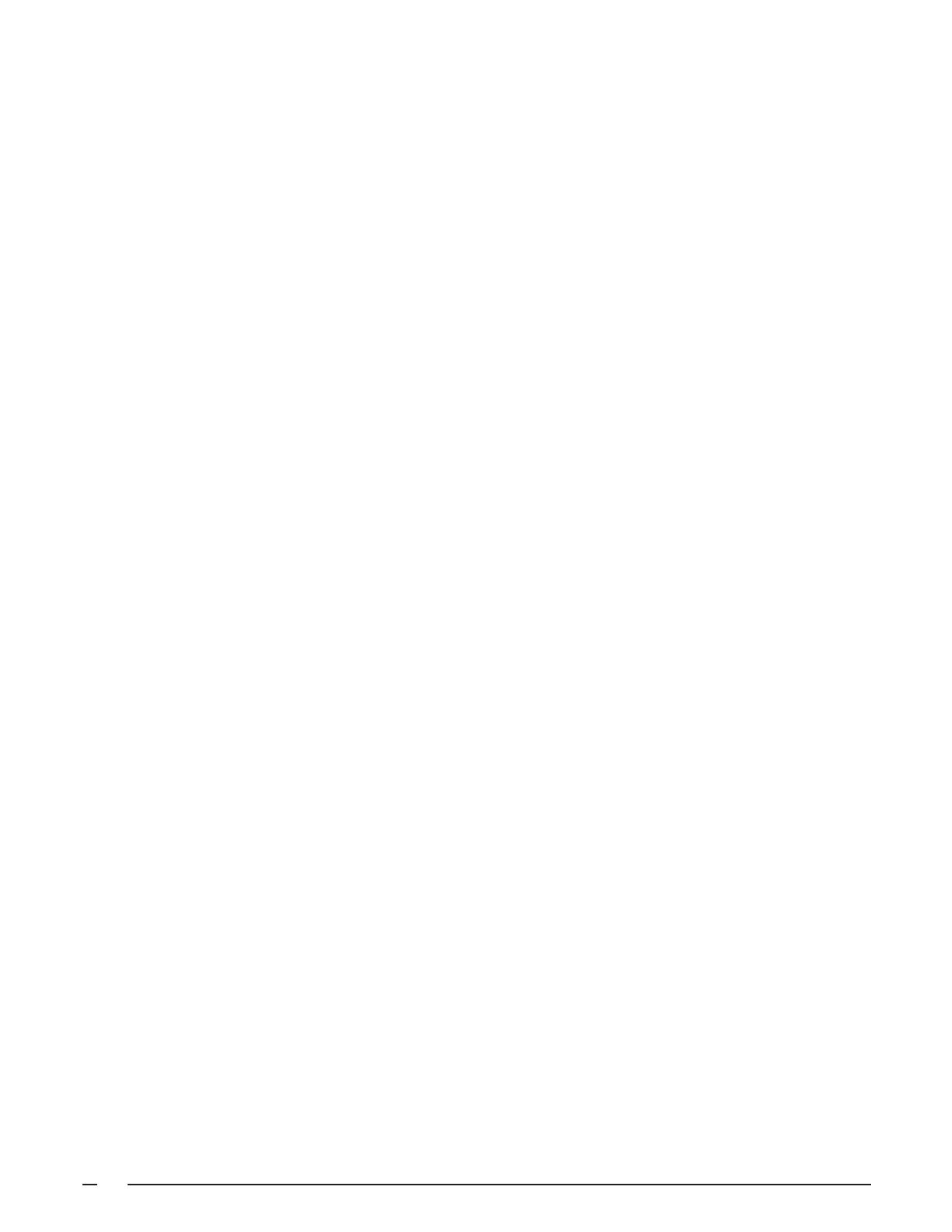
2
GENERAL SPECIFICATIONS ......................................3
SAFETY CONSIDERATIONS .......................................3
• Literature, Labels, and Tags ..................................3
• Pressures Within The System ...............................3
INSTALLATION REQUIREMENTS ...............................3
• Equipment Application ..........................................3
• Equipment Check ..................................................3
• Requirements and Codes .....................................3
• Unit Location .........................................................3
• Venting Requirements .......................................3,5
• Unit Dimensions ....................................................4
• Clearances to Combustible Materials ....................5
• Thermostat ............................................................5
• Air Filter Requirements .........................................5
• Condensate Drain .................................................6
UNIT INSTALLATION ...................................................6
• Ground Level .........................................................6
• Rigging and Hoisting .............................................6
• Rooftop ..................................................................7
AIR SUPPLY FOR COMBUSTION
AND VENTILATION .................................................7
CIRCULATING AIR SUPPLY ........................................8
• Unconditioned Spaces ..........................................8
• Acoustical Ductwork ..............................................8
• Horizontal to Down Flow Conversion ....................8
• Airfl ow Data ...........................................................9
GAS SUPPLY AND PIPING .......................................10
• Leak Check .........................................................10
GAS AND HIGH ALTITUDE CONVERSIONS ............10
• High Altitude Application .....................................10
• Natural Gas High Altitude Conversion .................10
• LP/Propane Gas Conversion ...............................10
ELECTRICAL WIRING ...............................................11
• General ...............................................................11
• Line Voltage .........................................................11
• Electrical Data Table ............................................13
LOW VOLTAGE WIRING ............................................12
• Heating Confi gurations ........................................12
VARIABLE SPEED BLOWER .....................................13
• Confi guring the Blower ........................................13
• Selecting Heat Airfl ow .........................................13
•
Selecting the Cooling Airfl ow...............................13
WIRING DIAGRAMS .......................................14,17-20
SYSTEM CHECK ......................................................15
• Pre-Start Check List ...........................................15
START-UP PROCEDURE ..........................................15
• Air Circulation .....................................................15
• System Cooling ..................................................15
• System Heating ..................................................16
• Verifying and Adjusting Firing Rate ....................16
• Verifying and Adjusting Temperature Rise ..........16
• Verifying Burner Operation .................................16
• Verifying Operation of Over-Temperature
Limit Control .......................................................19
COMPONENT FUNCTIONS .....................................19
• Flame Sensor .....................................................19
• Flame Roll-Out Control ......................................19
• Gas Valve ...........................................................19
• Pressure Switch .................................................19
• Over-Temperature Limit Control .........................19
• Comfort Alert Diagnostics ..................................19
• Led Description ..................................................19
• Compressor Wire Routing ..................................20
UNIT MAINTENANCE ...............................................20
• Thermostat Second Stage Cooling Wiring .........20
• L Terminal Wiring ................................................20
• DC SOL Connection ...........................................20
• Interpreting the Diagnostics LEDs ......................20
• Installation Verifi cation ........................................20
• Troubleshooting the Installation ..........................24
• Flash Code Tables ........................................21, 22
• Resetting Alert Codes ........................................24
• Gas Flow Rate Table ..........................................24
• Refrigerant Charging ..........................................25
• Routine Maintenance .........................................25
• Air Filter ..............................................................25
• Vent Cover Assembly .........................................25
• Condensate Drain and Outdoor Coil ..................25
• Electrical .............................................................25
• Motor Lubrication ...............................................25
• Blower Compartment .........................................25
• Heat Exchanger and Burner Maintenance .........25
• Cleaning of Heat Exchanger ..............................25
• Cleaning of Burners ...........................................26
SEQUENCE OF OPERATION ...................................26
• Heating Mode .....................................................26
• Cooling Mode .....................................................27
• Fan Mode ...........................................................27
• Unit Fails to Operate ..........................................27
INSTALLATION CHECKLIST .....................................28
TABLE OF CONTENTS