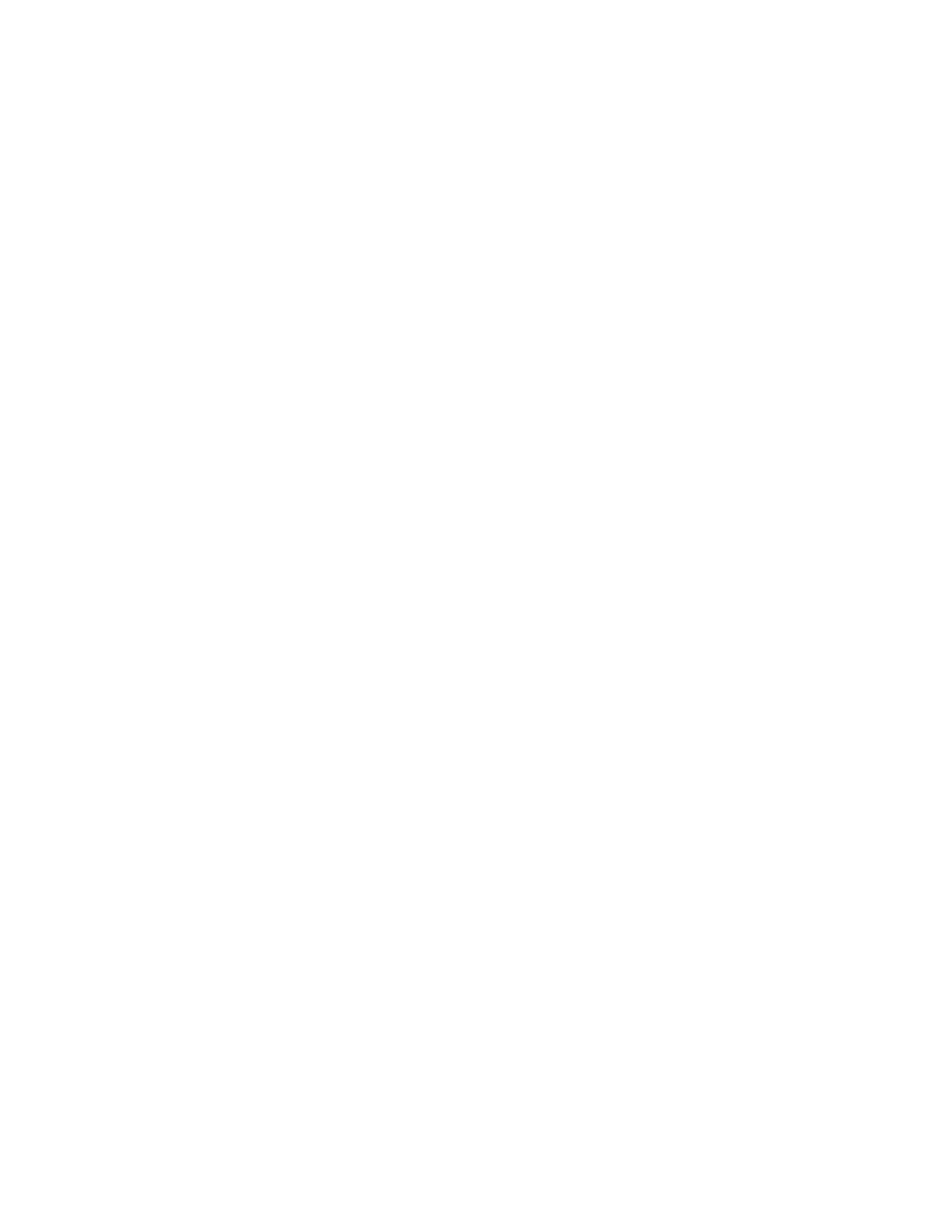
Impinger I -–1000 Series Service Manual - International 2
TABLE OF CONTENTS
TABLE OF CONTENTS..............................................................................................................................................2
SEQUENCE OF OPERATIONS 1002/1003...............................................................................................................3
SEQUENCE OF OPERATIONS 1106........................................................................................................................4
SEQUENCE OF OPERATIONS 1028 / 1029 / 1228 / 1229 ......................................................................................5
SEQUENCE OF OPERATIONS 1030........................................................................................................................6
SEQUENCE OF OPERTIONS 1032 ..........................................................................................................................7
SEQUENCE OF OPERATIONS / 1033, 1034, 1046, 1047 .......................................................................................8
SEQUENCE OF OPERATIONS 1042 / 1043 / 1242 / 1243 ....................................................................................10
SCHEMATIC / 1002, 1003 .......................................................................................................................................12
SCHEMATIC / 1006 TO SERIAL NUMBERS Q14279.............................................................................................13
SCHEMATIC / 1028, 1029, S/N Q19071 & BELOW................................................................................................14
SCHEMATIC / 1028, 1029, S/N Q19078 & ABOVE.................................................................................................15
SCHEMATIC / 1030, TO S/N Q17170......................................................................................................................16
SCHEMATIC / 1030, S/N Q17171 & ABOVE...........................................................................................................17
SCHEMATIC / 1032. S/N Q19077 & BELOW ..........................................................................................................18
SCHEMATIC / 1032, S/N Q19078 & ABOVE...........................................................................................................19
SCHEMATIC / 1033, 1034, 1046, 1047 ...................................................................................................................20
SCHEMATIC / 1042, 1043, S/N Q14279 & BELOW................................................................................................21
SCHEMATIC / 1042, 1043, S/N Q14280 & ABOVE.................................................................................................22
SCHEMATIC / 1228. 1229, S/N Q14790 & BELOW................................................................................................23
SCHEMATIC / 1228, 1229, S/N Q14791 & ABOVE.................................................................................................24
SCHEMATIC / 1242, 1243 .......................................................................................................................................25
TROUBLESHOOTING GUIDE 1000 & 1200 / GAS OVENS ..................................................................................26
TROUBLESHOOTING GUIDE 1000 & 1200 SERIES / ELECTRIC OVENS...........................................................39
TROUBLESHOOTING / GAS OVENS 1033, 1034, 1046, 1047..............................................................................46
REMOVAL, INSTALLATION & ADJUSTMENTS .....................................................................................................53
MODEL SERIES 1000 &1200...............................................................................................................................53
PARTS / MODEL SERIES 1000 & 1200 - GENERAL..............................................................................................80
BLOW UP / 1000, 1200 – GENERAL.......................................................................................................................81
PARTS / MODEL 1002-1003 , S/N 2584 TO 4389 ..................................................................................................82
