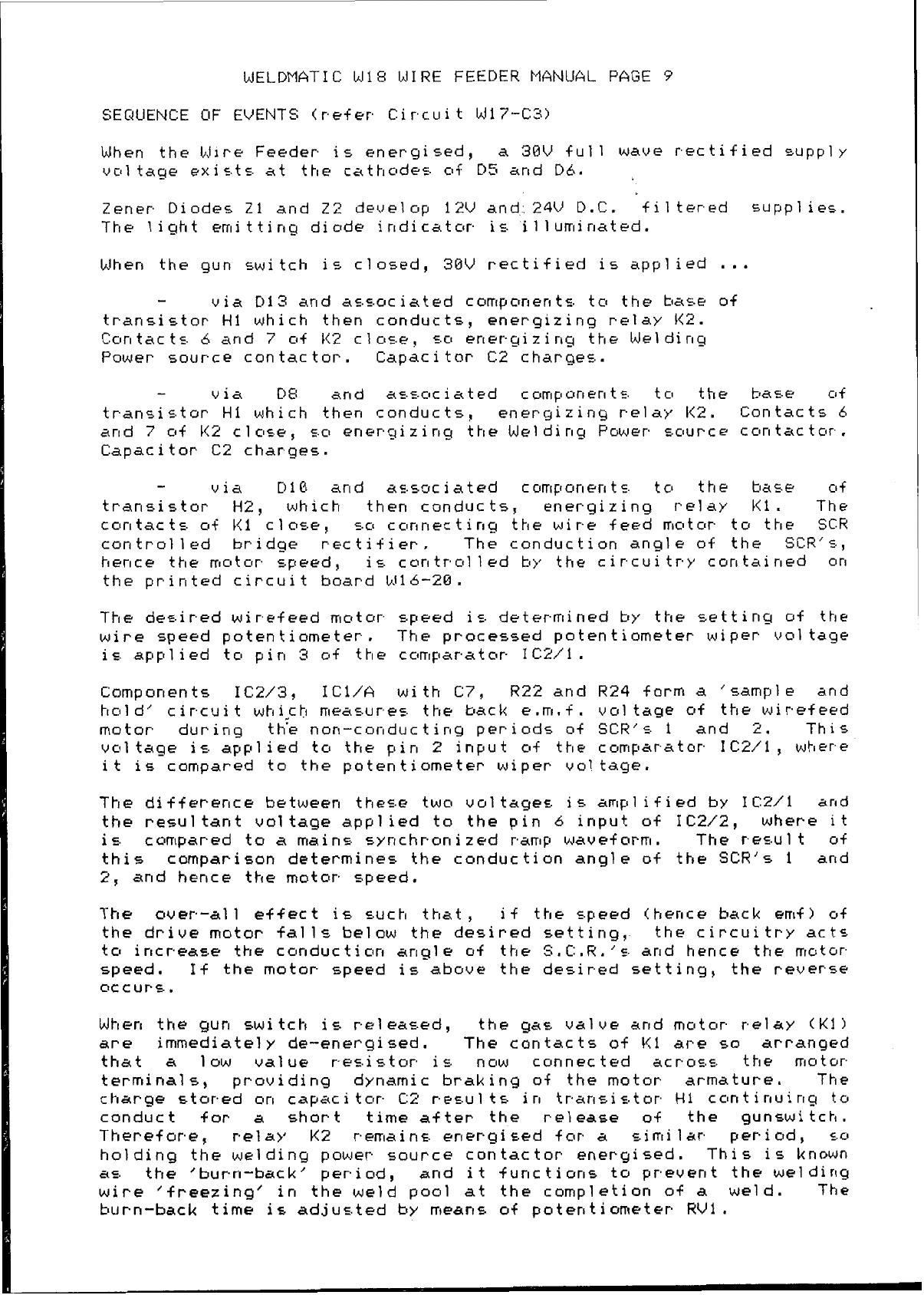
WELDMATIC
W1
b
W1
RE
FEEDER kI/;NUAL
PAGE
9
SEQUENCE
OF
EVENTS (refer Circui
t
W17-C3)
When the Mire Feeder
is
energised,
a
38U
full wave rectified supply
uul tage exists
at
the cathcades
of
D5
and
D6.
Zener Diodes
21
and
22
develop
12U
and:,
24U
D.C.
fil
tered supplies.
The
1
iqht emitting diode indicator
is
illuminated.
When the gun switch is closed,
30V
rectified is applied
...
-
via
D13
and associated components
tcl
the
tlase of
transistor
H1
which then conducts, energizing
relay
K2.
Contacts
6
and
7
of
K2
c
l
cts.e,
5.~1
enerqi
zi
ng the Wel ding
Power source contactor. Capaci tor
C2
charges.
-
via
D8
and
ac.c.ociiated componentE.
tcl
the
base
of
transistor
HI
which then conducts, energizing relay
KZ.
Contacts
6
and
7
of
K2
c
1
else,
5.0
energizing the We1 di ng Power murce ccln
tac
tor,
Capac
i
tor
C2
charges
.
I
via D10
and associated components. to the
base
of
transistor
HZ,
which then conduct5, energizing
relay
K1.
The
contactc. of
K1
close,
5.0
connectirlg the wire feed
rrlotur
tu
the
SCR
controlled bridge rectifier. The conduction angle
of
the
SCR‘s,
hence the mutor
speed,
is
contr.al1ed
tly
the circuitry contained on
the printed circuit board
W16-20.
The desired wirefeed mator.
speed
is
determined
by
the setting
of
the
wire speed potentiometer.
The proces5ed potentiometer wiper
v01
tage
is.
app1 ied
tcl
pin
3
of
the
cumparator
ICZ/l.
Components
IC2/3,
ICl/A
with
C7,
R22
and
R24
form
a
‘sample and
hald’ circuit whilctl
measures
the
back
e.m.f.
vu1
tage
of
the wirefeed
motor during th’e non-conducting periods
of
SCR’s
1
and
2.
This
v01
tage
is
applied
tu
the pin
2
input of the cumparator
IC2/1,
where
it
is
compared to the potentiometer wiper uol tage.
The
difference between these two uul tayec is amp1 ified
by
IC2/1
and
the resultant uoltage applied to the pin
6
input
sf
IC2/2,
where
it
is. compared
to
a
mains synchronized
rarr~p
waueform. The result of
this comparison determines the conduction angle of the
SCR’s
l
and
2,
and hence the motor speed.
The
ouer-all
effect
is
such that,
if
the
‘..peed
(hence back
em+)
of
the drive motor
falls
below the desired setting, the circuitry
act5
to irIcreac,e the ccrlducticln angle
c1.F
the
S.C:.H.’E.
and hence the
motor
speed.
If
the motor
speed
is
above the desired setting, the reverse
occurs.
When the
gun
switch
is
released, the
gas
value and mator
relay
(K1)
are immediately de-energised. The contacts
sf
K1
are
50
arranged
that
a
low value re~.istor is now connected acru~.~, the motor
terminals, providing dynamic braking of the motor armature. The
charge
stored on capacitor
C2
resu1
t5
in tranc,ic,tor
HI
continuing
tu
conduct
for
a
short time after the release of the gunswi tch.
Therefore, relay
K2
rerrlains energised for
a
similar period,
so
holding the welding power source contactor energised. This is known
as.
the ’burn-back’ period, and
it
functions
tu
prevent the welding
wire ’freezing‘ in the weld pool
at
the completion
of
a
weld.
The
burn-back time
is
adjusted
by
means
of
potentiometer
RU1.