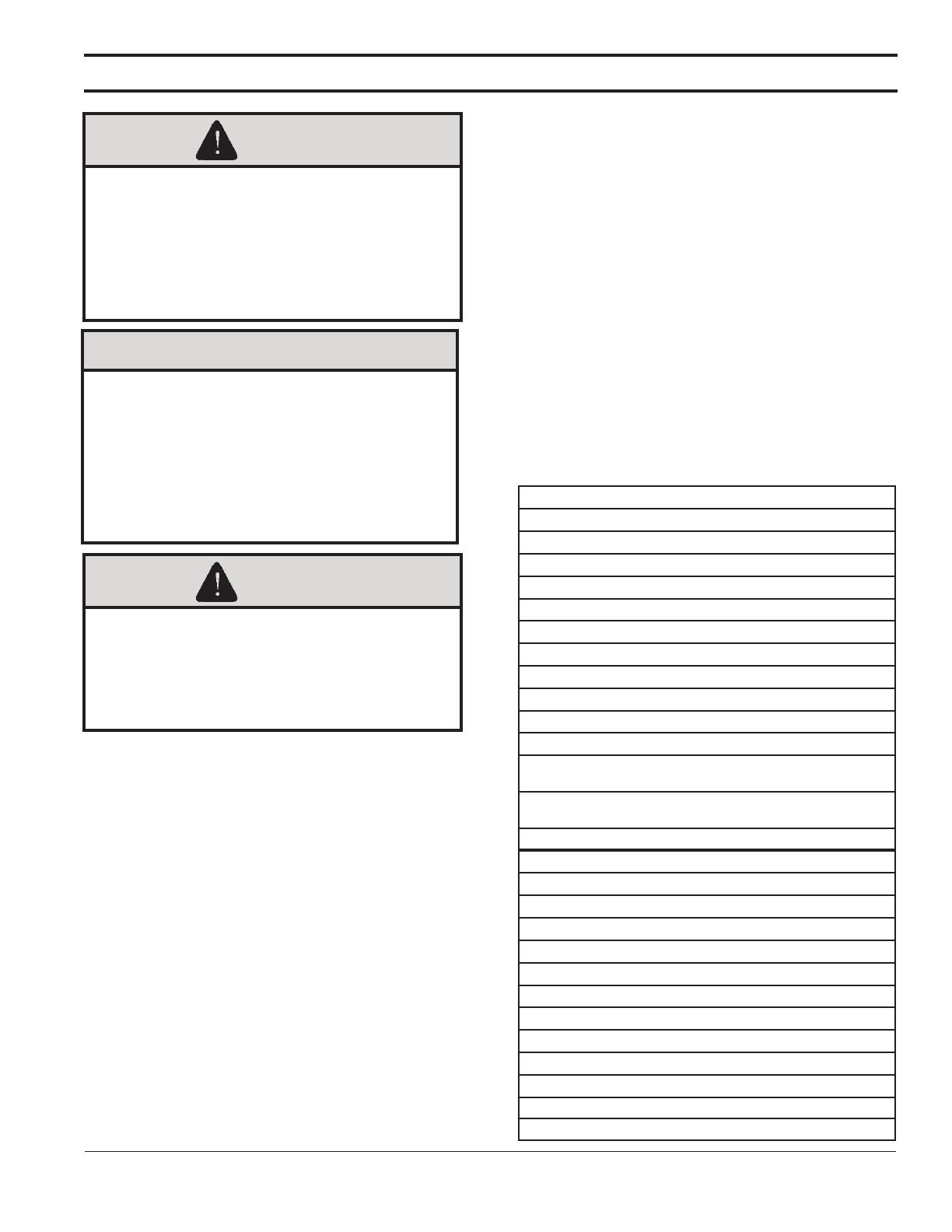
11
106309-03 - 4/19
WARNING
Explosion Hazard. Asphyxiation Hazard.
Electrical Shock Hazard. Installation of this
boiler should be undertaken only by trained
and skilled personnel from a qualied service
agency. Follow these instructions exactly.
Improper installation, adjustment, service,
or maintenance can cause property damage,
personal injury or loss of life.
NOTICE
Due to the low water content of the boiler, mis-
sizing of the boiler with regard to the heating
system load will result in excessive boiler
cycling and accelerated component failure.
Velocity Boiler Works, LLC DOES NOT warrant
failures caused by mis-sized boiler applications.
DO NOT oversize the boiler to the system.
Multiple boiler installations greatly reduce the
likelihood of boiler oversizing.
WARNING
Asphyxiation Hazard.
Apply supplied dielectric grease to gasket
inside vent connector. Failure to apply the
grease could result in ue gas leaks from gasket
rupture during vent pipe installation or gasket
deterioration due to condensate exposure.
A. Installation must conform to the requirements
of the authority having jurisdiction in or, in the absence
of such requirements, to the National Fuel Gas Code,
ANSI Z223.1/NFPA 54, and/or Natural Gas and
Propane Installation Code, CAN/CSA B149.1.
Where required by the authority having jurisdiction, the
installation must conform to the Standard for Controls
and Safety Devices for Automatically Fired Boilers,
ANSI/ASME CSD-1.
B. Boileriscertiedfor installation on combustible
ooring. Do not install boiler on carpeting.
C. Provide clearance between boiler jacket and
combustible material in accordance with local re
ordinance. Refer to Figure 4 for minimum listed
clearances from combustible material. Recommended
service clearance is 24 in. (610 mm) from left side,
front, top and rear of the boiler. Recommended front
clearance may be reduced to the combustible material
clearance providing:
1. Access to boiler front is provided through a door or
removable front access panel.
2. Access is provided to the condensate trap located
underneath the heat exchanger.
3. Access is provided to thermal link located at boiler
rear.
D. Protect gas ignition system components
from water (dripping, spraying, rain, etc.) during
boiler operation and service (circulator replacement,
condensate trap, control replacement, etc.).
E. Provide combustion and ventilation air in
accordance with applicable provisions of local building
codes, or: USA - National Fuel Gas Code, ANSI
Z223.1/NFPA 54, Air for Combustion and Ventilation;
Canada - Natural Gas and Propane Installation Code,
CAN/CSA-B149.1, Venting Systems and Air Supply for
Appliances.
Contaminants to avoid:
Spray cans containing chloro/uorocarbons (CFC’s)
Permanent wave solutions
Chlorinated waxes/cleaners
Chlorine-based swimming pool chemicals
Calcium chloride used for thawing
Sodium chloride used for water softening
Refrigerant leaks
Paint or varnish removers
Hydrochloric acid/muriatic acid
Cements and glues
Antistatic fabric softeners used in clothes dryers
Chlorine-type bleaches, detergents, and cleaning solvents found
in household laundry rooms.
Adhesives used to fasten building products and other similar
products
Excessive dust and dirt
Areas likely to have contaminants:
Dry cleaning/laundry areas and establishments
Swimming pools
Metal fabrication plants
Beauty shops
Refrigeration repair shops
Photo processing plants
Auto body shops
Plastic manufacturing plants
Furniture renishing areas and establishments
New building construction
Remodeling areas
Garages with workshops
Table 4: Corrosive Combustion Air Contaminants
and Sources
III. Pre-Installation and Boiler Mounting