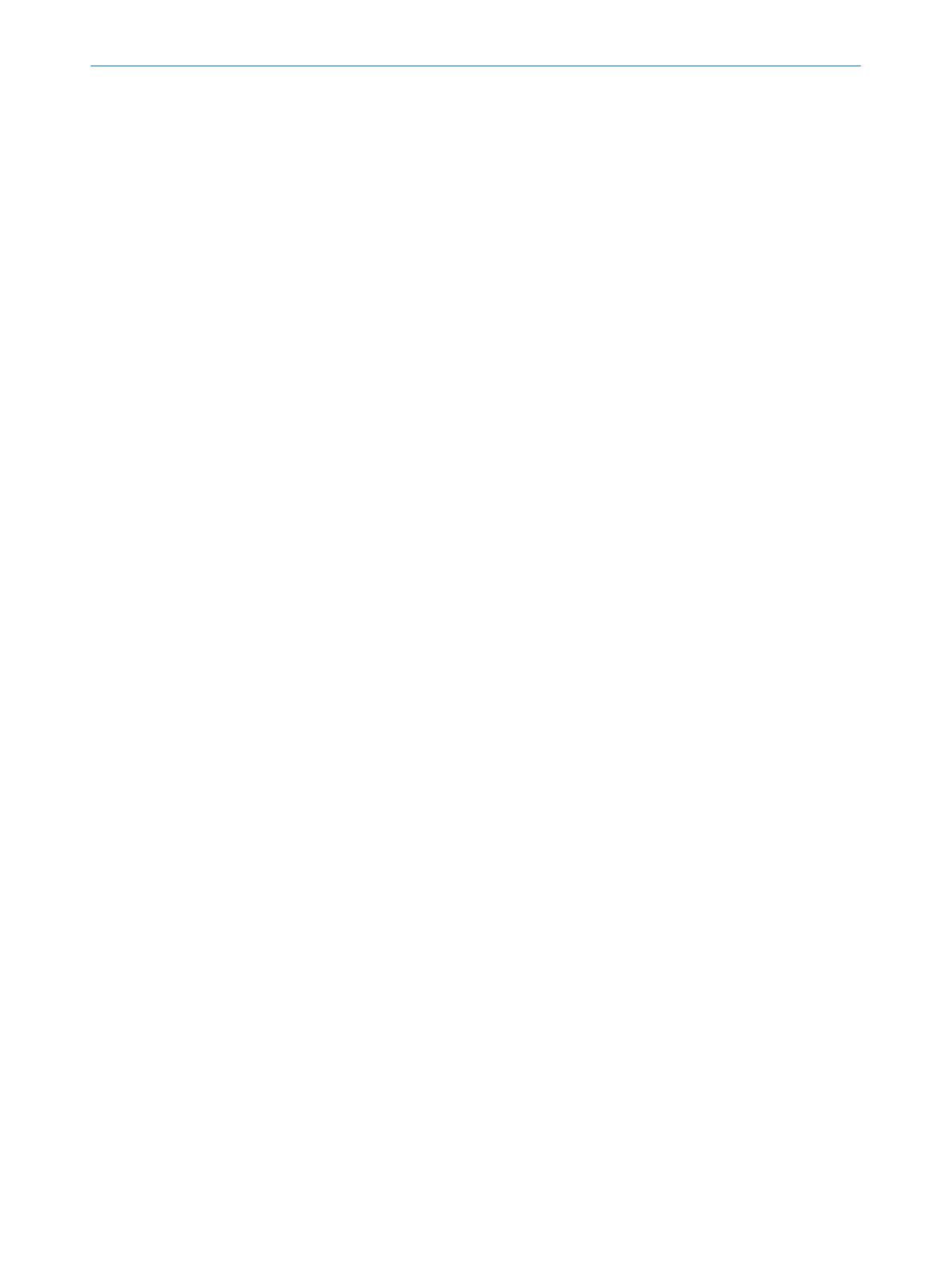
4.5.3 Notes on the tests................................................................... 34
5 Mounting............................................................................................. 37
5.1 Safety......................................................................................................... 37
5.2 Unpacking.................................................................................................. 37
5.3 Mounting the device................................................................................. 37
6 Electrical installation........................................................................ 39
6.1 Safety......................................................................................................... 39
6.2 Connecting................................................................................................ 39
6.2.1 Connecting cable with M12 plug connector, 8-pin................ 39
7 Configuration..................................................................................... 41
7.1 Overview.................................................................................................... 41
7.2 User groups............................................................................................... 42
7.3 Introduction to the Safety Designer......................................................... 43
7.3.1 User interface.......................................................................... 44
7.3.2 The device window for the safe multibeam scanner............. 44
7.4 Working with configurations..................................................................... 45
7.4.1 Reading a configuration from a device (Safety Designer)..... 46
7.4.2 Transferring a configuration from Safety Designer to a
de
vice....................................................................................... 46
7.4.3 Verifying the configuration in Safety Designer....................... 47
7.4.4 Reading and transferring the configuration using the
Safety Assistant app................................................................ 48
7.5 Overview (Safety Designer)...................................................................... 48
7.6 Configuring the safe multibeam scanner (Safety Designer).................. 49
7.6.1 Identification............................................................................ 50
7.6.2 Fields........................................................................................ 50
7.6.3 Inputs and outputs, local........................................................ 53
7.6.4 Monitoring cases..................................................................... 54
7.7 Report (Safety Designer).......................................................................... 57
7.8 Service (Safety Designer)......................................................................... 57
7.8.1 Resetting the password for the “Administrator” user group. 58
7.9 Starting and stopping the safety function (Safety Designer)................. 59
8 Commissioning.................................................................................. 60
8.1 Safety......................................................................................................... 60
8.2 Overview.................................................................................................... 60
8.3 Alignment.................................................................................................. 60
8.4 Switching on.............................................................................................. 60
8.5 Check during commissioning and modifications.................................... 61
9 Operation............................................................................................ 62
9.1 Safety......................................................................................................... 62
9.2 Regular thorough check........................................................................... 62
9.3 LEDs........................................................................................................... 62
CONTENTS
4
O P E R A T I N G I N S T R U C T I O N S | scanGrid2 I/O 8025936/2021-01-08 | SICK
Subject to change without notice