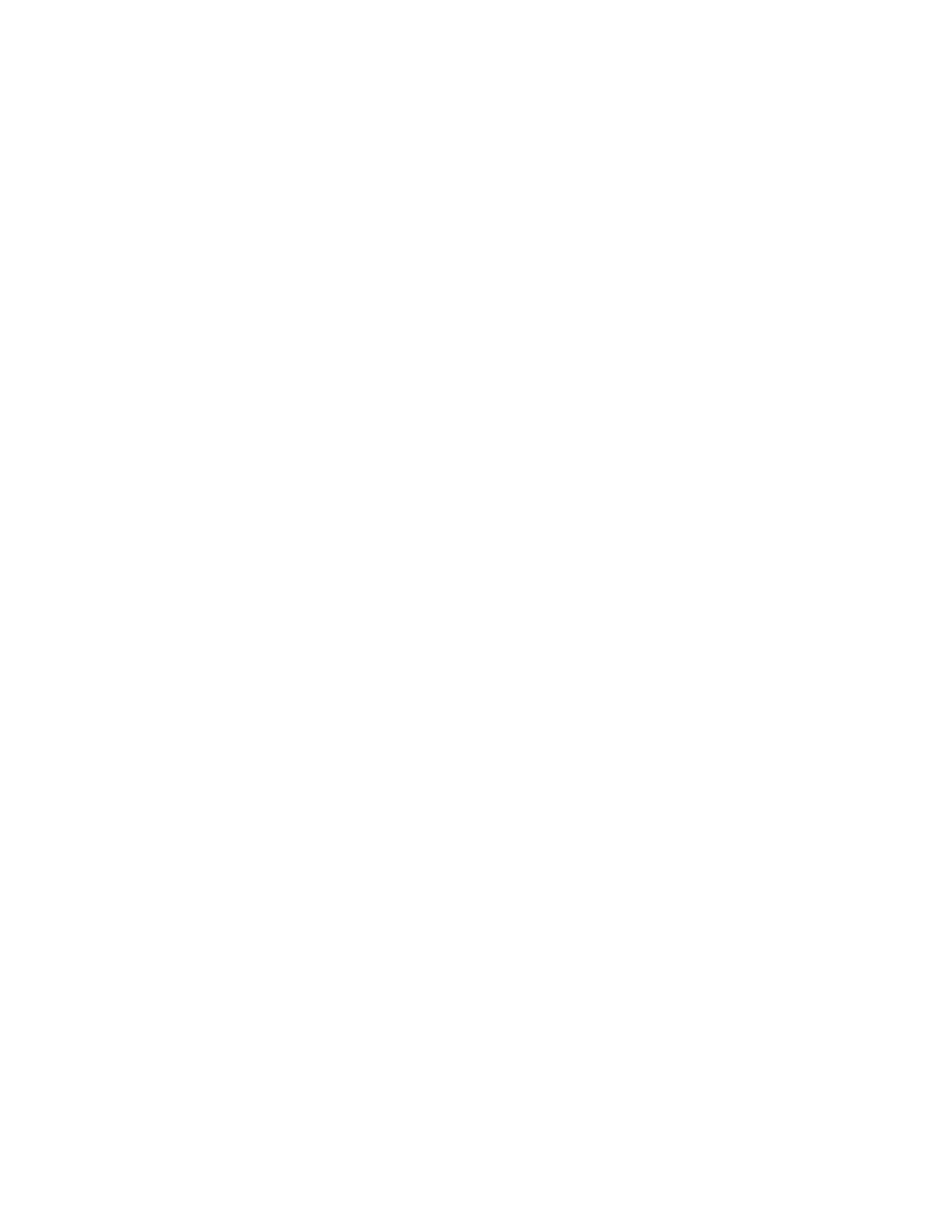
2
INTRODUCTION ...................................................................................................................................................4
1.0 TERMS & DEFINITIONS OF FUEL INJECTION MANAGEMENT SYSTEMS..............................................5
1.1 FUEL MANAGEMENT SYSTEM ...........................................................................................................................5
1.2 THROTTLE BODY INJECTION (TBI)....................................................................................................................5
1.3 MULTI-POINT FUEL INJECTION (MPFI).............................................................................................................. 6
1.4 ELECTRONIC CONTROL UNIT (ECU)................................................................................................................. 6
1.5 THROTTLE BODY ASSEMBLY (TBA) ..................................................................................................................6
1.6 FUEL INJECTORS............................................................................................................................................7
1.6.1 Bottom-Fed Fuel Injector........................................................................................................................ 7
1.6.2 Top-Fed Fuel Injector.............................................................................................................................7
1.6.3 High-Impedance Injectors.......................................................................................................................8
1.6.4 Low-Impedance Injectors........................................................................................................................8
1.7 MANIFOLD ABSOLUTE PRESSURE SENSOR (MAP) .............................................................................................8
1.8 THROTTLE POSITION SENSOR (TPS)................................................................................................................ 8
1.9 IDLE AIR CONTROL VALVE (IAC) ......................................................................................................................9
1.10 MANIFOLD AIR TEMPERATURE SENSOR...........................................................................................................9
1.11 COOLANT TEMPERATURE SENSOR .................................................................................................................9
1.12 OXYGEN SENSOR ......................................................................................................................................... 9
1.13 ELECTRIC IN-LINE FUEL PUMP...................................................................................................................... 10
1.14 ELECTRIC IN-TANK FUEL PUMP .................................................................................................................... 10
1.15 FUEL PUMP INLET FILTER ............................................................................................................................ 10
1.16 MAIN FUEL FILTER...................................................................................................................................... 11
1.17 FUEL PRESSURE REGULATOR...................................................................................................................... 11
1.18 FUEL RAILS................................................................................................................................................ 11
1.19 FUEL INJECTION CONTROL METHODS ........................................................................................................... 11
