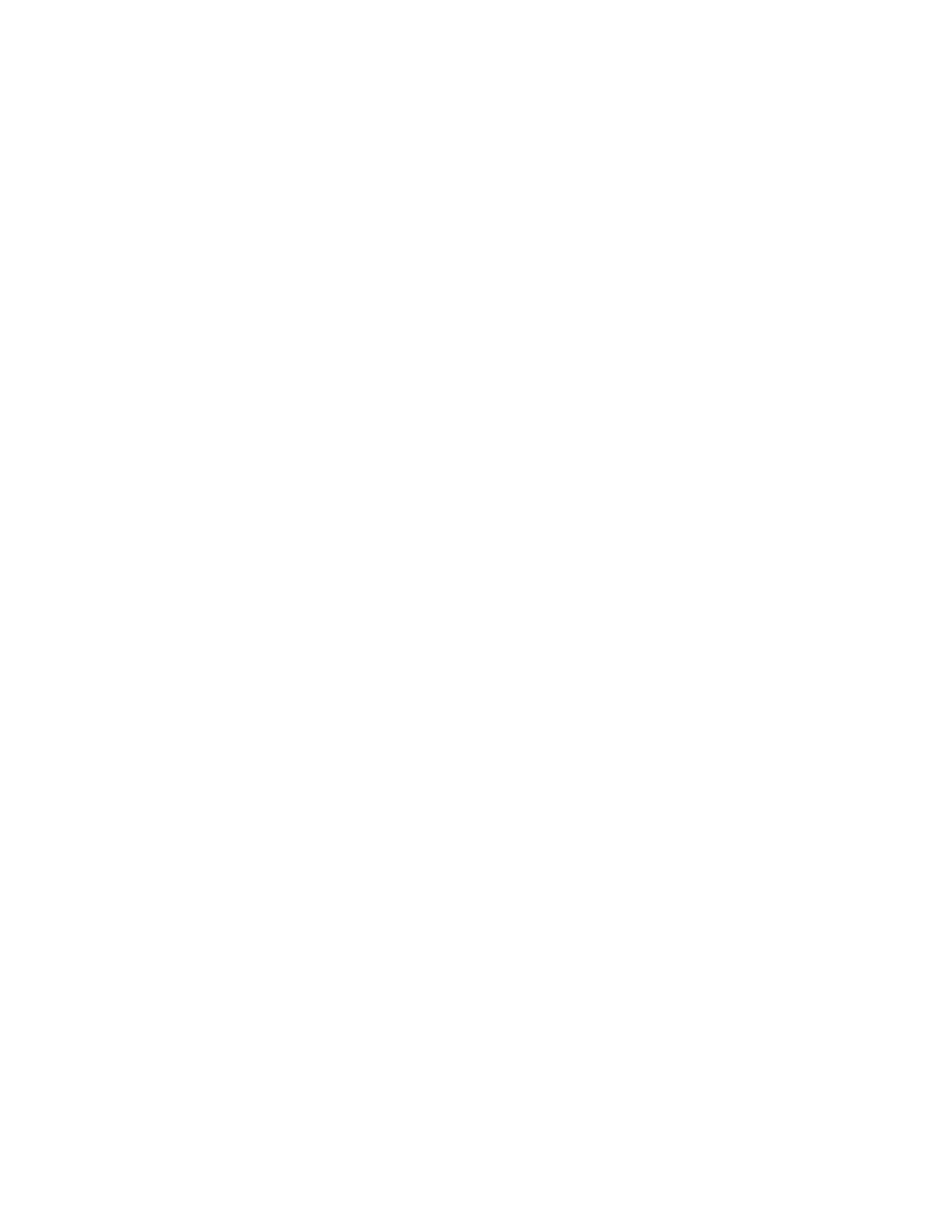
July 24, 2003 Manual No. 430429-518
TABLE OF CONTENTS
TABLE OF CONTENTSTABLE OF CONTENTS
TABLE OF CONTENTS
1.0 GENERAL DESCRIPTION............................................................................................ 1
1.1 O
VERVIEW
..........................................................................................................................................................1
1.2 C
ONTROL
O
UTPUTS
...........................................................................................................................................1
1.3 C
ONTROL
I
NPUTS
...............................................................................................................................................1
1.4 C
ONTROL
D
ISPLAY AND
S
TATUS
I
NDICATORS
.....................................................................................................2
2.0 CONTROL INSTALLATION.......................................................................................... 3
2.1 E
NCLOSURE
I
NSTALLATION
.................................................................................................................................3
2.2 S
TANDARD
E
NCLOSURE
D
IMENSIONS
.................................................................................................................3
2.3 R
EMOTE
C
ONTROL
R
ECEPTACLE
.......................................................................................................................4
3.0 WELD SEQUENCE EVENTS........................................................................................ 5
3.1 W
ELD
S
EQUENCE
P
ARAMETERS
........................................................................................................................5
3.2 P
ULSE
W
ELD
M
ODE
P
ARAMETERS
....................................................................................................................5
3.3 W
ELD
C
YCLE
E
VENTS
.......................................................................................................................................5
3.4 S
POT
W
ELD
M
ODE
............................................................................................................................................6
3.5 A
RC
A
CTIVE
T
EST
..............................................................................................................................................6
4.0 USER INTERFACE........................................................................................................ 7
4.1 R
EMOTE
C
ONTROL
I
NTERFACE
S
PECIFICATION
...................................................................................................7
4.2 R
EMOTE
P
ENDANT
I
NTERFACE
...........................................................................................................................7
4.3 O
PTIONAL
O
PERATOR
P
ENDANT
.........................................................................................................................7
4.4 RS-232 S
ERIAL
P
ORT
........................................................................................................................................7
4.5 A
UTOMATED
U
SER
I
NTERFACE
