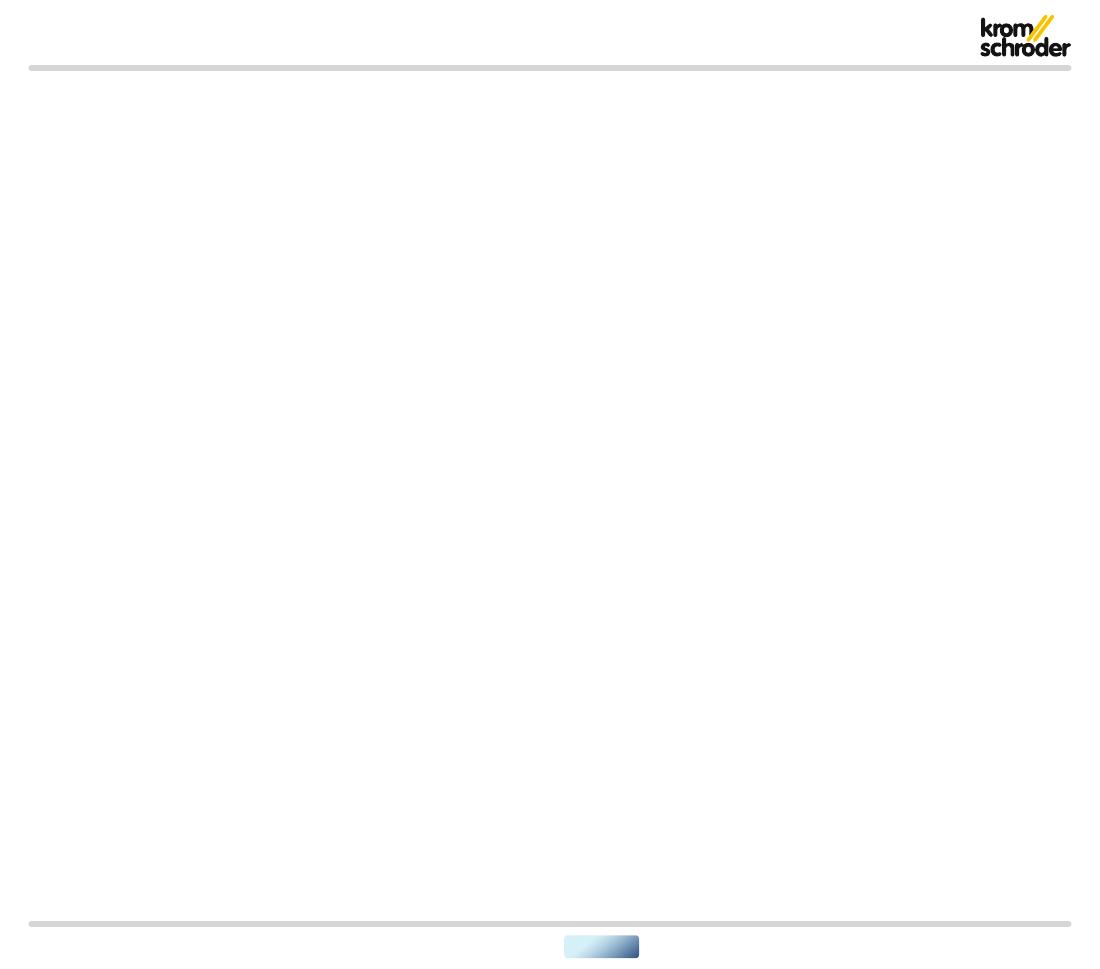
BCU 580 · Edition 11.15 3
▼ = To be continued
10.6.7 Air actuator can be activated externally on start-up ... 83
10.6.8 Air actuator in the event of fault ................... 83
10.6.9 Capacity control (bus)............................ 84
10.7 Valve check .................................89
10.7.1 Valve proving system ............................ 89
10.7.2 Relief valve (VPS) ................................ 90
10.7.3 Measurement time Vp1 .......................... 90
10.7.4 Valve opening time 1 tL1 ...........................91
10.8 Behaviour during start-up......................92
10.8.1 Minimum pause time tBP ......................... 92
10.9 Manual mode ...............................93
10.9.1 Operating time in Manual mode ................... 93
10.10 Functions of terminals 50, 51, 65, 66, 67 and 68...94
10.10.1 Function of terminal 50 .......................... 94
10.10.2 Function of terminal 51 .......................... 94
10.10.3 Function of terminal 65.......................... 94
10.10.4 Function of terminal 66.......................... 95
10.10.5 Function of terminal 67 .......................... 95
10.10.6 Function of terminal 68.......................... 95
10.11 Password...................................96
10.12 Fieldbus communication . . . . . . . . . . . . . . . . . . . . . . 96
11 Selection .....................................97
11.1 Type code ...................................97
12 Project planning information.....................98
12.1 Installation...................................98
12.2 Commissioning ..............................98
12.3 Electrical connection ..........................99
12.3.1 OCU .......................................... 99
12.3.2 Safety current inputs.............................100
12.3.3 UVD control....................................101
12.4 Actuators ..................................102
12.4.1 IC20..........................................102
12.5 Parameter chip card .........................103
12.6 Protecting the pilot burner from overload ........103
12.7 Calculating the safety time tSA........................104
12.8 Fifth or switchable gas valve on BCU..F3 .........105
13 Accessories ................................. 106
13.1 BCSoft .....................................106
13.1.1 Opto-adapter PCO 200 ...........................106
13.1.2 Bluetooth adapter PCO 300 .......................106
13.2 OCU ......................................106
13.3 Connection plug set..........................106
13.4 Stickers for labelling.......................... 107
13.5 “Changed parameters” stickers ................ 107
14 OCU .......................................108
14.1 Application .................................108
14.2 Function ...................................109
14.2.1 Manual mode ..................................109
14.3 Electrical connection ......................... 110
14.4 Installation ................................. 110
14.5 Selection ................................... 110
14.6 Technical data for OCU ........................111
15 BCM 500 ....................................112
15.1 Application ..................................112
15.2 Function ....................................112
15.3 Electrical connection ..........................112
15.4 Installation ..................................112
15.5 Selection ................................... 113
15.6 Technical data .............................. 113
16 Technical data ................................114
16.1 Electrical data ............................... 114
16.2 Mechanical data ............................ 115
16.3 Environment ................................ 115
16.4 Dimensions ................................ 115
16.5 Safety-specific characteristic values..............116
16.6 Converting units..............................117
17 Maintenance .................................118
18 Legend ......................................119
19 Glossary....................................120
Contents