BLOW UP / 1002, 1003 – S/N 2584 to 4389............................................................................................................83
PARTS / MODEL 1002-1003, S/N 4390 & UP.........................................................................................................84
BLOW UP / 1002, 1003 – S/N 4390 & ABOVE........................................................................................................85
PARTS / MODEL 1006.............................................................................................................................................86
BLOW UP / 1006 ......................................................................................................................................................87
PARTS / 1028-1029-1032 ........................................................................................................................................88
BLOW UP / 1028, 1029, 1032 ..................................................................................................................................89
PARTS/ MODEL 1030..............................................................................................................................................90
BLOW UP / 1030 ......................................................................................................................................................91
PARTS / 1042, 1043.................................................................................................................................................92
BLOW-UP / 1042, 1043............................................................................................................................................93
PARTS / 1033, 1034, 1046, 1047.............................................................................................................................94
BLOW-UP / 1033, 1034, 1046, 1047........................................................................................................................95
PARTS / 1228-1229..................................................................................................................................................96
BLOW UP / 1228, 1229 ............................................................................................................................................97
PARTS / 1242, 1243.................................................................................................................................................98
BLOW - UP / 1242, 1243..........................................................................................................................................99
PARTS / OVEN BACK - GAS.................................................................................................................................100
BLOW UP / OVEN BACK – GAS ...........................................................................................................................101
PARTS / OVEN BACK- ELECTRIC........................................................................................................................102
BLOW UP / OVEN BACK – ELECTRIC .................................................................................................................103
PARTS / CONVEYOR MOTOR ASSEMBLY S/N 4390 & ABOVE ........................................................................104
BLOW UP / CONVEYOR MOTOR ASSEMBLY S/N 4390 & ABOVE ...................................................................105
PARTS / SERIES 1000 – CONVEYOR..................................................................................................................106
BLOW UP / SERIES 1000 CONVEYOR ................................................................................................................107
PARTS / SERIES 1200 - CONVEYOR CONTROL................................................................................................108
BLOW UP / SERIES 1200 – CONVEYOR CONTROL ..........................................................................................109
PARTS / SERIES 1200 – CONVEYOR..................................................................................................................110
BLOW UP / SERIES 1200 – CONVEYOR .............................................................................................................111