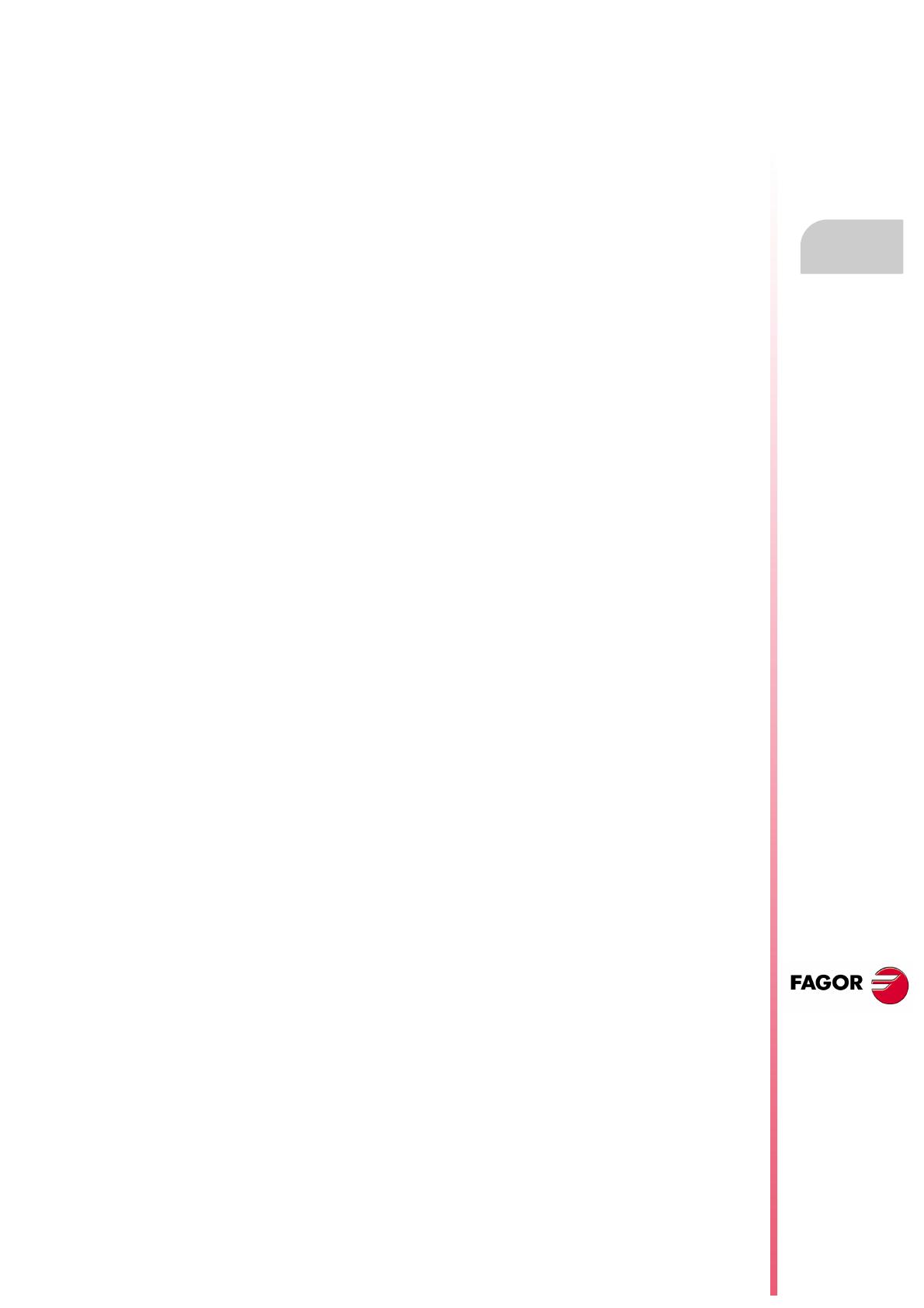
Drive. CT series
I
CT
Ref.1509
· 3 ·
GENERAL INDEX
1 DESCRIPTION ......................................................................... 5
System configuration. General diagrams....................................................................................... 6
Stages of the system configuration................................................................................................ 9
Supplied accessories ................................................................................................................... 10
2 DRIVE MODULES .................................................................. 11
Presentation................................................................................................................................. 11
Outside appearance..................................................................................................................... 12
Technical data.............................................................................................................................. 13
Connector layout.......................................................................................................................... 23
3 OTHER MODULES ................................................................. 25
SM-Keypad .................................................................................................................................. 25
SM-SERCOS ............................................................................................................................... 25
EMC external mains filters........................................................................................................... 26
Braking resistors .......................................................................................................................... 27
4 MECHANICS ......................................................................... 29
Safety data................................................................................................................................... 29
Planning the installation............................................................................................................... 29
Removing the terminal caps ........................................................................................................ 31
Installation and removal of a resolution module........................................................................... 34
Installation and removal of a keyboard ........................................................................................ 35
Mounting methods ....................................................................................................................... 36
Coupling of the SPMD1403 and SPMC1402 ............................................................................... 39
5 CABLES ................................................................................. 43
AC supply cable to external EMC filter ........................................................................................ 43
AC supply cable - or external EMC filter - to drive ..................................................................... 43
Motor-drive power cable ............................................................................................................ 44
Motor feedback cables................................................................................................................. 45
Direct feedback cables................................................................................................................. 47
Communication cable. SERCOS optical fiber.............................................................................. 49
PC-DRIVE serial communication cable ....................................................................................... 50
6 CONNECTIONS ..................................................................... 51
Mains connection......................................................................................................................... 51
AC supply requirements............................................................................................................... 51
Rated values................................................................................................................................ 52
Ground connections..................................................................................................................... 53
Connection of protection fuses .................................................................................................... 54
Connection of external EMC filters ..............................................................................................55
Connection of the line induction................................................................................................... 57
Connection of the external braking resistors................................................................................ 58
Connection of the heatsink fan supply ......................................................................................... 60
Connection of 24 V DC control supply ......................................................................................... 61
Connection of low voltage DC power supply ............................................................................... 61
Connection of control and communication signals....................................................................... 62
7 CONNECTION DIAGRAMS .................................................... 79
SP6402 drive with FM9-A100-C5Cx-E01 asynchronous motor................................................... 79
SP6402 drive with FM9-B113-C5Cx-E01 asynchronous motor................................................... 80
SPMD1403-1S drive with FM9-A130-C5Cx-E01 asynchronous motor........................................ 82
8 DIMENSIONS ........................................................................ 83
Drives........................................................................................................................................... 83