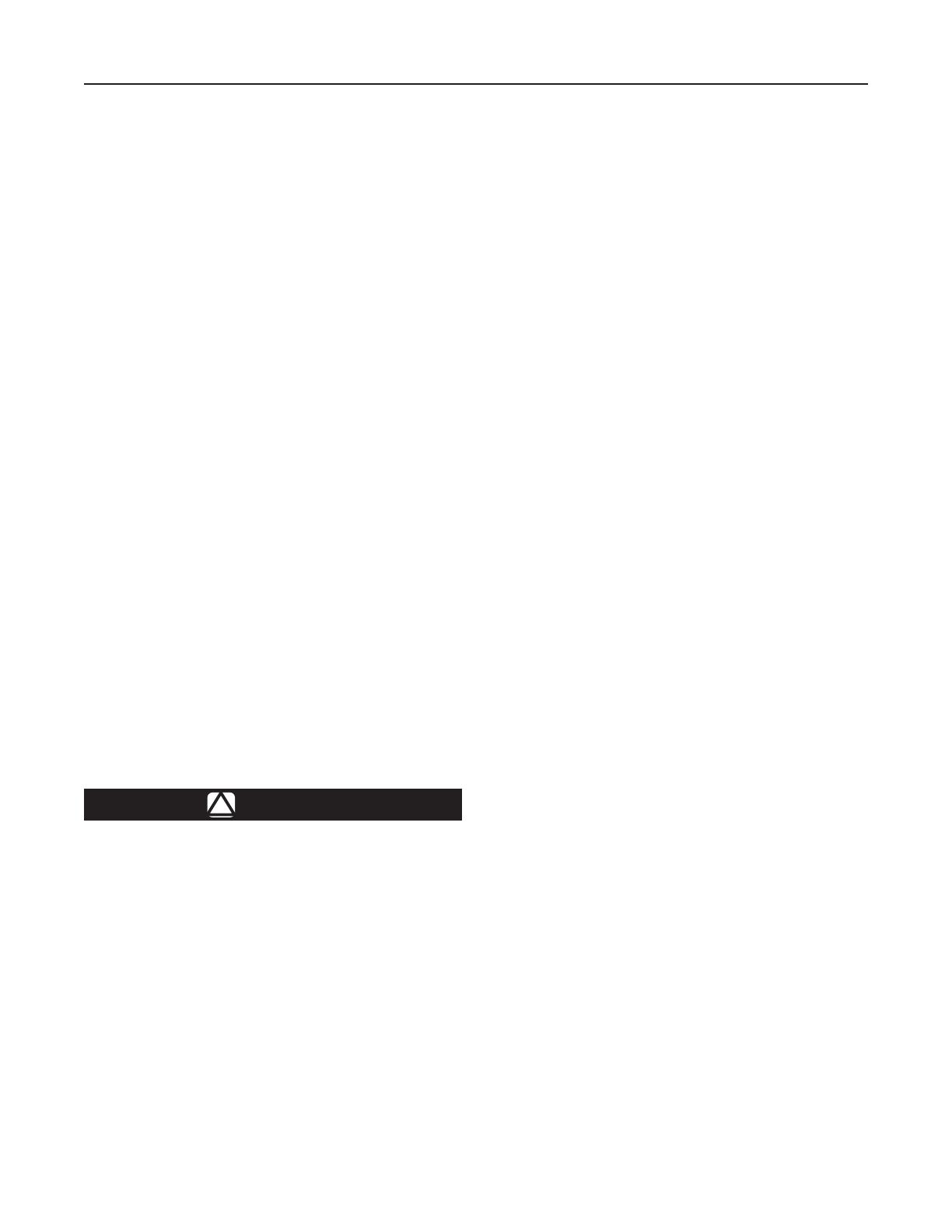
The arrestor should be positioned such that the entire
arrestorisaccessibleforremoval.Installtheunit
suchthattheowarrowlocatedontheunitpointsin
thedirectiontravellingwiththeproductow.Models
thathavedrainplugsaredesignedforhorizontal
installation and should be installed with the drain plugs
alignedatthebottomoftheunit.Modelsthathave
pressure taps are designed to allow pressure gauges
tobeinstalledonbothsidesoftheamecellassembly
todetermineblockage.Thepressuretapsshould
bealignedatthetoptoalloweasyviewingofthe
gauges.Unitsthatareequippedwithoptionalinternal
cleaningsystemsshouldbeconnectedtoasourceof
cleaning media such as water, steam or other suitable
solvent.Observerecommendedinstallationpracticeas
detailedbendsand/orowobstructionsection.
