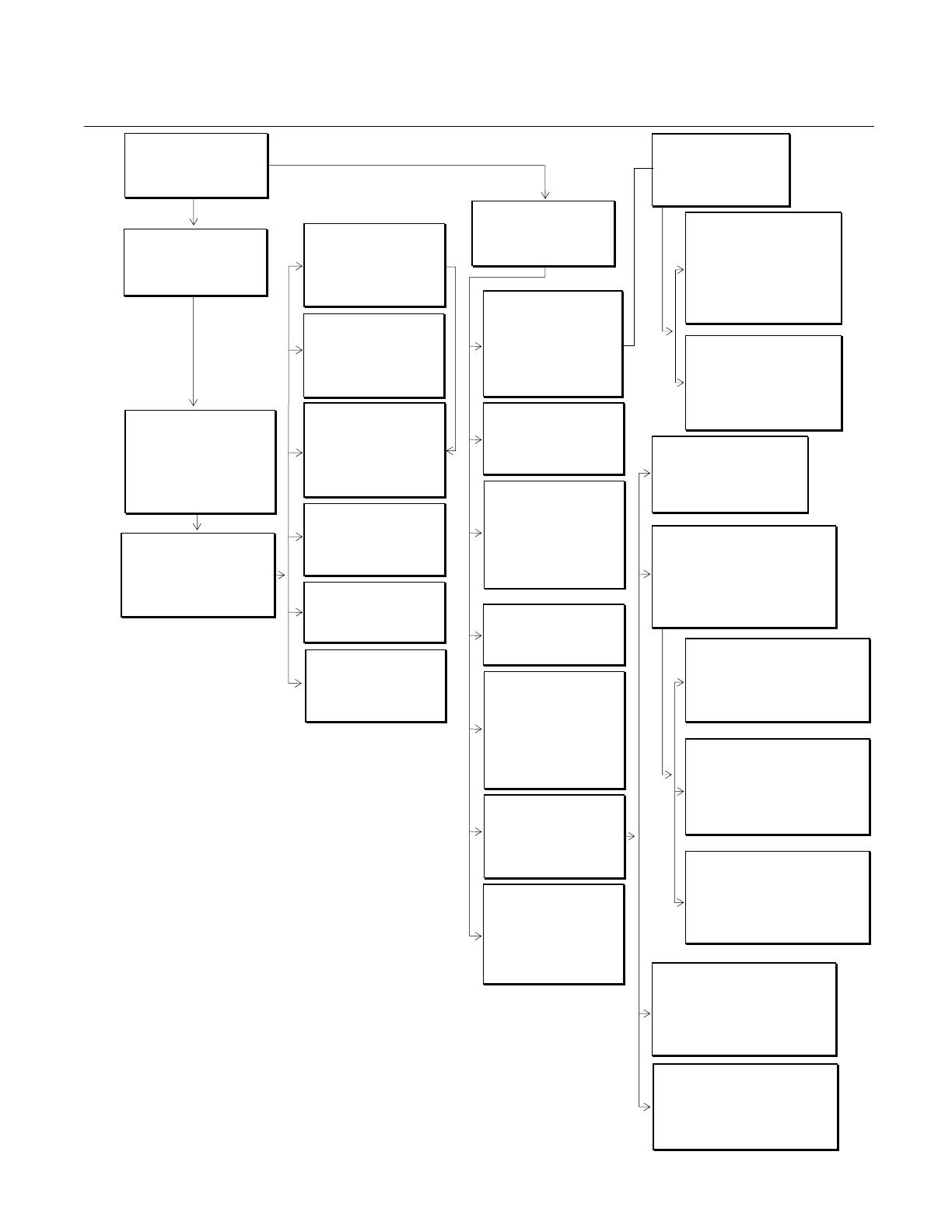
Instruction Manual
748275-F
September 2003
2-2 Analog Output/3 Alarms Rosemount Analytical Inc. A Division of Emerson Process Management
Model NGA2000 I/O Modules
Figure 2-1. Software Displays Relative to Analog Output
with 3 Alarms I/O Module
Expert controls and setup
Expert analyzer controls...
Auxiliary module controls...
System set up...
Analyzer Module set up...
Auxiliary Module set up...
Auxiliary module set up
Select an auxiliary module for set up
Module Tag
Module Tag
Module Tag
Module Tag
Module Tag
Module Tag
Module Tag
Module Tag
Analog module set up
Analog output parameters...
Automatic range change parameters...
List range limits...
Alarm conditions...
General concentration alarm parameters...
Specific concentration alarm parameters...
Slot position 1
Main Menu
Basic Controls...
Expert controls and setup...
(Operational Configuration)
Technical level configuration...
(Diagnostic and manufacturing/service)
General concentration alarm
parameters
Trips as % of range or absolute: % range
Hysteresis: 10%
Delay till alarm activates: 10 Secs
Specific concentration alarm
parameters
Relay 1 (2, 3)
Alarm trip point - absolute ppm: 0 ppm
Alarm trip point - % range: 0%
Alarm type: High
Alarm operation: High
Analog output parameters
Parameter reported: CO
Voltage or current: 0-5 V
Output value on analyzer failure: 0
Output hold on validity: Yes
Output hold on maintenance: Yes
Output hold on calibration: Yes
List range limits...