1.19A Speed Density EFI Systems................................................................................................................ 11
1.19B Alpha-N EFI Systems.......................................................................................................................... 11
1.20 CLOSED LOOP............................................................................................................................................ 11
1.21 OPEN LOOP ............................................................................................................................................... 12
2.0 HOW DOES FUEL INJECTION WORK?....................................................................................................... 12
2.1 SPEED DENSITY ...........................................................................................................................................14
2.2 ALPHA-N..................................................................................................................................................... 15
3.0 SKILL LEVEL REQUIRED............................................................................................................................. 16
4.0 TOOLS REQUIRED FOR INSTALLATION.................................................................................................... 16
5.0 ELECTRICAL CONNECTIONS ..................................................................................................................... 16
5.1 STEP-BY-STEP WIRING HARNESS INSTALLATION.............................................................................................. 17
5.2 NON-TERMINATED WIRE CONNECTION ...........................................................................................................17
5.3 PLUG-IN CONNECTIONS ................................................................................................................................ 18
5.4 IGNITION WIRING.......................................................................................................................................... 18
6.0 SOFTWARE INSTALLATION, SOFTWARE OPERATIONAL DESCRIPTION, AND COMPUTER
OPERATION .......................................................................................................................................................19
6.1 SOFTWARE INSTALLATION ............................................................................................................................. 19
6.1.1 Windows 95, 98, NT............................................................................................................................. 19
6.1.2 Windows 3.1 ........................................................................................................................................ 19
6.2 BASIC COMPUTER OPERATION....................................................................................................................... 19
6.3 SOFTWARE OPERATION AND NAVIGATION .......................................................................................................20
6.4 BASE MAPS .................................................................................................................................................21
6.5 ADVANCED AND BEGINNING USERS ................................................................................................................ 21
7.0 STEP-BY-STEP INITIAL STARTUP INSTRUCTIONS ..................................................................................21
8.0 STEP-BY-STEP BASIC TUNING................................................................................................................... 26
8.1 STARTUP / ENGINE WON’T START.................................................................................................................. 26