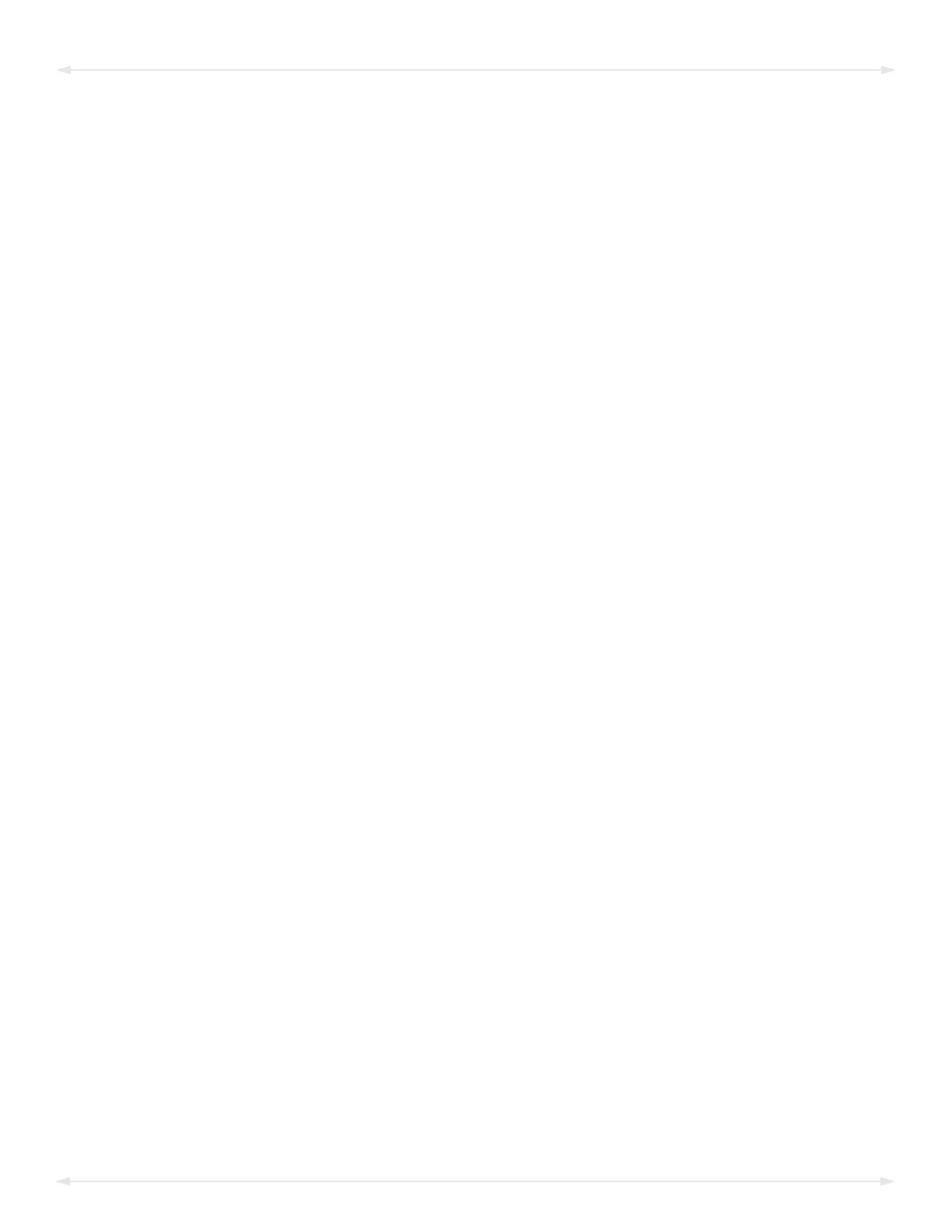
Rev 0.0/9-23 MTEX-DC3: #353041
SPECIFICATIONS .....................................................................................3
SAFETY...................................................................................................5
OPERATING FEATURES............................................................................6
MTEX-DC3 FEATURES..................................................................................6
INTELLI-GRIP® CONTROL UNIT FEATURES .........................................................7
ASSEMBLY..............................................................................................8
TO CHANGE THE PAD FRAME CONFIGURATION ................................................10
Repositioning (or Removing) Movable Pad Mounts .........................................................12
Repositioning (or Removing) the Sliding Pad Arms...........................................................13
Removing and Installing Pad Frame Tubes........................................................................14
Connecting/Disconnecting Vacuum Hoses .......................................................................19
TO INSTALL THE OPTIONAL ROOF PANEL KIT ...................................................20
INTENDED USE .....................................................................................26
LOAD CHARACTERISTICS...............................................................................26
ALLOWABLE OVERHANG ..............................................................................27
INDIRECT LOADING .....................................................................................27
OPERATING ENVIRONMENT..........................................................................28
DISPOSAL OF THE LIFTER .............................................................................28
OPERATION..........................................................................................29
BEFORE USING THE LIFTER...........................................................................29
Taking Safety Precautions .................................................................................................29
Selecting a Screen Language.............................................................................................29
Performing Inspections and Tests .....................................................................................30
Checking the 12-Volt Battery ............................................................................................30
Preparing to Use the Remote Control System ..................................................................31
TO ATTACH THE PADS TO A LOAD ..................................................................32
Positioning the Lifter on the Load.....................................................................................32
Powering up the Lifter ......................................................................................................34
Sealing the Pads on the Load............................................................................................34
Reading the Vacuum Gauges ............................................................................................35
TO LIFT AND MOVE THE LOAD......................................................................36
Interpreting the Lift Light..................................................................................................36
Monitoring Vacuum Indicators .........................................................................................36
TABLE OF CONTENTS