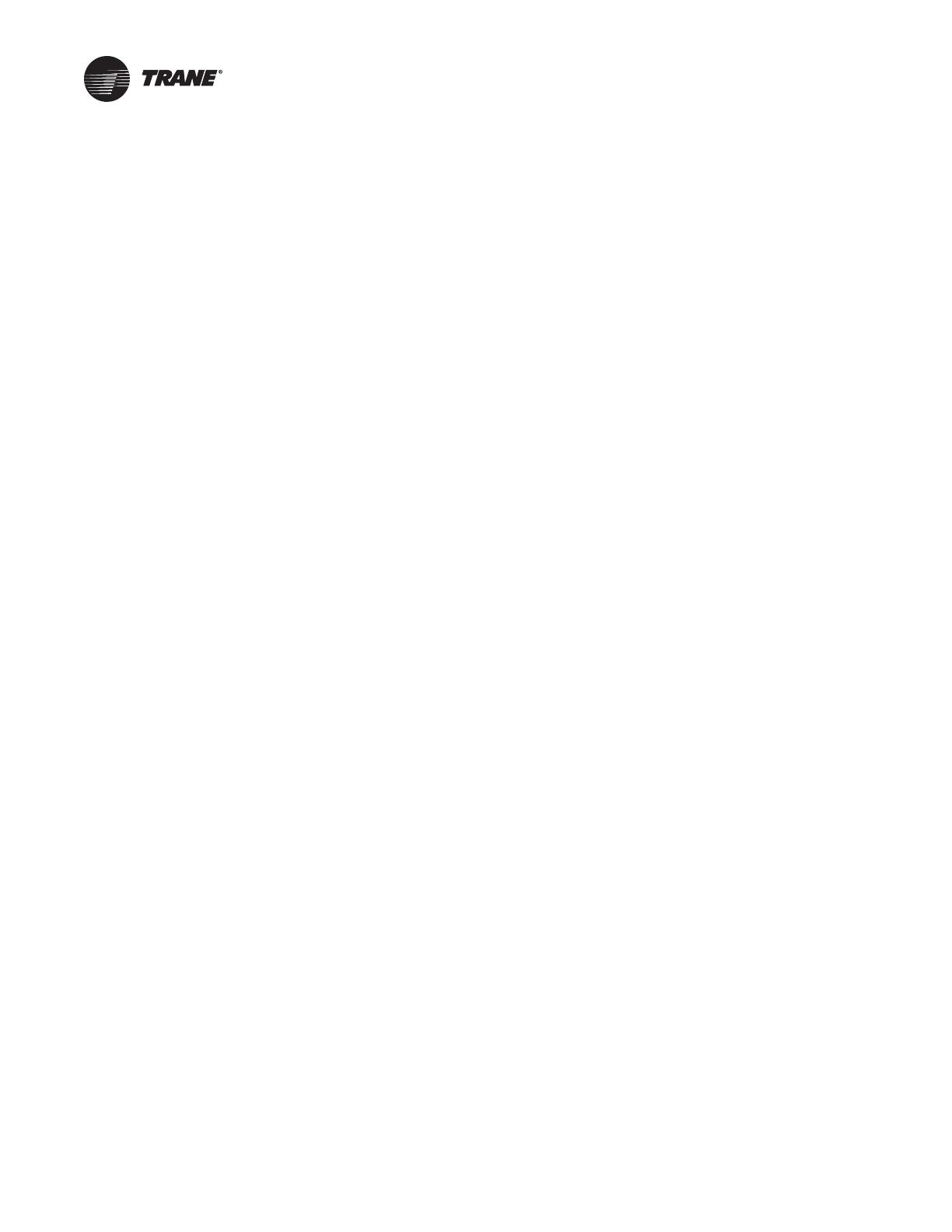
6 VAV-SVP01A-EN
General Information
Chapter Overview
This chapter contains information about the following:
• Unit Control Module VAV VV550 Controller
• Specifications
• VAV VV550 Controller Enhancements
• VAV VV550 Controller Features
• Shipping & Storage
• Data Lists
Unit Control Module VAV VV550 Controller
The VV550 is a microprocessor-based, Direct Digital Controller (DDC) for the (Variable Air Volume)
VAV terminal unit. Units have been made with either pneumatic, analog electronic, or
microprocessor controls (DDC VAV). This manual discusses only terminal units with Comm 5 VAV
VV550 DDC Controller. Factory installed DDC/VAV controls are available with all single duct
terminal units, dual duct units, as well as parallel fan-powered and series fan-powered units. Two
VAV VV550 Controllers are required for dual duct units (one for the heating duct and one for the
cooling duct) and another application requiring to controllers is Flow tracking (one unit controller
is programmed from the factory with the Space temperature program and the other is downloaded
with the Flow tracking program.
The VAV VV550 Controller can be configured from the factory with three different application
programs. The VAV VV550 Controller programmed for space temperature control modulates a
VAV's damper blade based on a zone temperature, measured airflow, and set points to
continuously control conditioned air delivery to the space. The volume of incoming air is
monitored and the damper adjusts to provide accurate control independent of the duct pressure.
The damper modulates between operator set points depending on space conditions. Additionally,
fan and heat outputs may be energized depending on the application.
The VAV VV550 Controller programmed for ventilation flow control is applied to a VAV terminal and
used to temper cold outdoor air (OA) that is brought into a building for ventilation purposes. The
tempered air is intended to supply an air-handling unit (AHU), which provides comfort control to
the zones it is serving. The VAV terminal supplies the correct amount of ventilation air and, when
reheat is added, tempers the ventilation air to reduce the load on the air handler by sensing the
discharge air temperature of VAV unit.
The VAV VV550 Controller programmed for Flow Tracking Control (FTC) has two VAV VV550
Controllers working together to provide flow tracking control. One VAV VV550 controller is
programmed from the factory with the Space temperature program and the other is downloaded
with the Flow tracking program. The space temperature controller airflow output is bound to the
flow tracking controller airflow setpoint input. The flow tracking controller adds the configured
airflow tracking offset (positive or negative) to the airflow setpoint (communicated airflow setpoint)
and controls the airflow to this setpoint.
The VAV VV550 Controller utilizes an FTT-10A Free Topology transceiver, which supports non-
polarity sensitive, free topology wiring, which allows the system installer to utilize star, bus, and
loop architectures. Available inputs include a twisted/shielded communication link, zone sensor,
auxiliary temperature sensor (optional), and Occupy/Unoccupied Sensor (optional), and 24VAC
power.