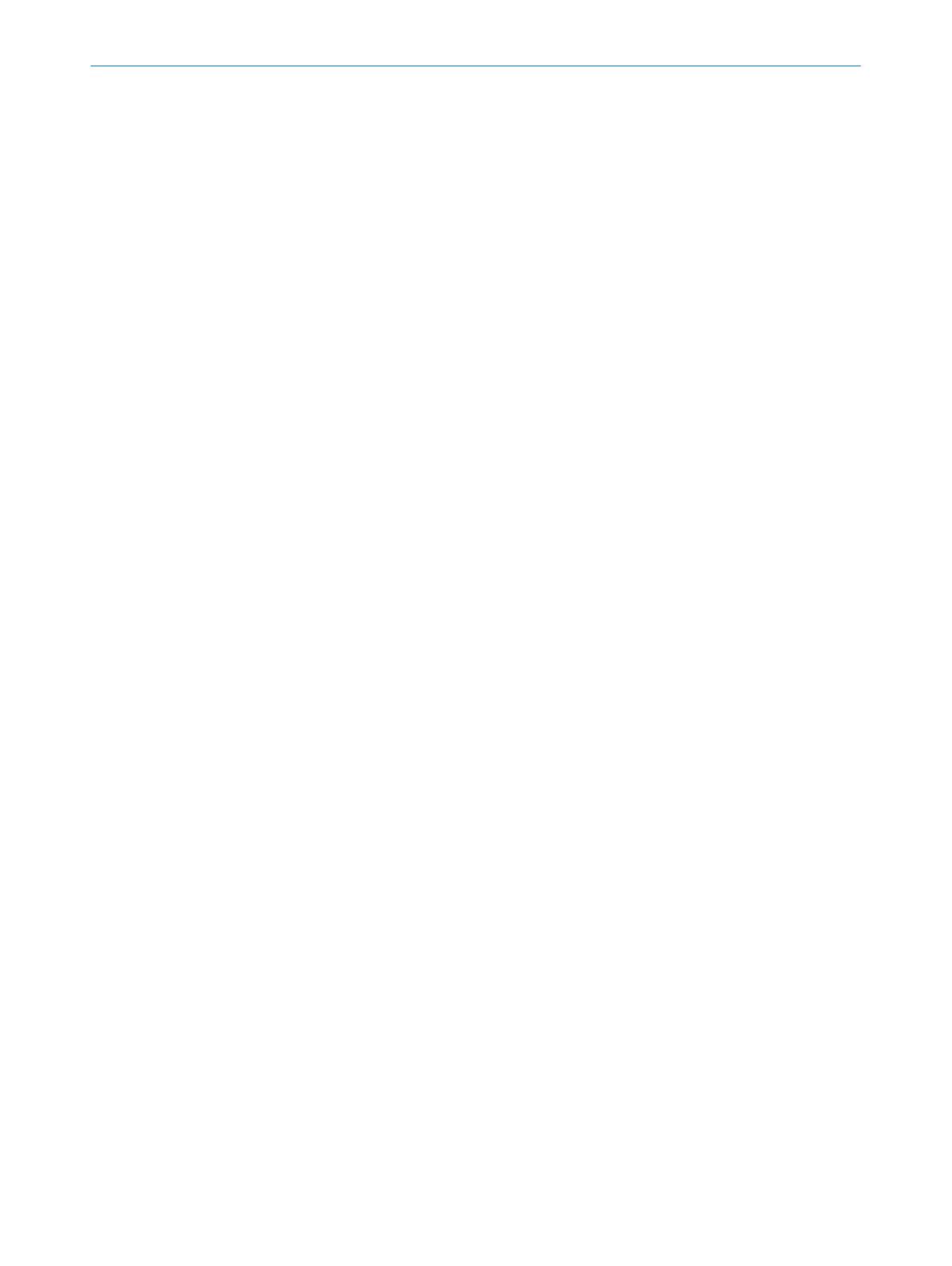
5.2 Mounting procedure................................................................................. 59
5.2.1 Direct mounting....................................................................... 60
5.2.2 Mounting using mounting kit 1a or 1b................................... 61
5.2.3 Mounting using mounting kits 2 and 3.................................. 62
5.2.4 Information label Notes on daily check.................................. 63
6 Electrical installation........................................................................ 64
6.1 Safety......................................................................................................... 64
6.2 Pin assignment......................................................................................... 65
6.2.1 Pin assignment........................................................................ 67
6.3 Unassembled system plug....................................................................... 69
6.4 Pre-assembled system plug..................................................................... 71
6.5 M8 × 4 configuration connection (serial interface)................................ 72
7 Configuration..................................................................................... 73
7.1 Delivery state............................................................................................ 73
7.2 CDS............................................................................................................ 73
7.3 Preparing the configuration..................................................................... 73
7.4 Compatibility mode................................................................................... 74
7.5 System parameters.................................................................................. 77
7.5.1 Application name..................................................................... 77
7.5.2 Name of the scanner............................................................... 77
7.5.3 User data.................................................................................. 77
7.5.4 Display direction of the 7-segment display............................ 77
7.6 Application................................................................................................ 78
7.6.1 Resolution................................................................................ 78
7.6.2 Basic response time................................................................ 79
7.6.3 Maximum protective field range............................................. 79
7.7 Incremental encoder................................................................................ 79
7.7.1 Pulses per cm travel that are output by the incremental
encoder
s.................................................................................. 80
7.7.2 Tolerances allowed on the dynamic inputs............................ 80
7.8 Inputs......................................................................................................... 81
7.8.1 Input delay................................................................................ 83
7.8.2 Sampling for the static control inputs.................................... 83
7.9 OSSDs........................................................................................................ 84
7.9.1 External device monitoring (EDM).......................................... 85
7.10 Restart....................................................................................................... 85
7.11 Universal I/O connections........................................................................ 88
7.11.1 Application diagnostic output in the compatibility mode...... 89
7.12 Field Sets................................................................................................... 89
7.12.1 Configuring the protective field and warning field................. 89
7.12.2 Importing and exporting field sets and fields........................ 90
7.12.3 Protective field or warning field suggested by the safety
laser scanner........................................................................... 91
7.12.4 Using the contour as a reference........................................... 92
CONTENTS
4
O P E R A T I N G I N S T R U C T I O N S | S300 8010948/ZA21/2020-06-18 | SICK
Subject to change without notice