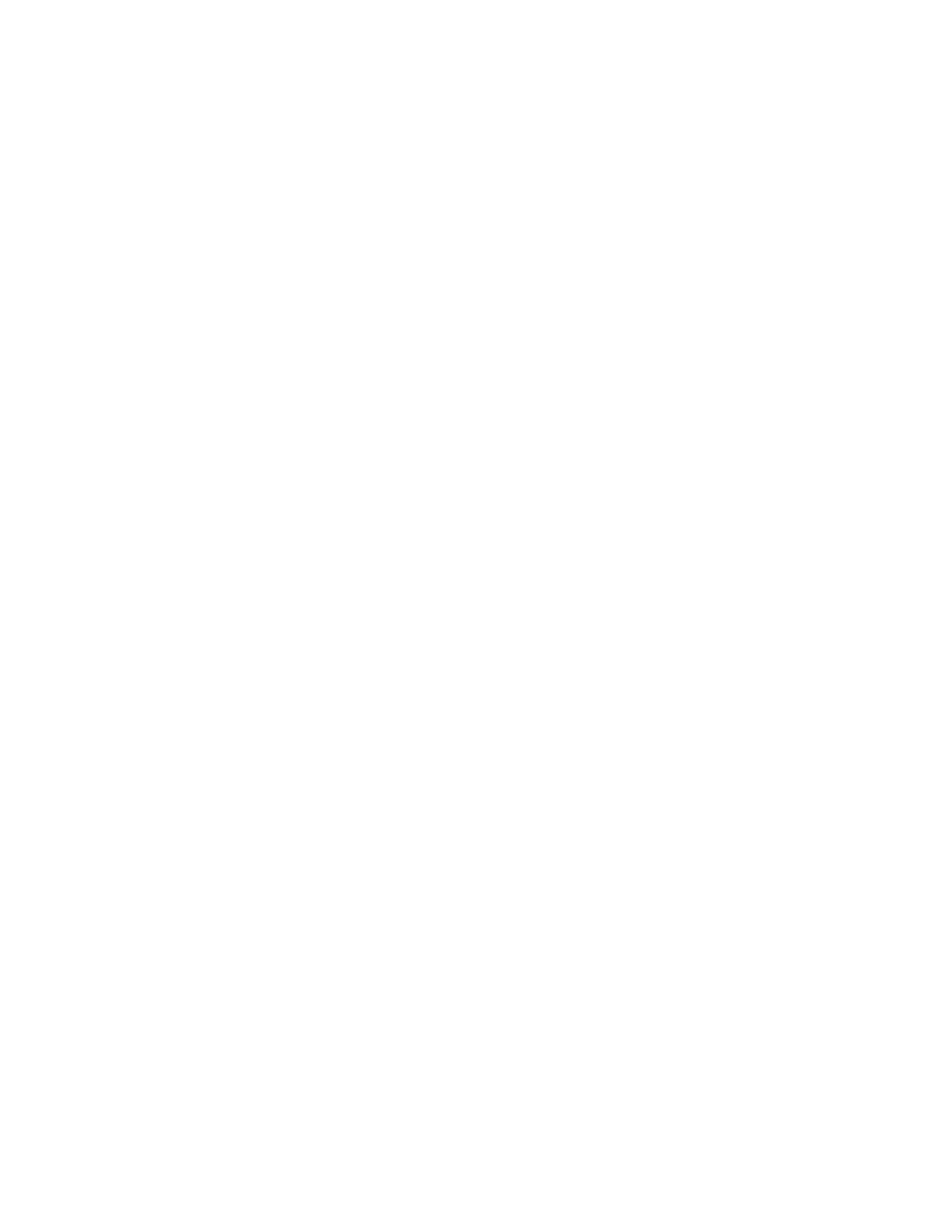
15 Goodyear Street, Irvine, California 92618 U.S.A.
Tel: (949) 951-1515 Fax: (949) 951-9237
Touch Up Calibration Procedure
Write a test program that will run each channel, but when you want to calibrate a channel, use
Dry Run and turn off every channel but the one that you are testing. For your test program,
make sure that the ALC is locked out in every segment. Also make sure to turn off Wait for Arc
and Touch Retract. Do not have any pulsing in your program for calibration. It is best to do the
calibration program in the Standard Mode.
To do a complete calibration you will need to run each channel near the high end of its range and
then near the low end of the range. You will need an independent test transducer for each of the
channels to measure parameter values and compare them to the 9900 program values:
For the Weld Current channel(s) you should have a calibrated current shunt or clamp-on
ammeter.
For Arc Voltage channel(s) you should have a 0 to 30 volt DC test power supply and a calibrated
DVM.
For Travel channel(s) you should have a calibrated tachometer with surface speed wheel capable
of measuring distance traveled.
Alternatively, depending on accuracy and traceability required, you could use the ammeter on
the welding power source for the weld current channel, a voltmeter and three 9 volt batteries for
the voltage channel, and do time/distance measurements for the travel and wire channels.
Touch Up Calibration Using Auto Calibration Routine (Analog Channels)
Weld Current Channel
1) Set up the system to weld. Make sure gas and water are on and set up some thick material or a
copper block to weld on during the calibration check. Use a tungsten size that will hold up to the
maximum current that will be used, for a few seconds. Set your test weld program to weld near
the high end of the weld current range (300 amps in the example screen). Call up the weld
program to run then de-select the unneeded channels from the Dry Run screen.
2) Connect the weld current test transducer or prepare to take readings from the welding power
supply if using that as the reference.
3) Run the program in the main weld segment for at least 8 seconds.
4) After running the test program, go into the Channel Configuration Editor and select the Current
channel that you are working with. First you will need to press the blue button. After you press
the Blue button, the calibration boxes will open up. Also, a green and a red button will appear.
The green button (marked “C”) is the “calculate” button, the red button is marked “U” and is the
“undo” button.