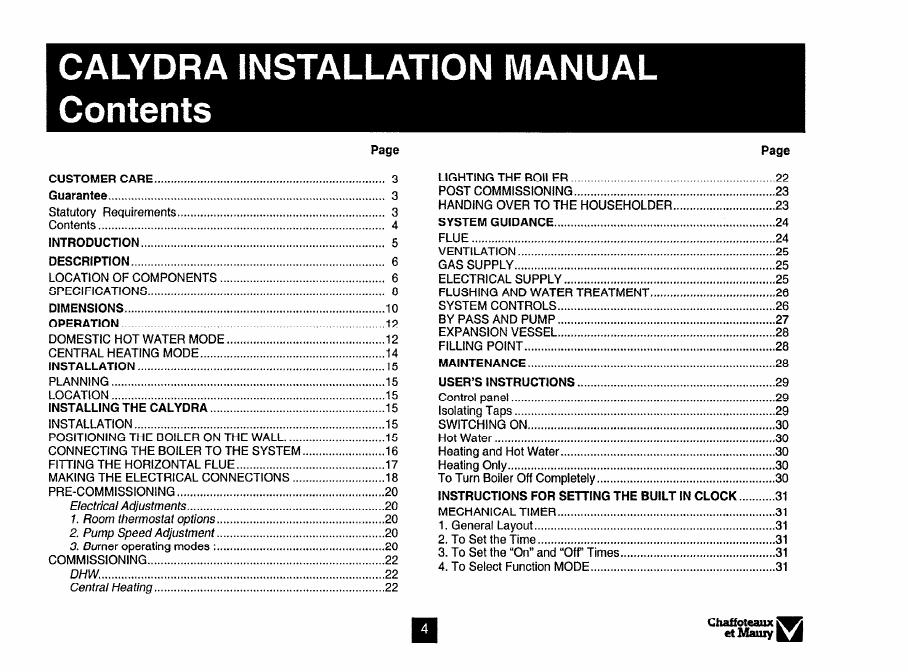
Page
CUSTOMER CARE.. .................................................................... 3
Guarantee.. .................................................................................. 3
Statutory Requirements.. ............................................................. 3
Contents.. ..................................................................................... 4
INTRODUCTION.. ........................................................................ 5
DESCRIPTION.. ........................................................................... 6
LOCATION OF COMPONENTS .................................................. 6
SPECIFICATIONS.. ...................................................................... 8
DIMENSIONS.. ............................................................................. 10
OPERATION ............................................................................... .12
DOMESTIC HOT WATER MODE ............................................... .12
CENTRAL HEATING MODE.. ..................................................... .I4
INSTALLATION .......................................................................... .15
PLANNING .................................................................................. .15
LOCATION ................................................................................. ..15
INSTALLING THE CALYDRA .................................................... .15
INSTALLATION ........................................................................... .15
POSITIONING THE BOILER ON THE WALL.. ............................ 15
CONNECTING THE BOILER TO THE SYSTEM.. ...................... .18
FITTING THE HORIZONTAL FLUE.. .......................................... .17
MAKING THE ELECTRICAL CONNECTIONS ........................... .18
PRE-COMMISSIONING.. ............................................................ .20
Electrical Adjustments ........................................................... .20
1. Room thermostat options.. ................................................ .20
2. Pump Speed Adjustment.. ................................................ .20
3. Burner operating modes :. ................................................. .20
COMMISSIONING.. ..................................................................... .22
DHW.. .................................................................................... .22
Central Heating ..................................................................... .22
Page
LIGHTING THE BOILER ............................................................. .22
POST COMMISSIONING.. ........................................................... 23
HANDING OVER TO THE HOUSEHOLDER.. ............................ .23
SYSTEM GUIDANCE.. ................................................................ .24
FLUE ........................................................................................... .24
VENTILATION.. ........................................................................... .25
GAS SUPPLY.. ............................................................................ .25
ELECTRICAL SUPPLY.. ............................................................. .25
FLUSHING AND WATER TREATMENT ...................................... 26
SYSTEM CONTROLS . . . . . . . . . . . . . . . . . . . . . . . . . . . . . . . . . . . . . . . . . . . . . . . . . . . . . . . . . . . . . . . . . . 26
BY PASS AND PUMP ................................................................. .27
EXPANSION VESSEL.. ............................................................... .28
FILLING POINT.. ......................................................................... .28
MAINTENANCE.. ......................................................................... 28
USER’S INSTRUCTIONS ........................................................... .29
Control panel ............................................................................... .29
Isolating Taps .............................................................................. .29
SWITCHING ON.. ........................................................................ .30
Hot Water .................................................................................... .30
Heating and Hot Water.. .............................................................. .30
Heating Only.. .............................................................................. .30
To Turn Boiler Off Completely.. ................................................... .30
INSTRUCTIONS FOR SETTING THE BUILT IN CLOCK.. ........ .31
MECHANICAL TIMER.. ............................................................... .31
1. General Layout.. ...................................................................... .31
2. To Set the Time.. ..................................................................... .31
3. To Set the “On” and “Oft” Times.. ............................................ .31
4. To Select Function MODE . . . . . . . . . . . . . . . . . . . . . . . . . . . . . . . . . . . . . . . . . . . . . . . . . . . . . . . . 31