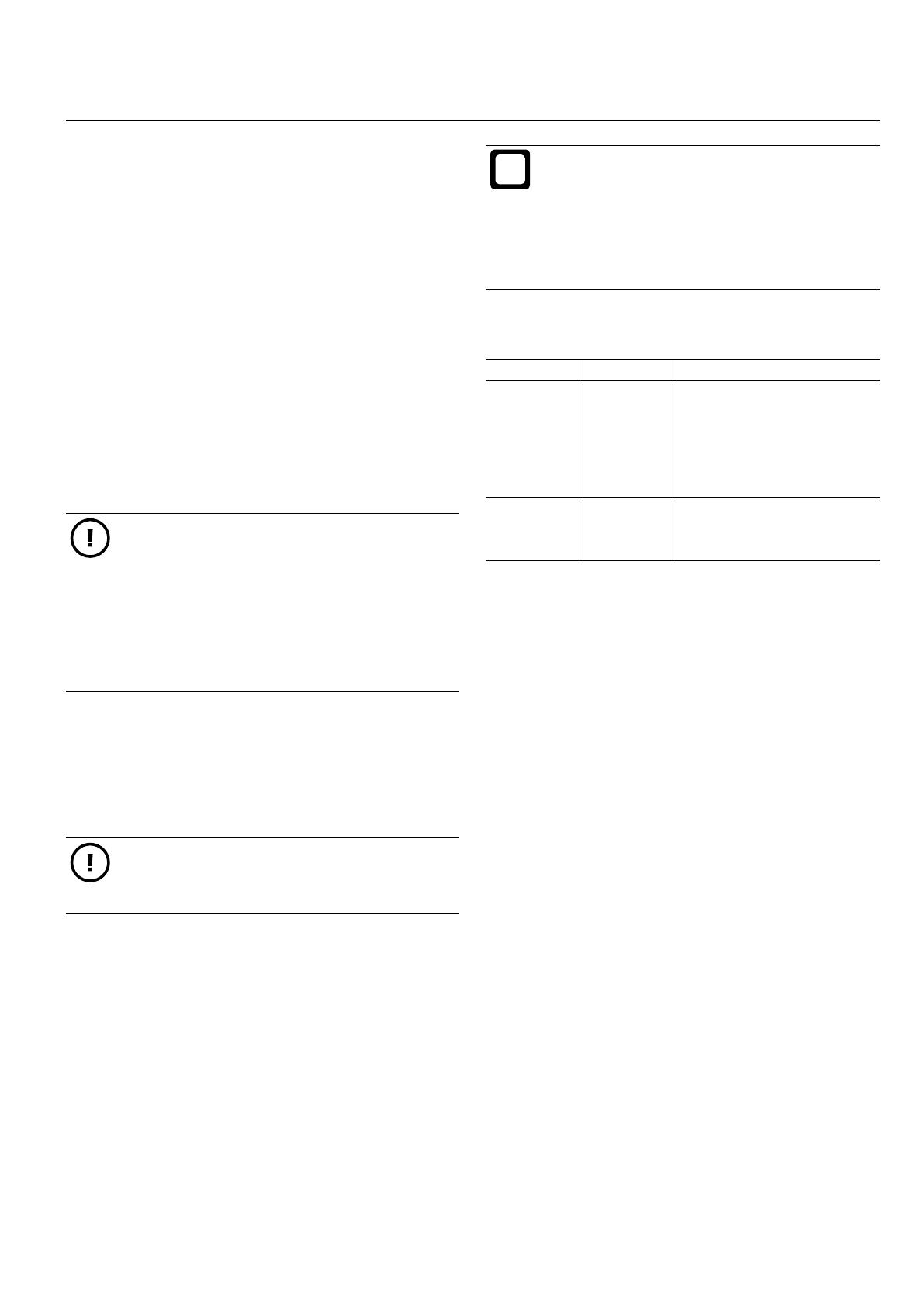
OPERATION | Maintenance and care
982001-TERRA-M2-M4-EN04.1 | www.ochsner.com 9
ments. Intermittent ventilation is considerably more energy
efcient than permanent ventilation, and therefore saves
money. Avoid permanent ventilation.
4.1.3 Heating setback program
From an energy efciency point of view, using a time
program to reduce the heating ow temperature is not
recommended for low temperature heating systems (such
as underoor heating). These systems are slow to respond
and, due to the additional output from the system required
following the end of the setback phase, it is possible that
the second heat generator (boiler, electric immersion heat-
er) will cut in. This can lead to higher operating costs.
4.1.4 Screed drying program
Screed drying mode with a brine/water heat pump (screed,
construction moisture) is not permissible.
Material damage
Screed drying mode with this heat pump leads to
efciency losses, formation of frost with faulting in
the ground, and even system failure.
»
For screed drying mode, use an electric im-
mersion heater as the heat generator. The
electric immersion heater should be installed
in the heat pump ow (indoor unit option), in
the heat pump buffer tank or in the low loss
header.
5. Maintenance and care
We recommend an annual inspection and if necessary
have your heat pump serviced by OCHSNER Customer
Service.
Material damage
Maintenance work on electrical components of the
heat pump may be carried out only by qualied
contractors.
»
If it is necessary to clean the casing sections of the
indoor unit, use only a damp cloth (with water or a
weak soapy solution). Do not use any abrasive or ag-
gressive cleaning materials.
»
During the building phase, protect the indoor unit from
dirt and dust with a suitable covering. Use the plastic
cover provided.
»
Ensure that the heating circuit is lled with sufcient
water.
Information
Ensure that the refrigerant circuit of your heat pump
is tested for leaks once a year (in acc. with Regu-
lation (EU) no. 517/2014).
»
Ensure year-round access to soldered joints in
the refrigerant circuit.
»
Document the results of the leakage test in the
system test report.
6. Problem solving
Problem Cause Solution
Too little DHW
is available
or the cen-
tral heating
system is too
cold.
The power
supply to the
appliance has
been cut off
Check the safety device on the
main distributor board for your
house. Switch the safety device
back on. If the safety device trig-
gers again after being switched
back on, contact a qualified con-
tractor or OCHSNER Customer
Service.
The appliance
is leaking
water.
The drain
for the safe-
ty valve is
blocked.
Clean the safety valve drain. (see
page 26, Safety valve drain)
If you have a problem that you cannot resolve, contact
the system installer, a qualied contractor or OCHSNER
Customer Service.
Faults are displayed as”Er XXX”on the master controller of
the OTE control unit. If a fault occurs, contact your system
installer. The system installer knows your hydraulic system
and how it operates. The causes of faults can often be
found in the settings or in the hydraulics.
Before contacting the installer, make a note of the serial
number and the heat pump model. The serial number and
heat pump model of your appliance are shown on the name
plate. The name plates are attached to the back of the
appliance on the outside and behind the front appliance
casing panel (control box outer side).
►Customer service hotline for Austria:
Tel: +43 (0) 504245 - 499
Email: kundendienst@ochsner.at
►Customer service hotline for Germany:
Tel: +49 (0) 69 256694 - 495
Email: kundendienst@ochsner.de
►Customer service hotline for Switzerland:
Tel: +41 (0) 800 100 - 911
Email: kundendienst@ochsner.de