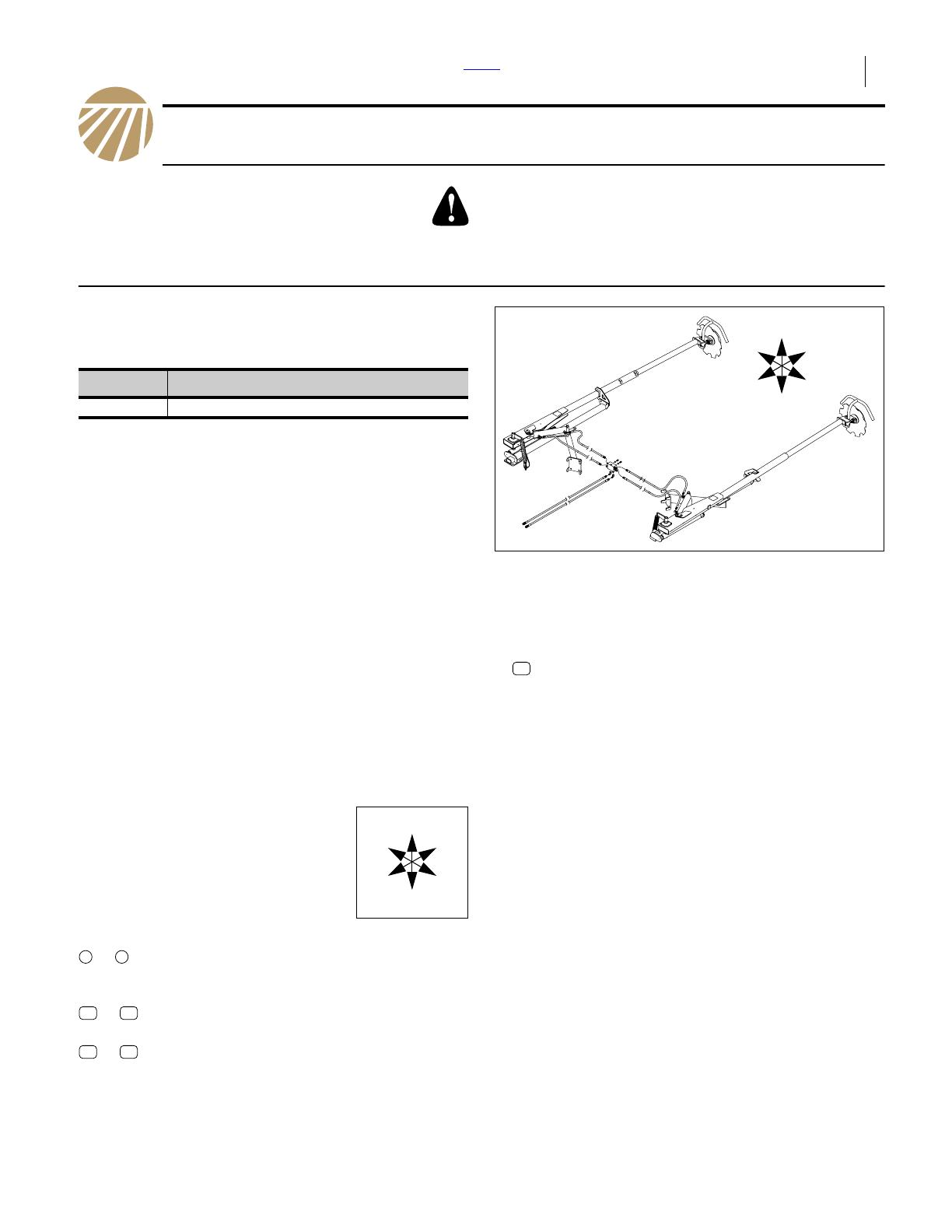
Great Plains Mfg., Inc. Parts Installation Instructions 1
2013-10-10 ©Copyright 2010 113-850M
2013- Single Fold Marker
6 Meter / 20 Foot HD Air Drill Implements
General Information
These instructions explain how to install field markers on
a compatible air drill implement.
These instructions apply to an installation of a 2013- kit:
Note: Kits manufactured in 2014 or later are described in
manual 113-921M. Compare Part List illustrations
if uncertain which manual applies to your kit.
One kit includes two markers (left and right), an auto-
matic sequence valve, all hydraulic hoses and fittings,
and all necessary mounting hardware.
One kit updates one air drill.
Related Documents
Have the Operator Manual at hand for drill movements.
Have the current Parts Manual at hand for parts ID.
Notations and Conventions
“Left” and “Right” are facing in the
direction of machine travel. An orienta-
tion rose in the line art illustrations
shows the directions of Left, Right,
Front, Back, Up, Down.
Call-Outs
Null4:
Parts and Tools Required
• Locate two existing QD fittings supplied with the air
cart (see Figure 22 on page 21):
811-070C CP 3/4FORB QD
These fittings were bundled with the marker QD ports
on the rear of the air cart, but are typically removed
prior to delivery (they present an open line risk should
anyone activate the marker circuit prior to marker
installation).
• You need a suitable tractor for positioning the air drill,
and having sufficient hydraulic circuits, with adequate
capacity to operate the markers (installing markers
increases the required circuits to 3).
• You need a hoist with 136 kg (300 pound) capacity.
• Have safety goggles and gloves for inspecting hydrau-
lic connections.
• Other than the hoist, only basic hand tools are
required.
• A few cable ties are required to secure hoses.
If orange colored ties are available, 6 can also be used
to identify hoses.
• 5 liters (1.2 gallons) of hydraulic fluid is needed to
charge the marker system.
Null4:
Used with: When you see this symbol, the subsequent instructions and
warnings are serious - follow without exception.
Your life and the lives of others depend on it!
• NTA607, NTA607HD
• NTA2007, NTA2007HD
Kit Kit Description
113-849A NTA607HD-NTA2007HD MARKER BDL
Null4:
Figure 1
Marker Kit
31327
U
D
F
B
L
R
166-283M NTA607HD/2007HD Operator Manual
166-372M NTA607/2007 Operator Manual
166-372M-ENG NTA607 Operator Manual (EU)
166-283P NTA607HD/2007HD Parts Manual
166-372P NTA607/2007 Parts Manual
to
Single-digit callouts identify components in
the currently referenced Figure or Figures.
These numbers may be reused for different
items from page to page.
to Two-digit callouts in the range 11 to 12 refer-
ence affected existing parts (see page 18).
to Two-digit callouts in the range 21 to 80 refer-
ence new parts (see list on page 18).
U
D
F
B
L
R
1 9
11 12
21 80
12