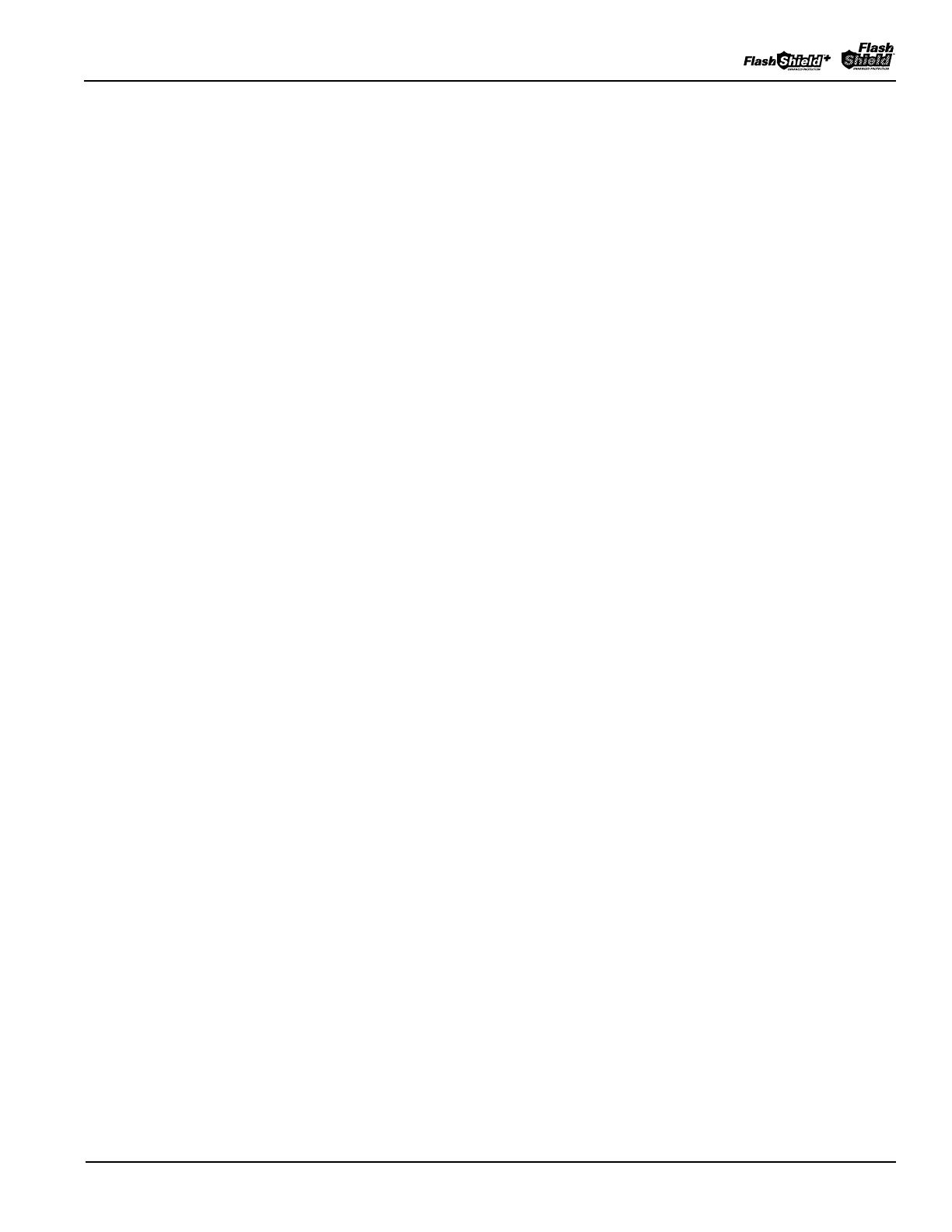
GASTITE DIVISION, TITEFLEX CORPORATION / 1116 Vaughn Parkway / Portland, TN 37148
iii
SECTION 1.0 INTRODUCTION
1.1 GENERAL USER WARNINGS ............................................................................................................. 1
1.2 LIMITATIONS OF THE GUIDELINES .................................................................................................. 3
1.3 STANDARDS, LISTINGS AND CODES ................................................................................................ 3
SECTION 2.0 SYSTEM DESCRIPTIONS & COMPONENTS
2.1 SYSTEM DESCRIPTIONS .................................................................................................................... 4
2.1.2 FLASHSHIELD™ SYSTEM DESCRIPTION ......................................................................................................... 4
2.1.3 FLASHSHIELD+™ SYSTEM DESCRIPTION ...................................................................................................... 5
2.2 COMPONENTS .................................................................................................................................. 6
2.2.1 CORRUGATED STAINLESS STEEL TUBING .................................................................................................. 6–7
2.2.2 FITTINGS ................................................................................................................................................... 8–9
2.2.3 MANIFOLDS ................................................................................................................................................ 10
2.2.4 MODULAR STUB SYSTEM ........................................................................................................................... 10
2.2.5 MOUNTING HARDWARE ..............................................................................................................................11
2.2.6 PIPE SUPPORT SYSTEM .................................................................................................................................11
2.2.7 STRIKE PROTECTION ................................................................................................................................... 12
2.2.8 SHUT-OFF VALVES AND QUICK CONNECTS ............................................................................................... 12
2.2.9 TOOLS ......................................................................................................................................................... 13
2.2.10 BONDING CLAMPS .................................................................................................................................... 13
2.2.11 SYSTEM IDENTIFICATION........................................................................................................................... 13
2.2.12 LINE REGULATORS ..................................................................................................................................... 14
SECTION 3.0 SYSTEM CONFIGURATION
3.1 CONFIGURATION............................................................................................................................ 16
3.1.1 INTRODUCTION ........................................................................................................................................... 16
3.1.2 SYSTEM REQUIREMENTS ............................................................................................................................ 16
3.1.3 REFERENCE DATA FOR PROPER SYSTEM SIZING .......................................................................................... 16
3.1.4 DETERMINING SYSTEM LAYOUT .............................................................................................................17-18
