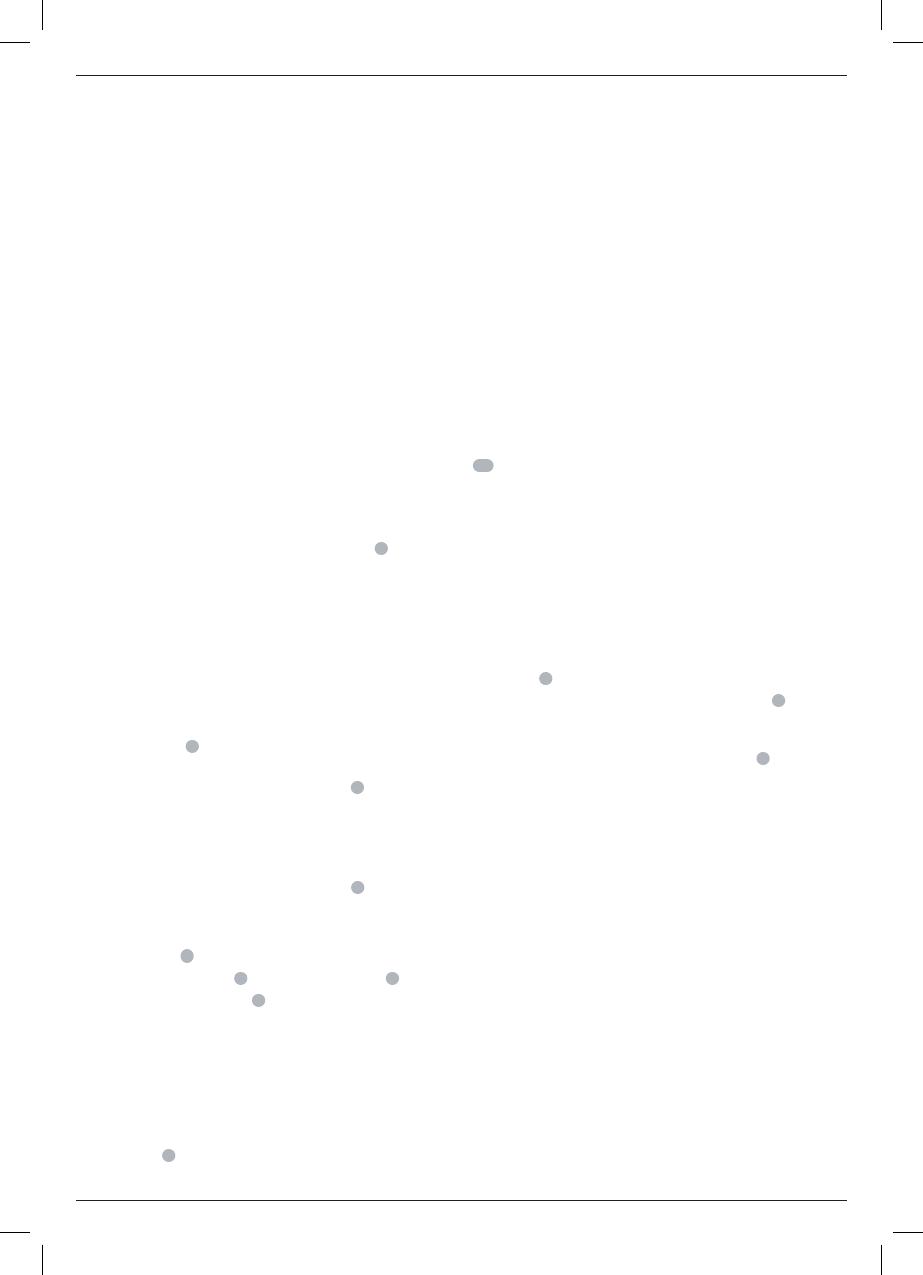
21
ENGLISH
1. Pull forward, then rotate collar in increase direction
(stamped on adjustment collar) to increase the amount of
clutch engagement and torque output.
