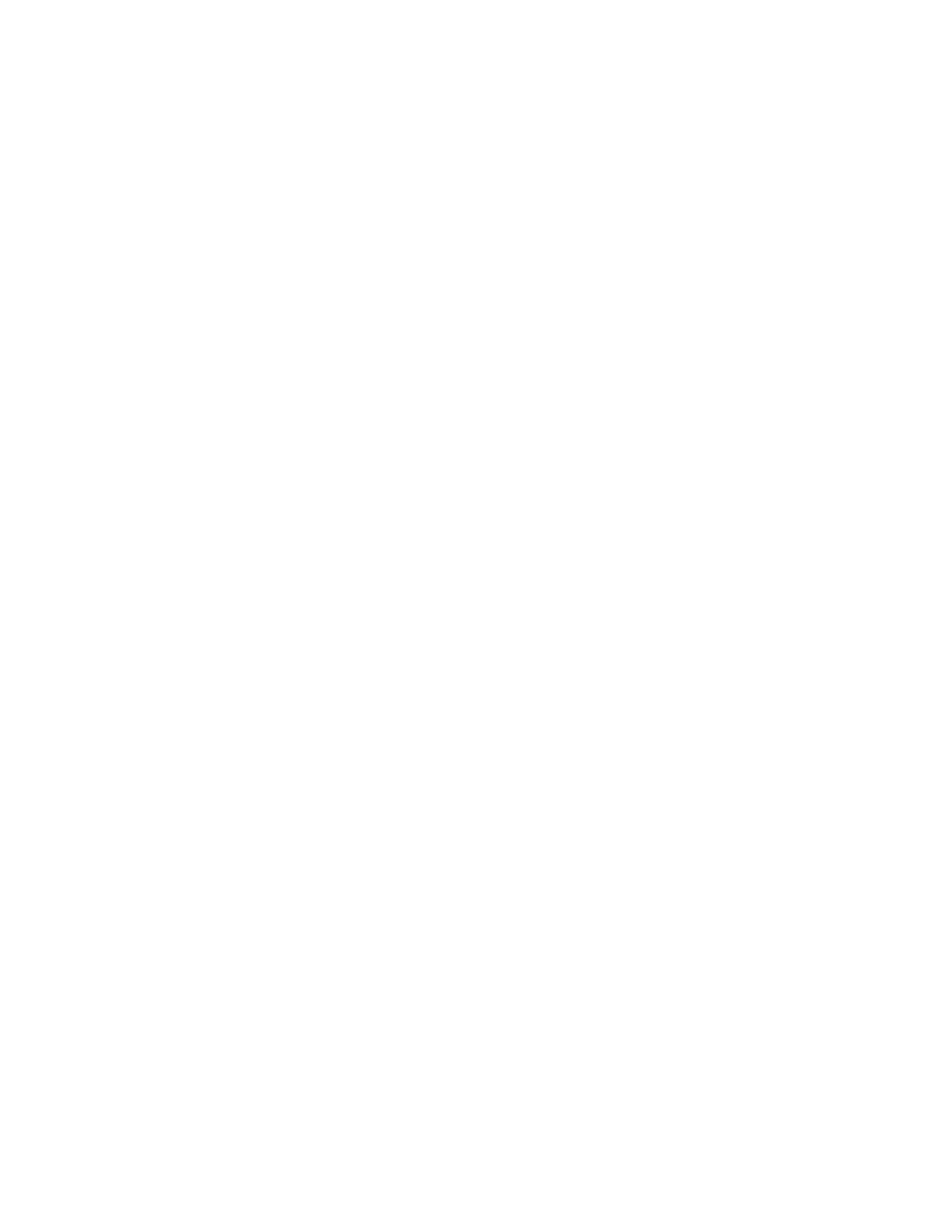
INSTALLATION INSTRUCTIONS FOR LWS LONGITUDINAL SEAM WELDERS
Initial Inspection
Upon receipt of the equipment, examine the shipping crate for freight damage. If the crate appears to have suffered
major damage, contact the shipping company. Once the unit is unpacked carefully examine the contents for
possible damage or possible misalignment in the track and mandrel.
Check that all the items, packages, or individual boxes have been received.
Although Miller Welding Automation packages your equipment with great care, long or extremely rough shipping can
adversely affect the equipment. As a result, please spend a few extra minutes to insure that the assembly pieces are
in good order.
The crate in which the seam welder has arrived will have to be dismantled. Be careful to dismantle the equipment
safely. Damage to the unit and personal injury can occur during unpacking, therefore follow all safety precautions.
Your seam welder was thoroughly tested and verified it met specifications before shipping. After receipt, visual
inspection of all adjustment points should be made. See Figure 1.
If a cable carrier assembly was purchased as an option, the carrier may have been removed from the track and
packed separately. Verify that it has arrived in good condition before proceeding with its installation.
The carriage assembly is normally shipped mounted on the track and requires only the removal of the temporary
mounting bracket. If the seam welder has an optional riser (for larger diameters than standard) the carriage may have
been removed before the seam welder was shipped. If this is the case, the carriage will be mounted on the crate deck
next to the seam welder. Verify there is no apparent damage to it or to the equipment mounted to it.
After this initial inspection is completed, installation of the longitudinal seam welder can begin.
Installation Guide
System Operating Conditions:
This system is designed for use in an industrial building.
Operating Conditions
Temperature range: 0 to 40C
Humidity: 5 to 95% RH non condensation
Altitude: Up to 1000 meters
Mounting: Secured to reinforced concrete floor
Electrical Input: 400VAC, 3 phase, 50 Hz nominal for export and 460 VAC, 3 phase 60 Hz domestic USA
Single Phase, 220VAC, 50 Hz for export and 120VAC, 60 Hz domestic USA
Compressed Air: Clean, dry air at 80 PSI (5.6 kg/sq cm)
Welding Gas: Bottled or bulk supply at 100 PSI (7 kg/sq cm) minimum pressure
Transportation, Storage: -20 C Degrees to 60 C Degrees
Vibration, Shock: 1G rms 5 to 500 Hz