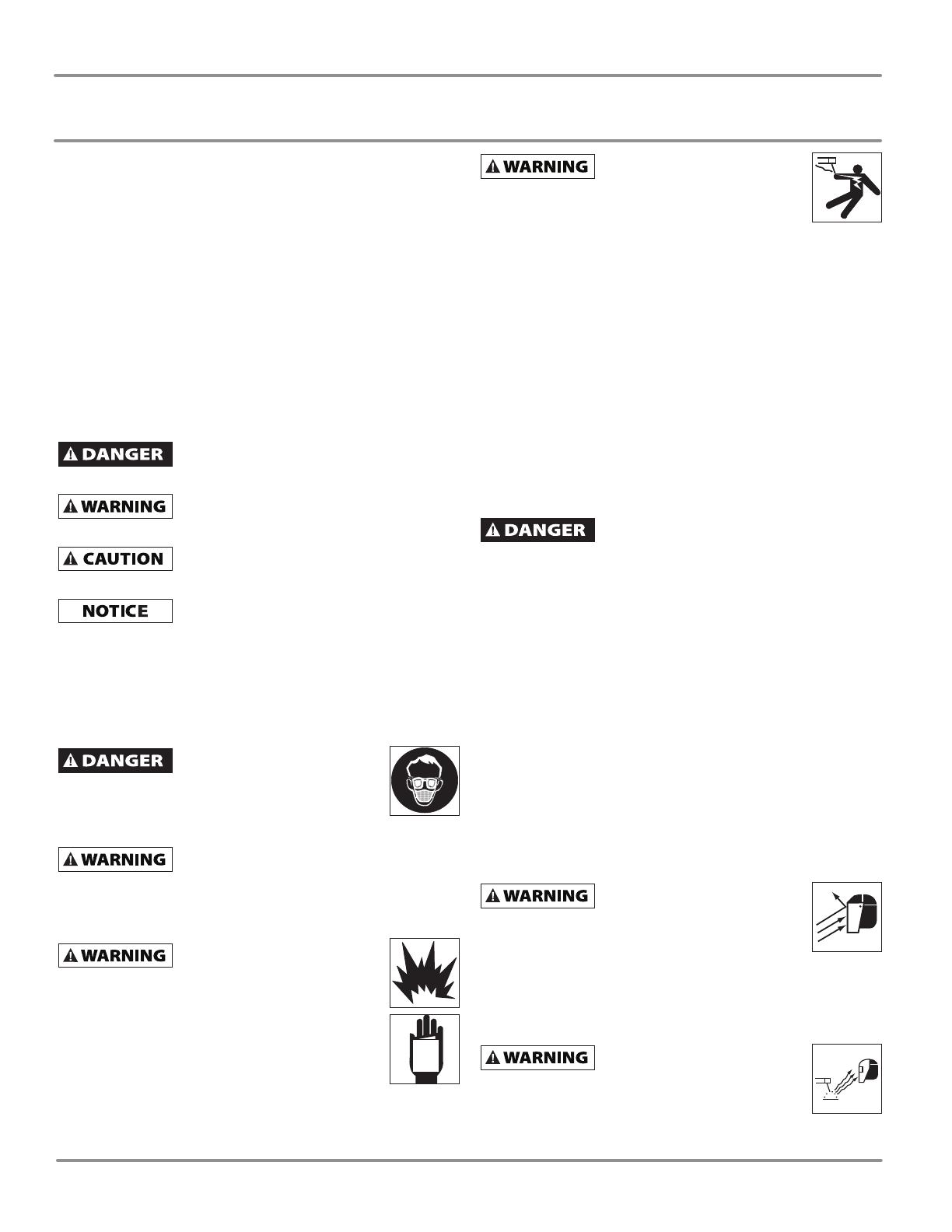
Operating Instructions and Parts Manual
2
www.campbellhausfeld.com
Unpacking
When unpacking, inspect carefully for any damage that may
have occurred during transit. Make sure any loose fittings and
screws, etc., are tightened before putting unit into service.