...........................................................................................................................7
4.6 T
YPICAL
U
SER
I
NTERFACE FOR
A
UTOMATED
O
PERATION
...................................................................................9
5.0 CONTROL SPECIFICATION....................................................................................... 10
5.1 E
NCLOSURE
S
PECIFICATION
............................................................................................................................ 10
5.2 C
ONTROL
C
ABLES AND
C
ONNECTORS
............................................................................................................. 10
5.3 C
ONTROLS AND
S
TATUS
I
NDICATORS
.............................................................................................................. 10
5.4 S
YSTEM
S
PECIFICATIONS
................................................................................................................................11
6.0 OPERATIONAL DISPLAY AND PROGRAMMING ................................................... 12
6.1 S
TATIC
W
ELD
D
ISPLAY
S
CREENS
.................................................................................................................... 12
6.2 S
TATIC
D
ISPLAY
S
CREEN
E
RROR
M
ESSAGES
.................................................................................................. 13
6.3 M
ODIFYING
W
ELD
S
CHEDULE AND
S
YSTEM
P
ARAMETERS
............................................................................... 13
6.4 W
ELD
S
CHEDULE
P
ARAMETER
M
ENUS
............................................................................................................ 14
6.5 PAW W
ELD
S
CHEDULE
M
ENU
S
CREENS
........................................................................................................ 14
6.6 PAW W
ITH
C
OLD
W
IRE
F
EED
O
PTION
W
ELD
S
CHEDULE
M
ENU
S
CREENS
...................................................... 15
6.7 GMAW O
PTION
W
ELD
S
CHEDULE
M
ENU
S
CREENS
........................................................................................ 16
6.8 S
ETUP
P
ARAMETER
M
ENUS
............................................................................................................................. 17
6.9 S
ETUP
P
ARAMETER
M
ENU
S
CREENS
............................................................................................................... 17
7.0 WC 1 OFF-LINE RS-232 TERMINAL PROTOCOL....................................................18
7.1 G
ENERAL
D
ESCRIPTION
...................................................................................................................................18
7.2 T
ERMINAL
P
ROTOCOL
......................................................................................................................................18
7.3 T
ERMINAL
C
OMMANDS
.....................................................................................................................................19
8.0 ENCLOSURE LAYOUTS............................................................................................. 22
8.1 WC 1 C
ONTROL
E
NCLOSURE
- S
TANDARD
L
AYOUT
P/N: C3A5003............................................................... 22