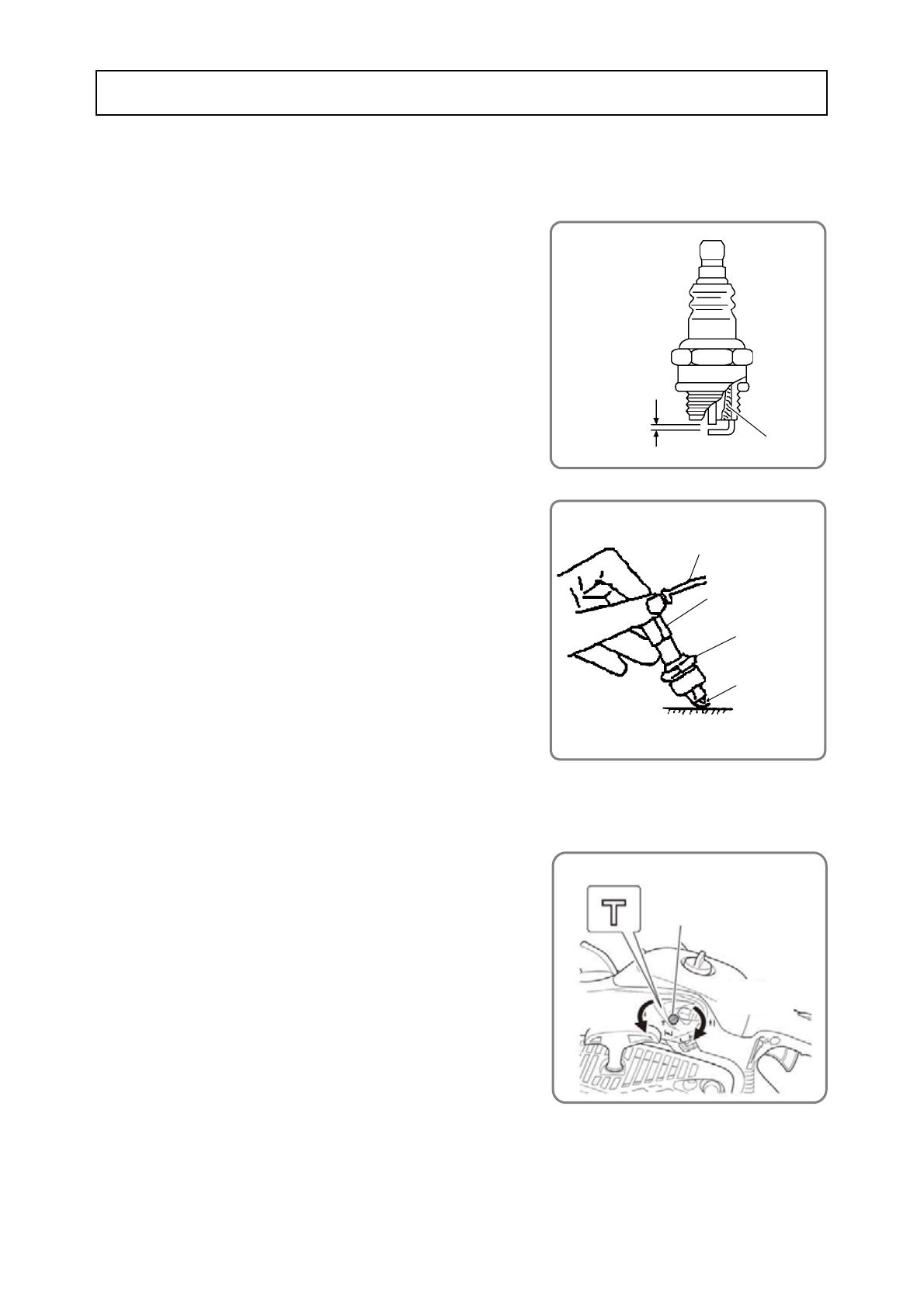
-7-
• Spark plug
• Checking for sparks
High voltage cord
Ignited sparks
Spark Plug Ass’y
BPMR7A [73]
Plug cap
Metallic portion of the engine
[Bold] numbers in the description below correspond to item numbers in the Parts List and exploded
assembly diagram for the Model CS 33EDP.
WARNING: Always stop the engine prior to disassembly or when replacing the saw chain.
1. Checking for sparks of the spark plug
CAUTION:
• Be careful not to touch the metallic portion of Spark
Plug Ass’y BPMR7A [73] when pulling the starter
handle; otherwise, you run the risk of electric shock.
Wear gloves to prevent electric shock.
• Carefully wipe off any fuel around the plug to avoid a
sudden flash of fire.
(1) Remove Spark Plug Ass’y BPMR7A [73] from the Cylinder
[74]. Use a wire brush to clean off carbon deposits on the
electrodes of Spark Plug Ass’y BPMR7A [73], as needed.
Adjust the gap between the electrodes if necessary. Use a
cloth to wipe off any fuel on the electrodes. Remove fuel left
in the Crank Case [96] by following the procedure below.
(a) Remove the Spark Plug Ass’y BPMR7A [73] from the
Cylinder [74].
(b) Open the Choke Lever [153], and then set the Stop
Switch [147] to the stop position.
(c) Open the throttle (by pulling the Throttle Lever [156]).
(d) Pull the starter handle several times.
(2) Insert Spark Plug Ass’y BPMR7A [73] into the Spark Plug
Cap [77], and then place the electrodes in contact with
the metallic portion of the engine. Under these conditions,
set the Stop Switch [147] to the startup position and pull
the starter handle.
(3) When all the above steps are completed normally, the electrodes of Spark Plug Ass’y BPMR7A [73]
should make a snapping sound to generate sparks.
2. Adjustment of the carburetor
(1) Use the Idle Adjust Screw [12] to adjust the carburetor.
• Use this screw to adjust revolutions at idling. Turning the
screw clockwise increases engine revolutions; turning it
counterclockwise decreases engine revolutions.
(2) Standard setting of the carburetor
• 2,800 to 3,200 min
-1
(Confirm that the saw chain does not rotate.)
(3) Fine adjustment
• Idling adjustment
(a) Adjust the idling revolutions after the engine is fully
warmed up.
(Tip on warm-up: Let the engine idle for one minute with the engine in half-throttled status.)
(b) Use the Idle Adjust Screw [12] to set revolutions so that the Saw Chain [132] does not start
rotating while the engine runs stably.
(c) Set idling revolutions to 2,800 to 3,200 min
-1
by using the Idle Adjust Screw [12].
(Adjust to approx. 3,000 min
-1
.)
Inspection and repair procedures
Gap between
electrodes
(0.6 to 0.7 mm)
Remove carbon here.
• Idle adjust screw
Idle Adjust Screw [12]
Revolutions
decrease.
Revolutions
increase.