4.3.4.2 Wiring for Source Type Output (FCU7-DX711/DX721/DX731) ...............110
4.3.4.3 Outline of Analog Signal Output Circuit ...................................................111
4.4 Connection of Remote I/O Unit...............................................................................112
4.4.1 Connection and Station No. Setting on Remote I/O Unit ................................112
4.4.2 Station No. Setting when Using Multiple Remote I/O Units ............................114
4.4.3 Connecting FCUA-DX10*/14* Unit with Machine Control Signal ....................118
4.4.4 Connecting FCUA-DX14* Unit with Analog Input/Output Signal.....................120
4.4.5 Connecting FCUA-DX11* Unit with Machine Control Signal...........................121
4.4.6 Connecting FCUA-DX12* Unit with Machine Control Signal...........................123
4.5 Connection of Scan I/O card ..................................................................................125
5. EMC Installation Guidelines...................................... 127
5.1 Introduction.............................................................................................................128
5.2 EMC Directives.......................................................................................................128
5.3 EMC Measures.......................................................................................................129
5.4 Panel Structure.......................................................................................................129
5.4.1 Measures for Control Panel Body ...................................................................129
5.4.2 Measures for Door ..........................................................................................130
5.4.3 Measures for Power Supply............................................................................130
5.5 Measures for Wiring in Panel .................................................................................131
5.5.1 Precautions for Wiring in Panel.......................................................................131
5.5.2 Shield Treatment of Cables.............................................................................132
5.6 EMC Countermeasure Parts ..................................................................................134
5.6.1 Shield Clamp Fitting........................................................................................134
5.6.2 Ferrite Core.....................................................................................................135
5.6.3 Surge Absorber...............................................................................................136
5.6.4 Selection of Stabilized Power Supply..............................................................138
6. Transportation Restrictions for Lithium Batteries.. 139
6.1 Restriction for Packing............................................................................................140