Automatic range change pa-
rameters
Range change control: Local
If auto, change down at -% 80%
If auto, change up at -% 90%
(Percentage of LOWER range)
Time delay on auto change-secs: 0 Secs
Toggle hold off - secs: 30 Secs
Range List
Range 1 lower limit: 0 ppm
Range 1 upper limit: 10 ppm
Range 2 lower limit: 0 ppm
Range 2 upper limit: 100 ppm
Range 3 lower limit: 0 ppm
Range 3 upper limit: 250 ppm
Range 4 lower limit: 0 ppm
Range 4 upper limit: 1000 ppm
Alarm Conditions
Relay 1 trips on: Validity
Relay 2 trips on: Control
Relay 3 trips on: Failure
(If used as an automotive remote control
module, relay 3 must be set to "CON-
TROL")
Technical configuration menu
System set up...
Service menus...
Diagnostic menus...
Other module diagnostic menus...
Listing of all modules...
System Set Up
Main display configuration...
Front panel control...
Date and time...
Miscellaneous control set up...
Module binding...
Interference binding...
System reset...
Record security codes...
System tag: Rosemount
Service Menus
Manufacturing data...
Service history...
Review stored data...
In maintenance since: N/A
Maintenance alert messages...
Record security codes...
Manufacturing data
Control module data...
Analyzer module data...
Module Tag
Module Tag
Module Tag
Module Tag
Module Tag
Module Tag
Module Tag
Module Tag
Diagnostic menus
Control module diagnostics...
Analyzer module diagnostics...
Module Tag
Module Tag
Module Tag
Module Tag
Module Tag
Module Tag
Module Tag
Module Tag
Analog output module
Power supplies...
Analog output...
Relay status...
Digital input lines...
Slot position: 1
Current range: 1
IO module ID Auto 1043
IO Unit manufacturing data
Hardware revision number: 1
Software revision number: 1.1
IO module ID: Auto 1043
Common range
indication and control: OFF
Other module diagnostics
This screen reserved for other modules if
present:
Module Tag
Module Tag
Module Tag
Module Tag
Module Tag
Module Tag
Module Tag
Module Binding
Analyzer module selected: CLA 1023
Select modules...
Proposed bind:
View bindings...
Bind selections!
Unbind everything!
Modules Bound
Analyzer module selected: CLA 1023
Auxiliary module: Auto 1023
Auxiliary module: Acal 2322
Auxiliary module: HART 1092
Auxiliary module: None
Auxiliary module None
Auxiliary module: None
Proposed new bind:
Select IO modules
Select the modules you wish to bind to the
current analyzer.
Module Tag
Module Tag
Module Tag
Module Tag
Module Tag
Module Tag
Module Tag
Module Tag
Analog module power supplies
+15V analog is: 14.98 V
+15V analog was: 14.87 V
-15V analog is: -14.92 V
-15V analog was: -14.98 V
+5V digital is: 4.98 V
+5V digital was: 5.02 V
IO Module Analog Output Diagnostics
Theoretical output voltage -V: 0.784 V
Theoretical output current-mA: 1.567mA
Measured output voltage -V: 0.762 V
Voltage on current terminals -V: 0.162 V
Output load -ohms: 200 ohms
Calculated output current -mA: 13 mA
Diagnostics limits...
Voltage output calibration...
Current output calibration...
Analog Output Diagnostic Limits
Maximum current load: 600 ohms
Minimum current load: 10 ohms
0 mA under-current limit -mA: -1 mA
4 mA under-current limit -mA: 3.9 mA
20 mA over-current limit -mA: 20.8 mA
0V under-voltage limit -V: -0.5 V
5V under-voltage limit -V: 5.5 V
Voltage output calibration
Voltage/current mode: 0-5 V
Desired output voltage: 0 V
Measured output voltage: 0.762 V
Zero offset: 0 V
Gain factor: 0
Set to test for calibration: Test
Set desired output voltage: Adjust the measured voltage
with the zero and gain factors. Then set to auto.
Current output calibration
Voltage/current mode: 0-5 V
Desired output current: 0 V
Measured output current: 13 mA
Zero offset: 0 V
Gain factor: 0
Set to test for calibration: Test
Set desired output current: Adjust the measured voltage
with the zero and gain factors. Then set to auto.
Relay status
Relay function: Test
(Set this to TEST to set relays below)
Relay 1 status: On
Relay 1 measures: On
Relay 2 status: On
Relay 2 measures: On
Relay 3 status: On
Relay 3 measures: On
Input line status
Line 1 status: OFF
Line 2 status: OFF
Line 3 status: OFF
Line 4 status: OFF
Line 5 status: OFF
Line 6 status: OFF
Common range indication/control: OFF