Flow Direction
The DFA Series is not bi-directional when temperature
sensorsarerequiredunlessasensorisinstalledon
bothsidesofthearrestorelementassembly.However,
detonationarrestorsareratedforstabilizedburning
andbi-directional.Allarrestorscoveredinthismanual
canbeinstalledeitherverticallyorhorizontally.
Considerationshouldbegiventonon-symmetrical
assemblies that include features such as clean-out
ports, temperature monitoring device or other options
that might have a preferred installation direction to suit
theneedsofthecustomer.
Piping Expansions and
Reductions Adjacent to Detonation
Flame Arrestor
WARNING
!
No instrument, tubing or other device
whatsoever shall circumvent the
detonation ame arrestor in such a
manner to allow a ame path to exist
around the ame element of the arrestor.
When instrumentation is installed in
such a manner that it creates a path
circumventing the ame element of an
arrestor, measures must be taken to
prevent passage of ame through the
instrumentation device and/or system.
Instrumentation must be capable
of withstanding the maximum and
minimum pressures and temperatures to
which the device may be exposed and at
a minimum be capable of withstanding
a hydrostatic pressure test of 350 psig /
24 bar.
TheDFASeriesdetonationamearrestormaybe
installedinanyvaporcontrollinethatissmallerthan
orequaltothenominalpipediameterofthearrestor’s
connectionanges. Whenitisnecessarytoincrease
the diameter of the piping on the downstream side
(unprotected)ofthedetonationamearrestor,alength
ofpipeatleast120pipediametersmustbeinstalled
betweenthedetonationamearrestorandthe
expansion.Apipediameterisconsideredastheinside
diameterofpipehavinganominalsizeequaltothe
detonationamearrestor’sconnectinganges.
Maintenance
Detonation Flame Arrestor Element
Assembly Cleaning
1. Keep the element openings clean to prevent
lossofefciencyinabsorbingheat.Removethe
elementassemblyandcleantheelementsto
prevent the clogging of particulates and other
contaminantsontheopenings.Cleantheelement
with a suitable cleaning media (solvent, soap,
waterorsteam)thenblowdryusingcompressed
air.Becarefulnottodamageordentthecell
openings as this would hamper the effectiveness
oftheunit.Donotcleanthearrestorelementsby
roddingwithwireorotherhardobjectstoremove
blockages.Cleaningtheelementswithwireor
otherhardobjectscoulddamagetheelementsand
seriouslyimpairthearrestor’sperformance.Ifthe
arrestorelementcannotbecleanedsatisfactorily,
replaceit.
2. For best cleaning results, use a high pressure
sprayerwithspraywand(1500psigto3000psig/
103to207bar)tocleantheentireelement
surface.Holdthespraynozzleperpendicular
tothesurfacebeingcleanedtomaximizespray
mediapenetrationintotheelement.Alternately
sprayeachsideoftheelementsurfaceuntilclean.
3. Thecleaningintervalshouldbegovernedbythe
amountandtypeofparticulateinthesystemto
whichitisinstalledandmustbedeterminedby
theuser.Todeterminethemaintenanceinterval,
theusershouldchecktheelementintherstfew
monthsofoperationtondhowquicklyparticulate
accumulatesinthecells.
7
DFA Series
North America Only