2. Maximum rotation of the collar in the increase direction
results in full clutch engagement and maximum torque
output and fastener capacity. Collar and adjustable stop will
not screw off clutch housing.
3. Test drive a fastener into a scrap piece to check proper
fastener seating. It is normal after a period of use to require
a slightly different collar setting due to wear on the clutch
faces.
NOTE: With Versa Clutch®, the operator has the ability to
“override” clutch ratchet if a fastener hits a wood knot, variable
hardness in steel work pieces or incorrect pilot holes. Increased
operator pressure will usually cause the clutches to pick-up
and continue to seat the fastener. Further, a quick twist of the
collar will change the clutch setting to overcome most driving
difficulties and will provide for immediate change in torque
output giving the operator the option to drive a wide range of
fastener sizes.
Using a Nutsetter (Fig. C)
DW263/DW264
1. For screws with sealing washers, turn the collar
4
until
the end of the nutsetter is flush with the end of the depth
locator.
If required, turn the collar until the nutsetter is recessed
approximately 2 mm into the depth locator.
NOTE: ALWAYS refer to the screw manufacturer’s
specifications for the proper sealing washer settings in
different applications.
2. Drive a screw into a scrap piece and check the distance
between the washer and the material.
3. Turn the collar
4
counterclockwise or clockwise to decrease
or increase the driving depth as required.
4. Drive another screw and readjust the collar
4
until the
desired setting is achieved.
Depth Locator (Fig. D)
DW263/DW264
This model is supplied with two depth locators
5
to
accommodate different bits, holders, sockets and adaptors.
To Change Depth Locators
1. Pull the collar
4
assembly off the tool.
2. Hold the depth locator
5
and unscrew the collar
4
.
3. Replace the depth locator
5
.
4. To reassemble, proceed in reverse order.
Forward/Reverse Switch (Fig. E)
WARNING: Always wait until the motor has come to
a complete standstill before changing the direction of
rotation.
Select the forward or reverse rotation by moving the forward/
reverse switch
3
in the direction indicated by the arrows.
OPERATION
Instructions for Use
WARNING: Always observe the safety instructions and
applicableregulations.
WARNING: To reduce the risk of serious personal
injury, turn tool off and disconnect tool from power
source before making any adjustments or removing/
installing attachments or accessories. Be sure the
trigger switch is in the OFF position. An accidental start-up
can cause injury.
Proper Hand Position (Fig. F)
WARNING: To reduce the risk of serious personal injury,
ALWAYS use proper hand position as shown.
WARNING: To reduce the risk of serious personal injury,
ALWAYS hold securely in anticipation of a sudden
reaction.
Proper hand position requires one hand on the main handle
14
, as shown.
For best results, hold the screwdriver with the hand directly in
line with the fastener and press the variable speed switch with
the last one or two fingers of the hand, as shown. This reduces
the chance of the screw slipping from the drive accessory when
pressure is applied.
Screwdriving or Nutsetting (Fig. A1)
1. Select the appropriate bit for the screw (or nut) to be driven.
2. Select forward or reverse rotation as described above.
DW263: For nutsetting, always use the correct depth
locator
5
.
3. To run the tool, press the variable speed switch
1
. The
pressure exerted on the variable speed switch determines
the tool speed.
NOTE: If necessary, press the lock-on button
2
for
continuous operation and release the variable speed switch.
The lock-on button only works in full speed, forward and
reverse rotation.
To stop the tool in continuous operation, press the switch
briefly and release it.
WARNING: ALWAYS turn the tool off when work is
finished and before unplugging.
4. To drive the screw, place it on the bit or into the socket,
press the variable speed switch and push the screw into the
workpiece with a smooth, continuous motion. When the
screw is seated, a buzzing sound will come from the front of
the tool to indicate that the clutch has disengaged.
5. To stop the tool, release the switch.
MAINTENANCE
Your
power tool has been designed to operate
over a long period of time with a minimum of maintenance.
Continuous satisfactory operation depends upon proper tool
care and regularcleaning.