Report any missing or damaged items by calling 1-800-746-
5641.
READ & FOLLOW ALL INSTRUCTIONS
SAVE THESE INSTRUCTIONS
DO NOT DISCARD
Safety Guidelines
This manual contains information that is very important to know
and understand. This information is provided for SAFETY and
to PREVENT EQUIPMENT PROBLEMS. To help recognize this
information, observe the following symbols.
Danger indicates an imminently hazardous
situation which, if not avoided, WILL result
in death or serious injury.
Warning indicates a potentially hazardous
situation which, if not avoided, COULD
result in death or serious injury.
Caution indicates a potentially hazardous
situation which, if not avoided, MAY result
in minor or moderate injury.
Notice indicates important information,
that if not followed, may cause damage to
equipment.
NOTE: Note means any additional information pertaining to the
product or its proper usage.
General Safety Information
CALIFORNIA PROPOSITION 65
This product, when used for
welding, produces fumes
or gases which contain chemicals known to the
State of California to cause birth defects (or other
reproductive harm) and, in some cases, cancer
(California Health & Safety Code Section 25249.5 et seq.).
The power cord and other cables on
this product contain chemicals, including
lead, known to the State of California to cause cancer and birth
defects or other reproductive harm. Wash hands after handling.
GENERAL SAFETY
Always keep a fire extinguisher
accessible while performing arc
welding operations.
u Before starting or servicing any electric arc
welder, read and understand all instructions.
Failure to follow safety precautions or
instructions can cause equipment damage and/
or serious personal injury or death.
u All installation, maintenance, repair and operation
of this equipment should be performed by qualified persons
only in accordance with national, state, and local codes.
Improper use of electric arc
welders can cause electric
shock, injury, and death! Take all precautions
described in this manual to reduce the possibility of
electric shock.
u Verify all components of the arc welder are clean and in
good condition prior to operating welder. Be sure insulation
on all cables, torch and power cord is not damaged. Always
repair or replace damaged components before operating
the welder. Always keep welder panels, shields, etc. in place
when operating welder.
u Always wear dry, protective clothing, welding gloves and
insulated footwear when operating unit.
u Always operate welder in a clean, dry, well ventilated
area. Do not operate welder in humid, wet, rainy or poorly
ventilated areas.
u Be sure work piece is properly supported and grounded prior
to beginning any electric arc welding operation.
u Spread out coiled welding cable before use to avoid
overheating and damage to insulation.
Never immerse wire or torch in water. If
welder becomes wet for any reason, be
absolutely certain it is completely clean and dry before use!
u Always shut equipment off and unplug power cord prior to
moving the unit.
u Always attach the work lead first.
u Verify work piece is securely grounded.
u Always shut off electric arc welding equipment when not in
use and cut off any excess wire from torch.
u Never allow any part of the body to touch welding wire and
ground or grounded work piece at the same time.
u Awkward welding conditions and positions can be
electrically hazardous. When crouching, kneeling or at
elevations, be sure to insulate all conductive parts, wear
appropriate protective clothing and take precautions to
prevent injury from falls.
u Never attempt to use this equipment at current settings or
duty cycles higher than specified on equipment labels.
u Never use an electric arc welder to thaw frozen pipes.
Flying sparks and hot metal
can cause injury. As welds
cool, slag can be thrown off. Take all precautions
described in this manual to reduce the possibility of
injury from flying sparks and hot metal.
u Wear ANSI approved face shield or safety glasses with side
shield protection when chipping or grinding metal parts.
u Wear ear plugs when welding overhead to prevent spatter or
slag from falling into ears.
Electric arc welding operations
produce intense light and heat
and ultraviolet (UV) rays. This intense light and UV
rays can cause injury to eyes and skin. Take all
precautions described in this manual to reduce the
possibility of injury to eyes and skin.
Please read and save these instructions. Read carefully before attempting to assemble, install, operate or maintain the
product described. Protect yourself and others by observing all safety information. Failure to comply with instructions
could result in personal injury and/or property damage! Retain instructions for future reference.
MANUAL