3.1.5 ALLOWABLE PRESSURE DROP ..................................................................................................................... 19
3.1.6 SIZING METHODS ................................................................................................................................... 19-20
3.1.7 MODIFYING AN EXISTING SYSTEM ............................................................................................................. 20
3.2 SIZING PROCEDURES AND EXERCISES .......................................................................................... 20
3.2.1 SIZING EXAMPLES ....................................................................................................................................... 20
3.2.2 EXAMPLE 1: SERIES SYSTEM – 6"WC ................................................................................................... 21–22
3.2.3 EXAMPLE 2: PARALLEL SYSTEM – 6"WC .............................................................................................. 23–24
3.2.4 EXAMPLE 3: PARALLEL SYSTEM – 12-14"WC ....................................................................................... 25–26
3.2.5 EXAMPLE 4: DUAL PRESSURE SYSTEM – 2 PSI TRUNK AND 8"WC APPLIANCE RUNS .......................... 27–28
3.2.6 EXAMPLE 5: MULTIPLE MANIFOLD SYSTEM .......................................................................................... 29-30
3.2.7 EXAMPLE 6: SERIES SYSTEM – 7"WC - HYBRID ..................................................................................... 31-32
3.2.8 EXAMPLE 7: PARALLEL SYSTEM – 7"WC – HYBRID .............................................................................. 33–34
3.2.9 EXAMPLE 8: SUMMATION METHOD FOR PARALLEL SYSTEM – 7"WC – HYBRID ................................. 35–36
3.2.10 EXAMPLE 9: SUMMATION METHOD FOR SERIES SYSTEM – 6"WC .................................................... 37–39
3.2.11 EXAMPLE 10: COMMERCIAL ELEVATED PRESSURE SERIES SYSTEM – 2 PSI.........................................40– 41
SECTION 4.0 INSTALLATION PRACTICES
4.1 GENERAL PROVISIONS ................................................................................................................... 42
4.2 FIELD FITTING ASSEMBLY PROCEDURE ......................................................................................... 43
4.2.1 XR3 FITTING TO FLASHSHIELD+ CSST ................................................................................................... 43–44
4.2.2 XR3 FITTING TO FLASHSHIELD CSST ......................................................................................................45-46
4.2.3 XR3 FITTING TO FLASHSHIELD CSST (WITHOUT STRIPPING TOOL) ........................................................47-48
4.2.4 OTHER ACCESSORY INSTALLATION ............................................................................................................ 49
4.3 ROUTING ........................................................................................................................................ 50
4.3.1 VERTICAL RUNS .......................................................................................................................................... 50
4.3.2 HORIZONTAL RUNS ..................................................................................................................................... 50
4.3.3 INSTALLATION CLEARANCE HOLES ............................................................................................................ 50
4.3.4 CONCEALED FITTINGS ................................................................................................................................ 51
4.3.5 MODIFICATIONS TO EXISTING SYSTEMS .................................................................................................... 51
4.3.6 OUTDOOR ................................................................................................................................................... 52